Increasing the sustainability of EV with ultrasonics
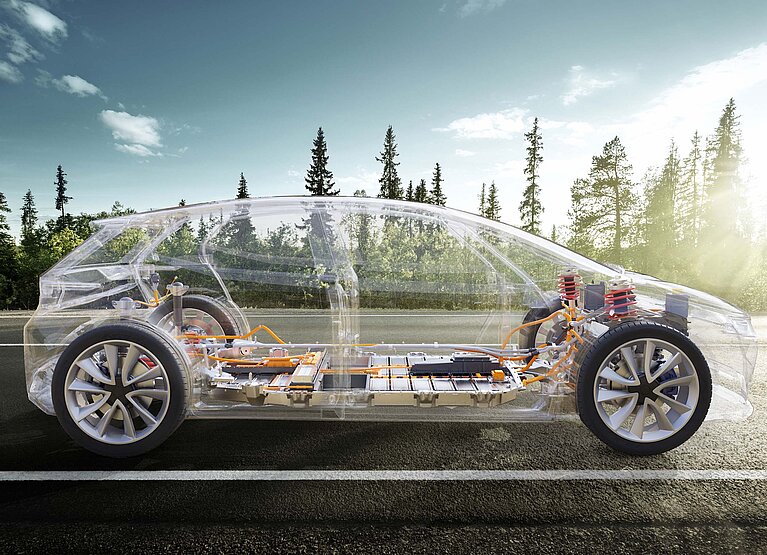
Saving energy, materials, and rejects
Sustainability becomes particularly interesting for companies when combined with cost savings. However, is that possible in the production of electric vehicles? As a particularly efficient, safe, and material-friendly process, ultrasonic welding offers some exciting options.
The production of vehicles with internal-combustion engines has undergone extensive optimization over the years; the mass production of electric vehicles is still in its early stages. This presents captivating opportunities for companies to enhance both production sustainability and cost-effectiveness.
One promising solution is the use of ultrasonic welding technology. When joining both plastic and metal applications, the process saves:
- Energy
- scrap
- raw materials
The technology becomes a promising link between sustainability and cost-effectiveness in the production of electric vehicles.
Saving up to 75 % energy with ultrasonics:
One of the most significant opportunities for energy savings lies in battery production. Traditionally, the sealing of pouch cells has been inefficient, often relying on thermal joining methods like heat sealing. However, these processes consume substantial amounts of energy and pose a risk of damaging the battery cell foils.
Based on experience from other industries, there is untapped potential here. Although ultrasonic sealing of pouch cells has not yet widely been implemented, it has successfully been used for sealing pouch packages in the food industry for many years. This process has demonstrated energy savings of up to 75% compared to conventional methods.
Using energy only where it is really needed:
The key to achieving energy savings lies in ultrasonic sealing, which differs from conventional processes. Unlike traditional methods, this technology does not rely on an external heat source. Instead, heat is generated internally within the materials through friction during the brief welding process, lasting only 100 to 200 milliseconds. This targeted approach ensures that energy is utilized only where necessary, eliminating any wastage between the welding tool and the application.
Another benefit is that the welding tools remain cool and ready for immediate use, eliminating the need for preheating, which saves additional energy, and thus, emissions.
Preliminary tests conducted in both the ultrasonic laboratory and production settings have confirmed that the experience gained from sealing pouch packaging can be effectively applied to the sealing of pouch cells. Given rising energy prices and rapidly growing demand for energy, savings becomes a major advantage for companies both ecologically and economically.
Saving resources with ultrasonics:
Alongside energy savings, reducing resource consumption plays a crucial role in enhancing the sustainability and cost-effectiveness of electric vehicle production. Ultrasonic welding facilitates a substantial reduction in resource consumption in two ways:
- The reduction of scrap rates
- The elimination of additional adhesives
1. Consistently low scrap rates
As one of the most cost-intensive components of an electric vehicle, the battery is a particular focus when making production safer. It is also of particular importance in the sustainability balance sheet. With dwindling availability of rare earth materials such as cobalt or lithium and the costly recycling of used batteries makes responsible handling of raw materials critical.
Ultrasonic welding, known for its gentle joining process, significantly reduces the scrap rate during battery production. The generator can gather valuable data during the welding process through direct contact between the welding tools and materials. This data enables the visualization and optimization of welding parameters such as force, energy, and amplitude. By recording up to 150 parameters per weld, it becomes possible to minimize industry-standard scrap rates from up to 20 percent, to a single-digit percentage.
“Scrap is a highly problematic issue as it is avoidable and negatively impacts both the sustainability and efficiency of production. That is why we are focused on maximizing the safety of the welding process. In doing so, we protect the environment and preserve valuable materials," explains Markus Haas, Global Sales Director METALS, emphasizing the commitment to creating a safe and sustainable production environment.
2. No more additives needed
Many plastic applications in electric vehicles still rely on adhesives due to the relatively low investment costs of the technology. However, the chemicals present in adhesives can have adverse environmental effects during production and disposal. Furthermore, adhesives often demand increased energy input, such as heating or drying, to ensure their efficacy.
The utilization of these chemicals not only affects the sustainability aspect but also contributes to ongoing cost factors. In recent years, the prices of raw materials have escalated, leading to a significant rise in costs associated with adhesive usage. Consequently, reducing reliance on such chemicals becomes imperative for both maintaining a favorable sustainability balance and managing expenses effectively.
Ultrasonic welding offers a distinct advantage as it eliminates the need for additional joining agents to achieve safe and permanent connections between applications. By using ultrasonic vibrations, the reliance on adhesives and the associated energy requirements are avoided.
Moreover, machines and production equipment that utilize adhesives require regular cleaning, resulting in downtime that decreases production efficiency. Adopting ultrasonic welding as a sustainable joining technology, not only is there a positive impact on the environmental balance sheet, but it also leads to a more streamlined and efficient production process.
Switching to sustainable materials:
The use of plastics in electric vehicles is on the rise, even though metals play a significant role in their construction. Whenever feasible, there is a push to replace metal applications with plastic alternatives. This shift is primarily driven by the multiple advantages that weight reduction through plastics offers:
- Improved Energy Efficiency: By reducing the overall weight of the vehicle with lightweight plastics, energy efficiency is enhanced. Electric vehicles can achieve better range and performance with reduced weight.
- Increased Battery Life: The lighter weight of the vehicle results in less strain on the battery, allowing for extended battery life and improved longevity.
- Enhanced Handling and Maneuverability: Lighter vehicles with plastic components provide improved handling and maneuverability, contributing to a better driving experience for users.
- Reduced Manufacturing Costs: Plastics are often more cost-effective to produce and process than metals. The use of plastics can lead to lower manufacturing costs, contributing to overall cost savings in the production of electric vehicles.
Choosing the right material for plastic applications:
By choosing the right plastic, companies can make an important contribution to sustainable production. Plastic recyclates made of polypropylene (PP), polyethylene terephthalate (PET), polyethylene (PE), acrylonitrile butadiene styrene (ABS), polyvinyl chloride (PVC), and polystyrene (PS) are particularly suitable. Especially PP, PE, and PET offer great potential, as these plastics can already be recycled by type.
However, the utilization of recycled plastics presents new challenges for joining processes. Each recycling process affects the quality of the material and subsequently, its ability to weld. This factor becomes increasingly important when working with purer recyclates.
Initial welding tests conducted with 100 percent pure recycled PA 6.6 (polyamide) have demonstrated comparable results to conventional plastics in terms of appearance, density, and tensile strength. This indicates that recycled plastics can be a viable alternative, already applicable in numerous electric vehicle components. Although recycled plastic has often been more expensive than conventional plastic, advancements in recycling processes can quickly change this situation, making recycled plastics more cost-effective in the future.
Conclusion: Combining Sustainability with efficiency
To meet the increasingly stringent sustainability goals in electric vehicle production, companies must focus on improving efficiency and sustainability simultaneously. Fortunately, there are opportunities to combine sustainability and cost-effectiveness in various areas. Ultrasonic welding, in particular, presents exciting prospects for manufacturers in this regard.
Ultrasonic welding offers a safe and efficient process that can make a significant impact on reducing energy consumption and scrap rates. It also enables the secure joining of more sustainable materials, including recycled plastics. These factors play a crucial role in reducing emissions and preserving critical resources.
To achieve these benefits, companies need to collaborate with experienced ultrasonic welding partners who can assist in developing efficient welding processes. Collaboration will ensure a safe, efficient, and sustainable production process that simultaneously reduces production costs.
By embracing ultrasonic welding technology and fostering partnerships, companies can make strides toward achieving their sustainability goals while enhancing cost-effectiveness in the production of electric vehicles.