31. March 2025
, News
Manufacturing adhesive-free hygiene products with ultrasonics
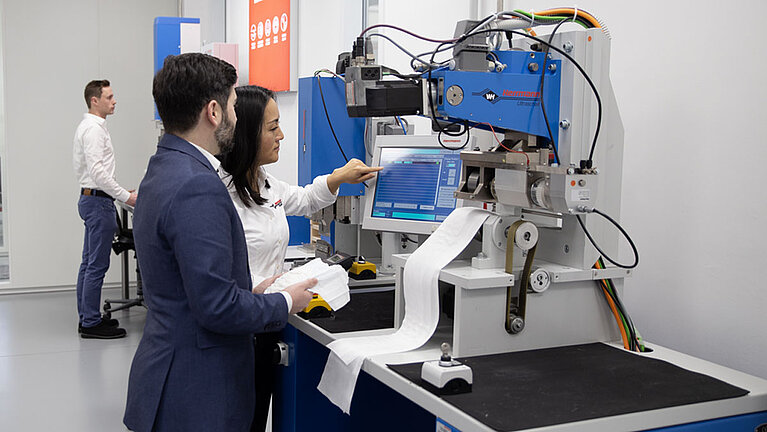
Manufacturers of hygiene products such as diapers are constantly under pressure to reduce costs while delivering high-quality products. One effective long-term method of meeting these requirements is to use ultrasonic bonding instead of conventional adhesives. This efficient joining method offers significant advantages in terms of cost savings, efficiency, and sustainability.
Ultrasonics bonding technology enables manufacturers to produce diapers without the use of adhesives, while also realizing significant savings in operational costs. This is mainly due to the following aspects:
The manufacturing costs of hygiene products can be permanently reduced without the use of additional adhesives. Companies can save up to 90% of operating costs by eliminating the purchase and transport costs of adhesives.
In addition, the costs of complying with the documentation guidelines required for chemicals are also eliminated. Reducing the number of consumables not only reduces costs, but also the space required in the warehouse.
Rejects can be a significant cost factor in the manufacturing of diapers and other hygiene products. Ultrasonic bonding can help to solve this issue: precisely controllable parameters such as welding time, energy, and frequency optimize the process to achieve consistent bonding results.
In the ultrasonic laboratory, these parameters can be defined individually for each application and tested under real production conditions. The result: minimal rejects and maximum efficiency.
With ultrasonic welding, manufacturers benefit from seamless, digital process control. During the welding process, valuable data is collected in real time. These data not only help to monitor process quality, but also to identify and eliminate potential error sources. This further reduces the number of rejects and increases the efficiency of diaper production.
Production losses or downtime can result in significant costs, especially in high-speed facilities such as those used to manufacture diapers.
Ultrasonic bonding helps to minimize these downtimes. Without the use of additional joining agents such as adhesives, time-consuming cleaning work is no longer necessary, nor are waiting times for chemicals to warm up.
It is also possible to switch between different applications by simply changing the welding program digitally. This means that the machine is back up and running in no time.
Switching to adhesive-free production methods such as ultrasonic bonding offers companies enormous potential for permanently reducing their costs. By eliminating the need for joining materials and the associated costs alone, up to 90% of operational costs can be reduced.
At the same time, the process optimizes the OEE of diaper production, making an important contribution to increasing the efficiency of the plant.
Learn more about the advantages of ultrasonic welding for diapers, femcare and other hygiene products in our free white paper: