Mask Task Force established
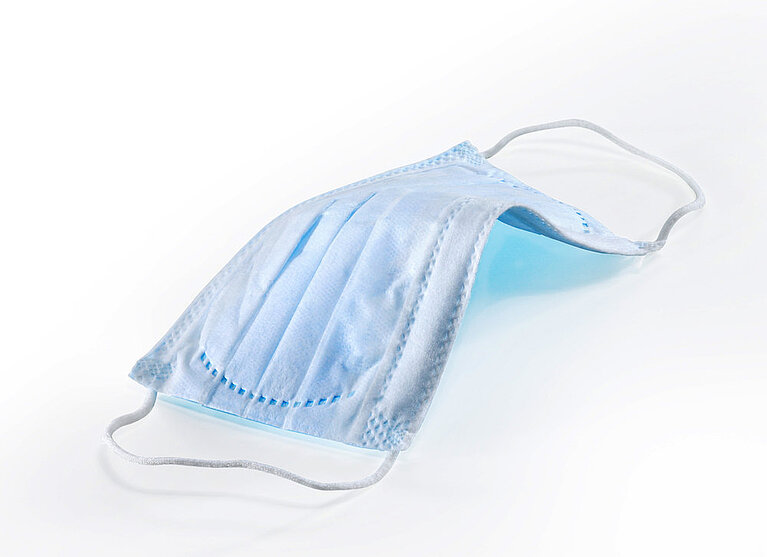
Focus on short transport distances
Herrmann Ultraschall supplies the ultrasonic welding technology for the production of different face masks. Inquiries accumulate. Focus on short transport distances.
Ultrasonic welding is a preferred technology for the production of respiratory masks made of nonwovens and demand increases worldwide. Herrmann Ultraschall is receiving multiple inquiries from medical technology customers who are expanding their existing production capacities and from hygiene customers who are switching from diaper to mask production. But also players from completely different sectors, such as the automotive industry, want to enter the market.
Herrmann Ultraschall has set up a mask task force to coordinate all efforts. Nine different mask types have been identified, says CEO Thomas Herrmann, ranging from simple face masks to complex 3D deep-drawn masks with breathing valves. The technological solutions range from simple intermittent manual welding to complex high-speed systems. The company offers products from standard machines and components to complex rotary ultrasonic welding modules to serve the different solutions, Herrmann explains further. Special shifts are worked in order to meet the high demand in a timely manner.
Since the majority of face masks still come from Asia, Herrmann Ultraschall also supports various European initiatives to shorten transport distances. These include the conversion of diaper machines - here, as at the Italian company Fippi in Milan, high output figures of up to 900,000 masks per day can be achieved. Herrmann is also in discussion with the Reifenhäuser Group for possible mask production in Germany.
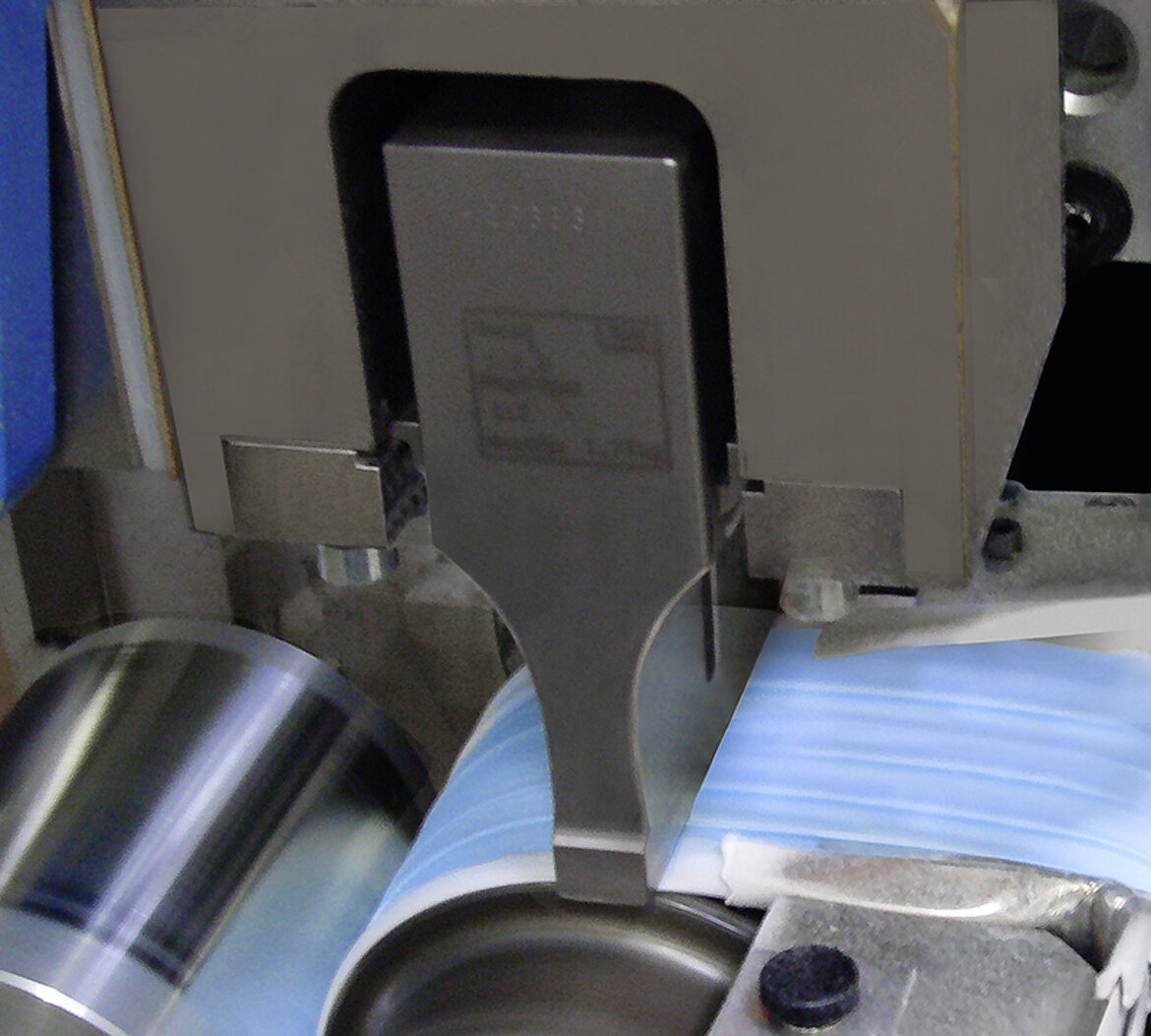