Customer Story KACO
For the sealing of a membrane in an emergency degassing system, KACO was looking for a precise and fast joining process. Thanks to the close cooperation, Herrmann Ultraschall was not only able to develop the ideal welding process for these specifications, but also to identify further areas of application for ultrasonic technology, making the manufacturing of the system even more efficient.
The challenge
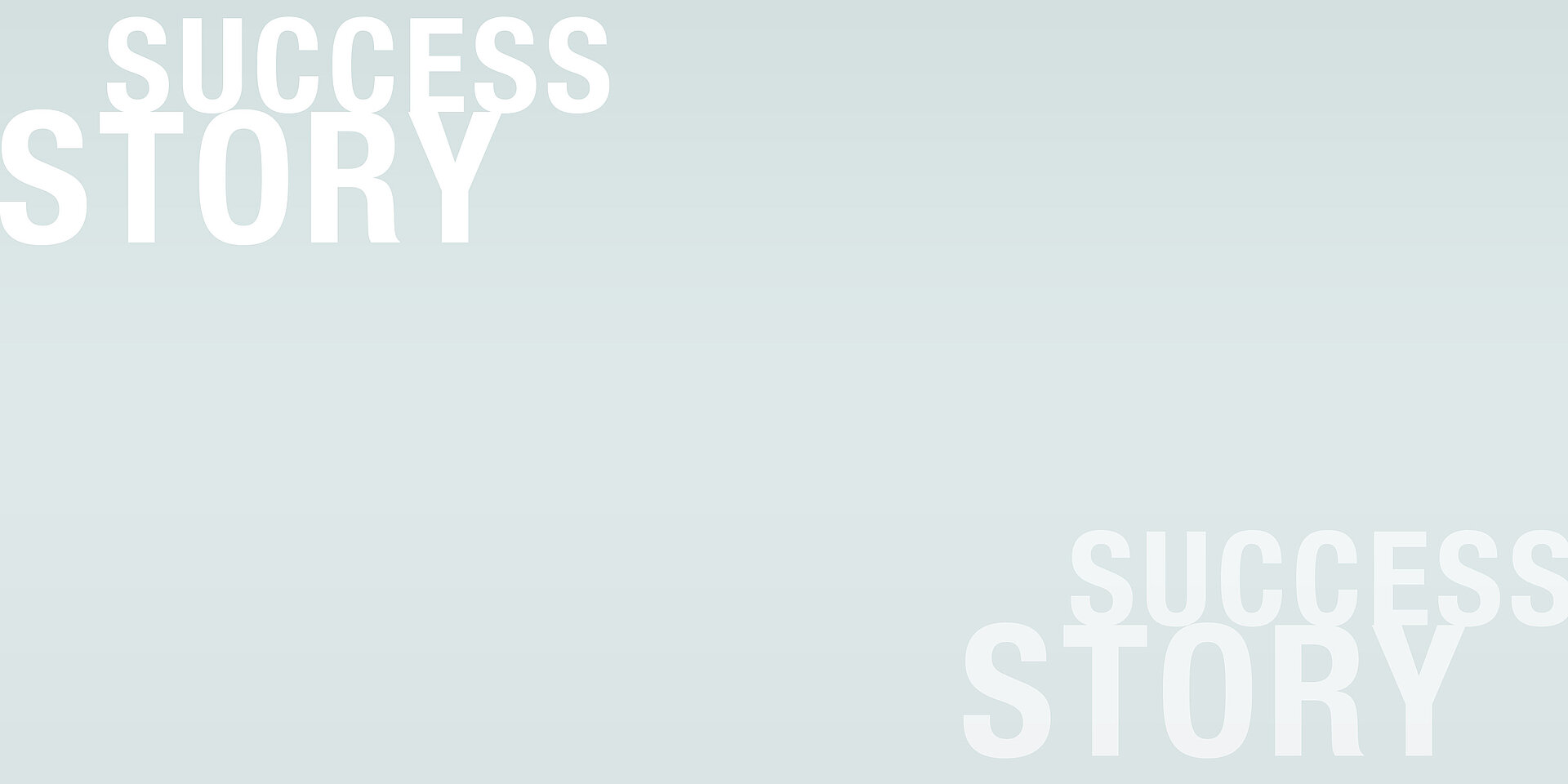
Despite its low weight and slight curvature, the membrane must be fitted exactly in the center of the housing. Since all the components of the application are precisely matched to one another, improper placement of the membrane can impair its functionality within the system.
Alternative joining methods, such as adhesive, were ruled out. It became apparent that this process would have made it difficult to center the membranes precisely due to deformation. In addition, the curing of the adhesive would have led to longer production times and the chemicals could have had a negative effect on the breathing capacity of the fine membrane.
Gentle
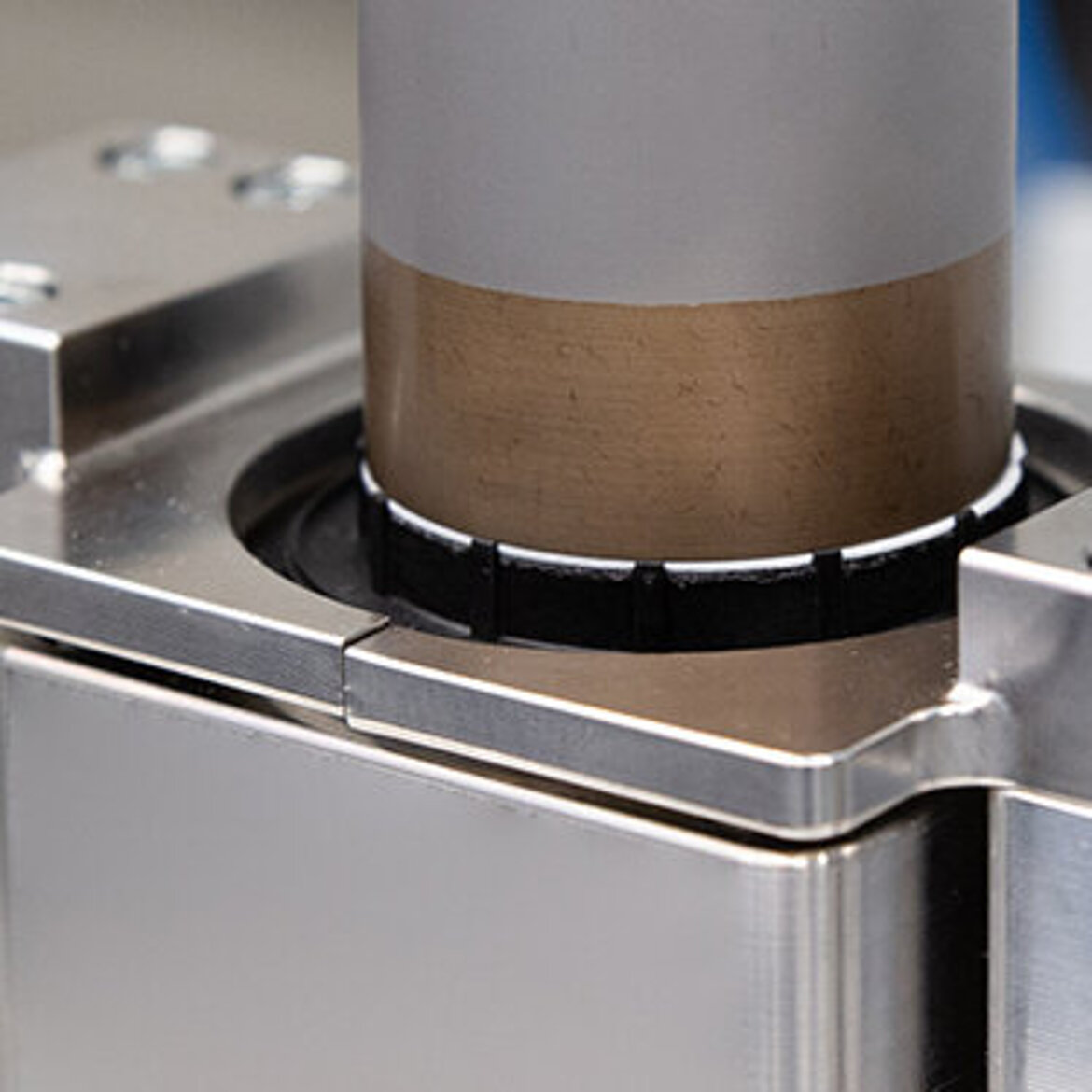
Ultrasonics can produce the desired connection without any joining agents, so that the material properties of the fine membrane are preserved.
Fast
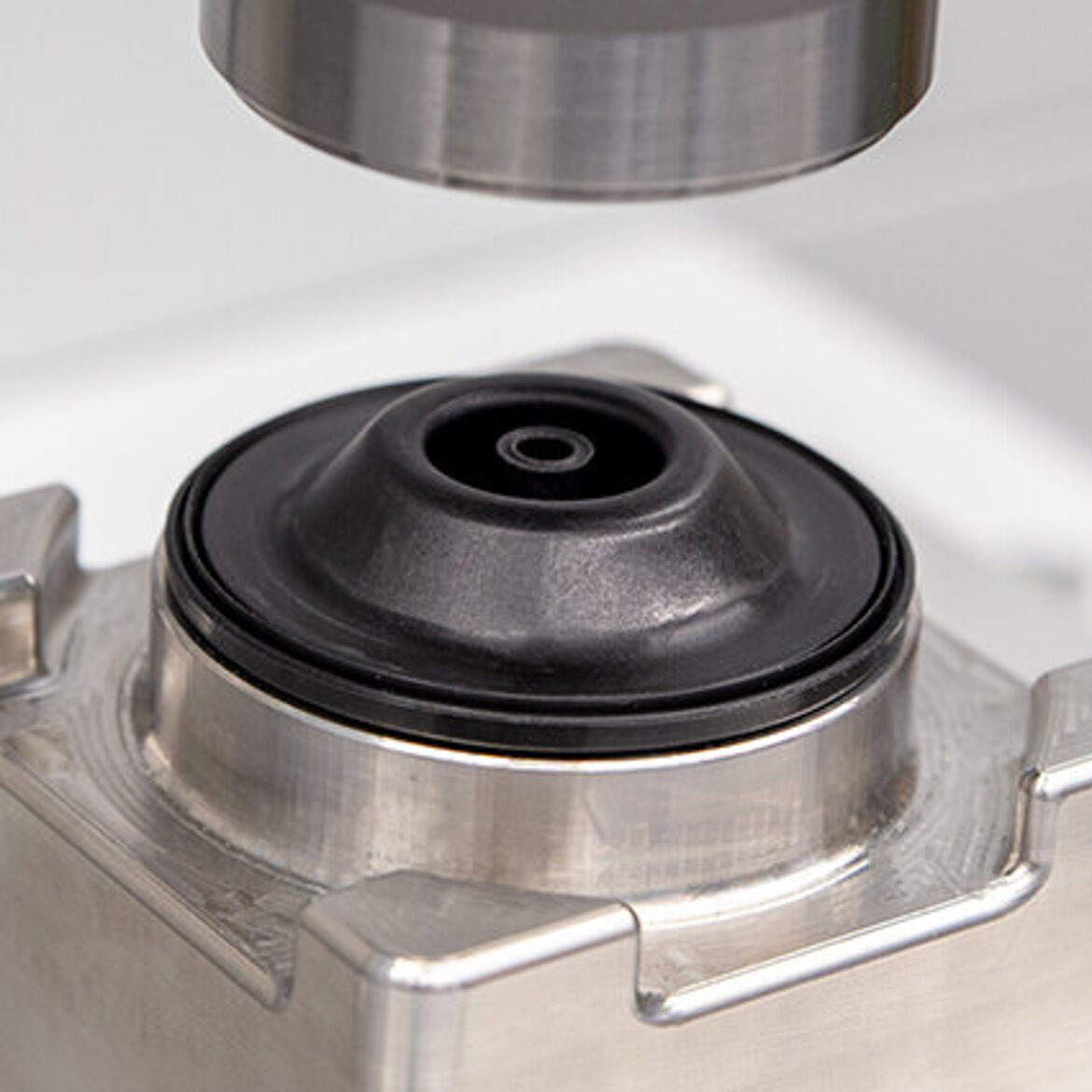
Minimal welding times ensure a smooth process that can be performed manually or automated.
Safe
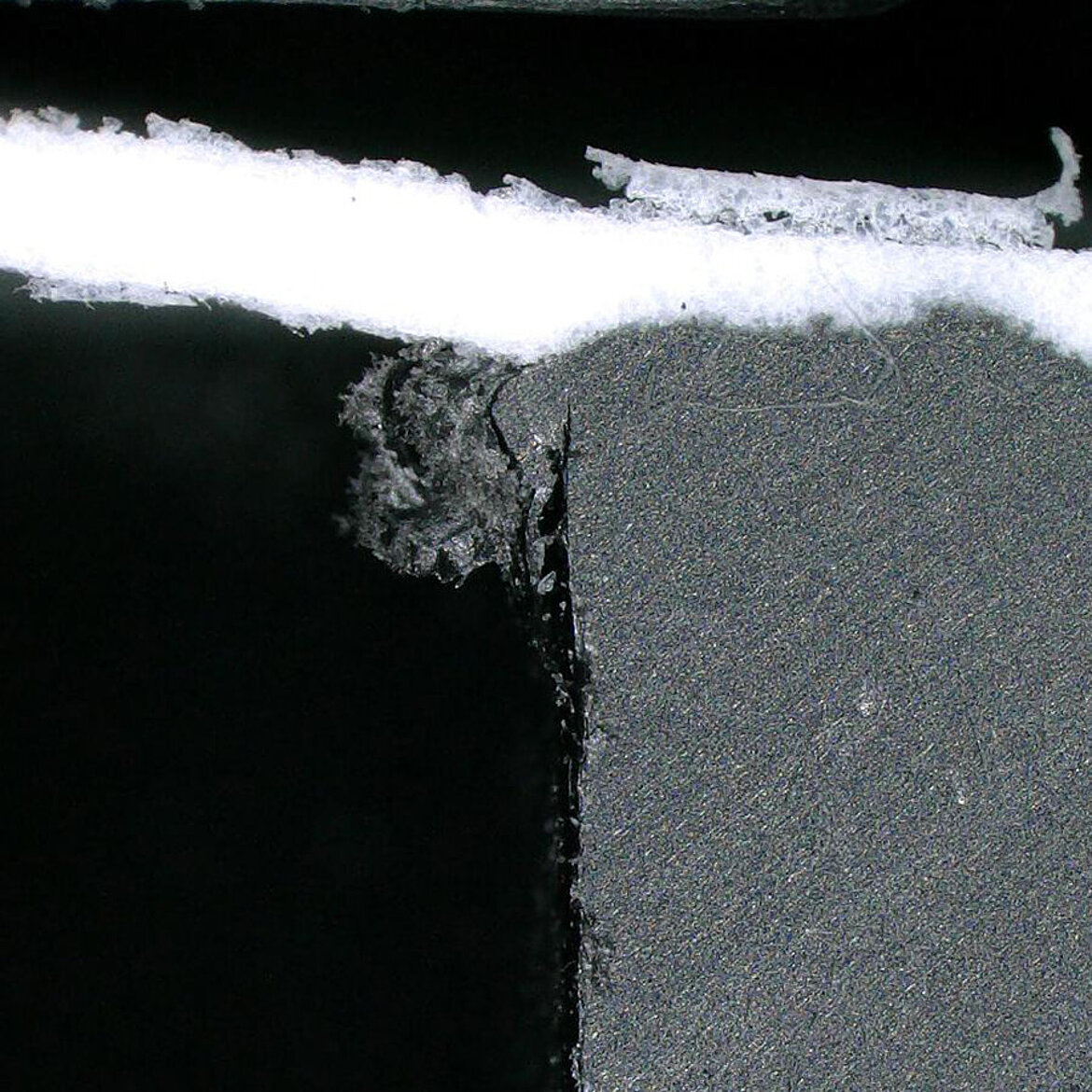
The first basic tests already showed that it was possible to produce a material-to-material connection between the membrane and the plastic housing.
Individual, pneumatic, safe
To ensure accurate centering of the joining partner in the application, a custom fixture has been developed and integrated into the workpiece holder. This makes it easier for the operator at the manual work station to position the membrane optimally for the welding process and prevents the joining partner from slipping.
For the welding tests, this fixture was still operated manually, but for mass production, it is to be controlled automatically via pneumatics.
The combination of such a custom fixture and adjustment of the welding parameters ensured an accurate seal of the membrane.
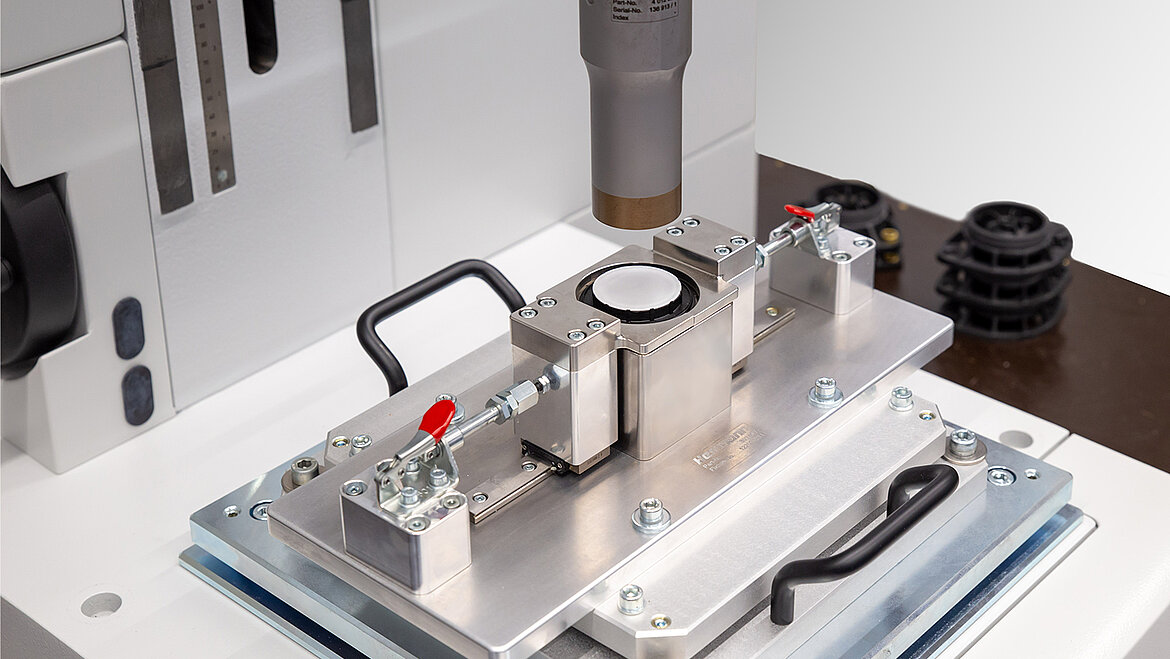
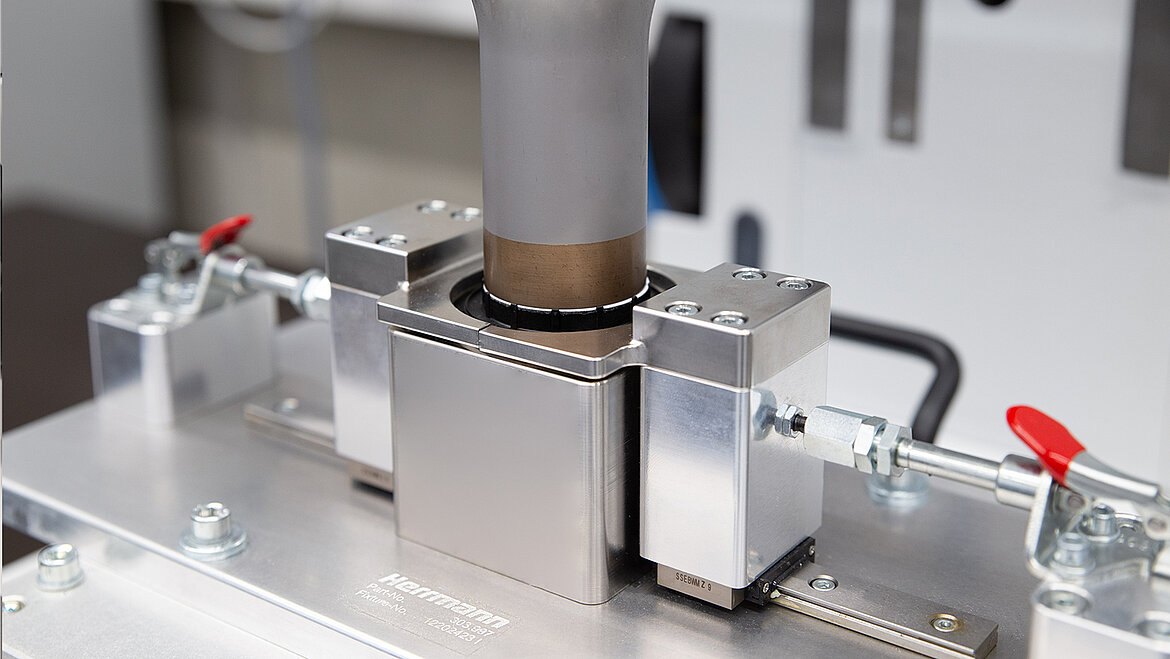
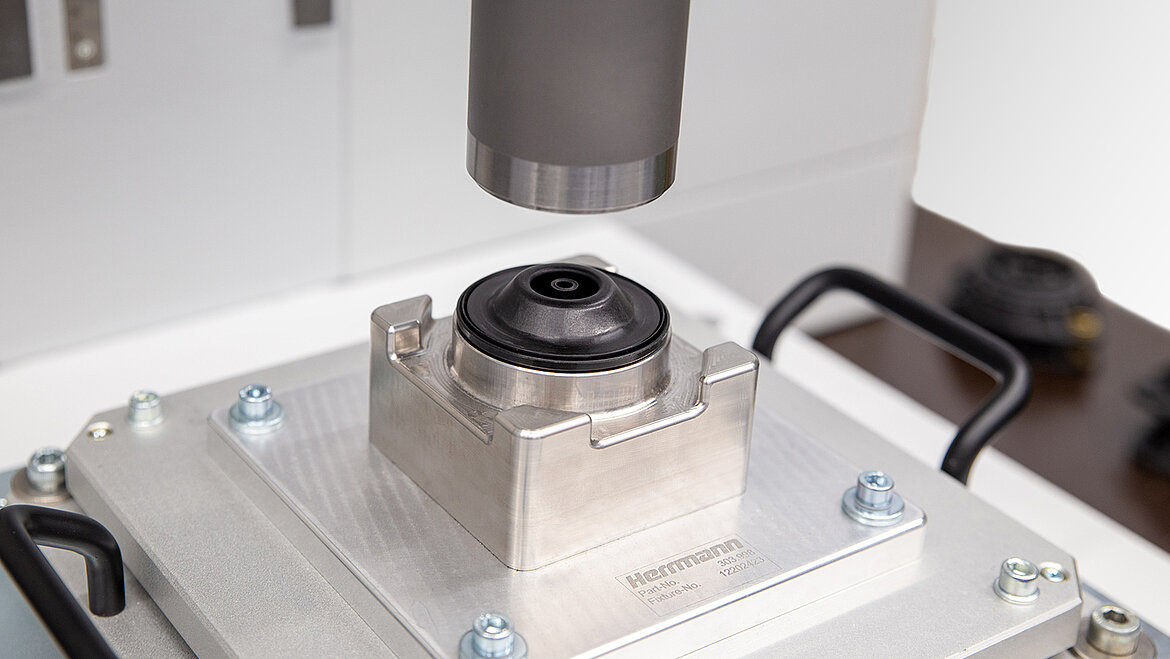
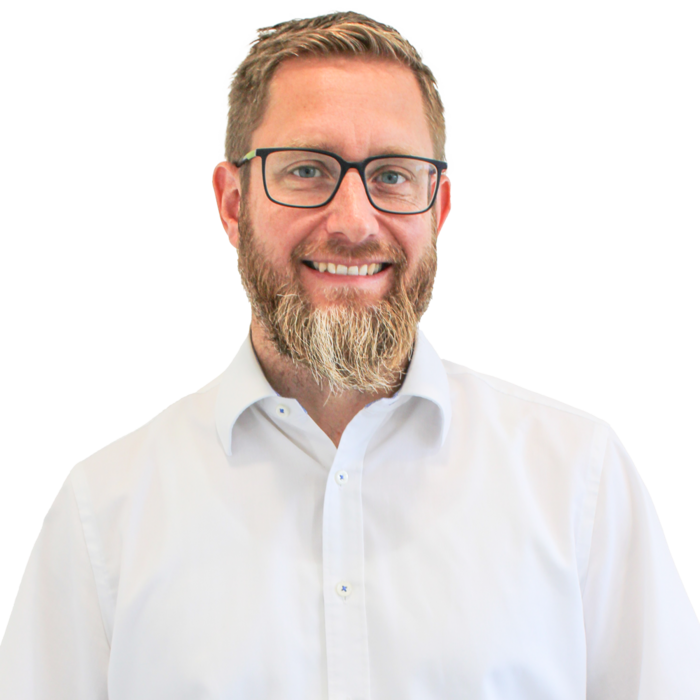
"For KACO, the battery vent is a new product with many challenges in the component design and the new manufacturing processes required for it.
We were therefore very glad to have found a partner in Herrmann Ultraschall who always provided us with competent support in the design of the necessary welding contours and the ultrasonic welding process, from the start of the project through various laboratory visits to series production."
Simon Kayser, Manager Advanced Engineering Processtechnology / Product KACO
Further application potential discovered
In addition to sealing the membrane, Herrmann's engineering team demonstrated other potential uses of ultrasonic technology that could contribute to fast and safe mass scale production of the application.
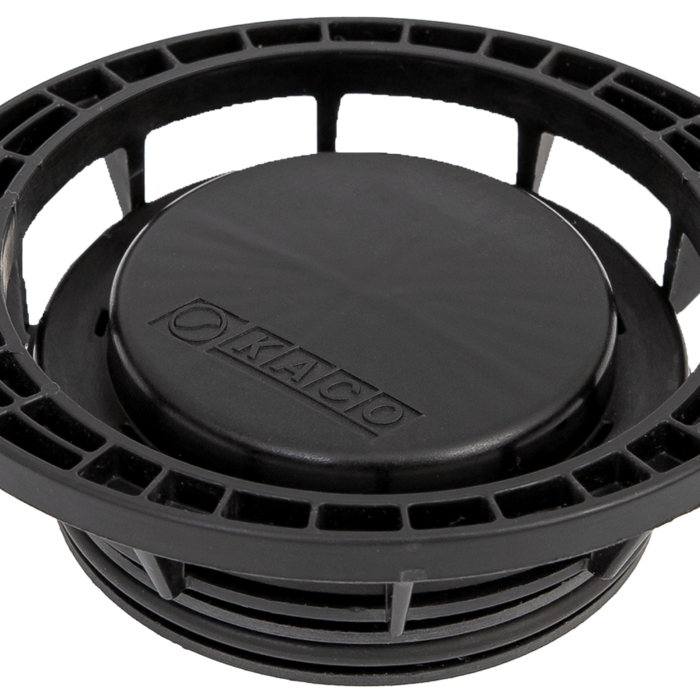
Welding of the plastic lid
Together, further welding processes were developed, for example to weld the plastic lid for the emergency degassing system onto the plastic housing with the sealed membrane. KACO attached great importance to a material-to-material connection between the two joining partners. This requirement was already implemented in the first welding tests in the laboratory.
Inserting the brass female connectors
To ensure the safety of the battery, four such newly developed emergency degassing systems are mounted per battery box. For this purpose, two female connectors per system are embedded in the plastic housing of the application. Since this process can also be realized with ultrasonics, KACO decided to rely on the reliable joining process here as well after consulting with the Herrmann Ultraschall team.
The inserting of female connectors with ultrasonics protects the material and simultaneously ensures a result with a perfect appearance.
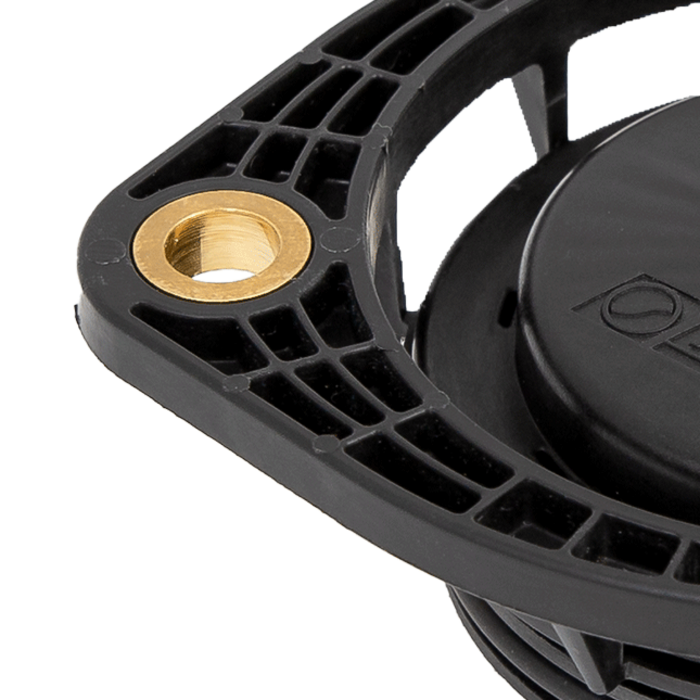
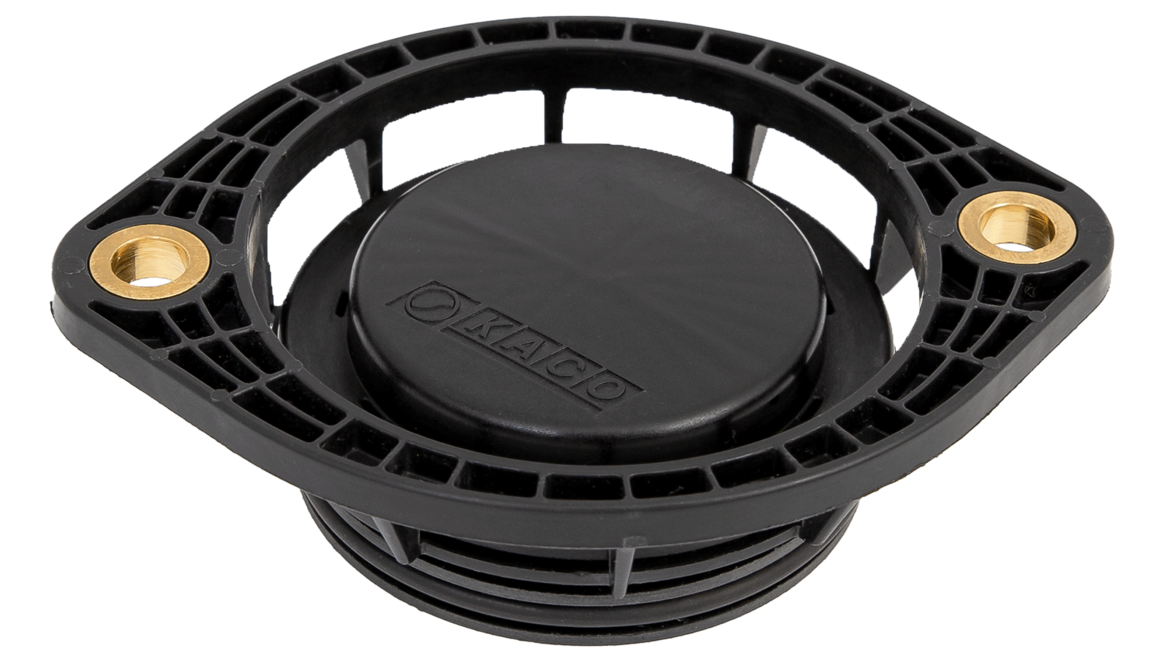
Close consulting opens up full ultrasonic potential
The joint welding project between KACO and Herrmann illustrates the versatility of ultrasonic welding technology. From sealing the membrane to welding two plastic components to inserting female connectors into the housing, the joining process offers enormous added value at every process step with precise, clean and fast connections.
The key is an experienced ultrasonic expert who can work closely with the customer to identify their needs and advise on the application of the joining technology. This enables the full potential of ultrasonic welding to be realized for economical and efficient mass production.
Photos: Herrmann Ultraschall
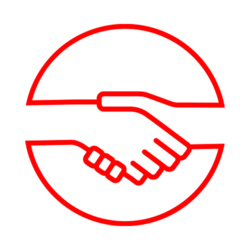
From the first ideal to the development of an application right up to process optimization, we will work out the best possible solution with you, hand-in-hand. We are convinced that we have the right experts and a great ultrasonic solution for every application.
Use our know-how and optimize your project too!