24. October 2024
, News
In the fast lane with ultrasonics
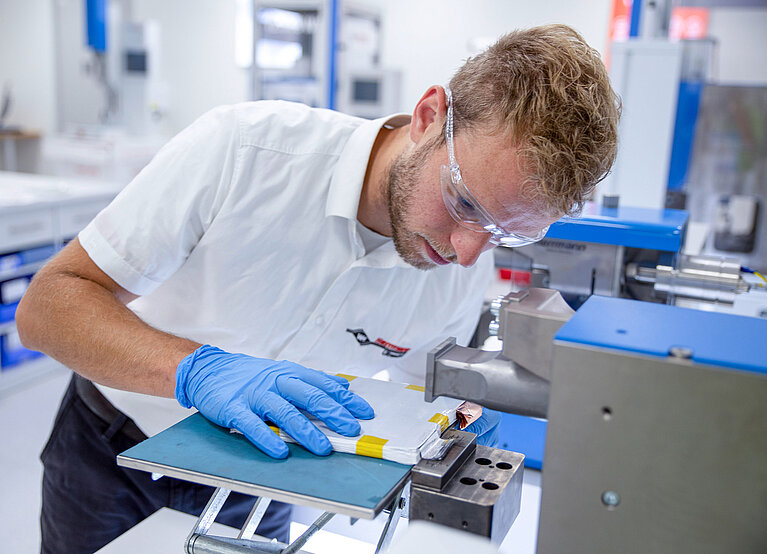
Minimal scrap rates with twice as fast cycle times: New developments in ultrasonic welding enable an optimization of production and can permanently reduce manufacturing costs for batteries and wire harnesses. A big help comes from the experience gained in the welding of plastics.
As the heart of electric vehicles, the battery cell plays a central role in the production. However, although the industry stands for progress, innovation and sustainability, many companies in the industry accept high reject rates – in some cases of up to 20 percent. Especially in times of long delivery times as well as material shortages, this is increasingly becoming a major cost factor. Thanks to a careful joining process, but also constant research in the ultrasonic laboratory, ultrasonic welding can make a decisive contribution to making production safer, more reliable and thus also more cost-efficient.
"Welding is usually used at the end of the battery production process. This means that if the joining process is failing, the entire battery cell has to be disposed of. For cost reasons, but also for sustainability reasons, this is not acceptable. That's why we looked for ways to help provide a safe and repeatable process – and found them," explains Michael Leipold, Business Unit Director Plastics and Metals at Herrmann Ultraschall.
For the reduction of reject rates, one tool in particular has proven its worth, which has already led to reject rates close to 0 percent in the ultrasonic welding of plastic parts: process visualization and monitoring. Each individual weld is monitored by intelligent control software that graphically displays the most important parameters such as welding force, amplitude, energy and joining distance in real time. In this way, potential for improvement can be identified, parameter settings optimized and the entire process can be continuously improved.
In total, up to 150 parameters per welding process can be recorded, stored and evaluated during ultrasonic welding of non-ferrous metals. And each welding has its own digital fingerprint, which ensures traceability. At the same time, this data forms a valuable basis for permanently low scrap rates and a reliable process.
The joining of battery cells with few foil layers or from thin materials is especially challenging. In order to be able to create strong connections in these applications without damaging the sensitive foils, extremely precise force control is required in a range of up to five newton at a frequency of 35 kHz.
In addition to an elaborate control system, it became clear that a corresponding addition to the hardware, i.e. the ultrasonic welding system, was necessary. Tests in the ultrasonic laboratory revealed that the development of a rocker is necessary to enable a stable process even with the lowest forces.
To ensure an ideal transfer of energy from or even into the battery, it requires strong connections to terminals and high-voltage cables with as little contact resistance as possible. Here, again, ultrasonic welding technology can deliver significant added benefit by creating connections without affecting the conductivity. As a result, no valuable energy is lost in the battery and wiring harness, which means that the range of the electric vehicle is not affected.
However, two challenges for ultrasonic welding technology appeared so far, especially for welding high-voltage cables made of aluminum and copper:
1. The cycle time
2. The increasing diameters of the cables
Both factors are closely related and are crucial for increasing production efficiency. Therefore, application engineers from the ultrasonic laboratories addressed these two points and developed corresponding solutions to optimize production conditions.
There is a supposedly simple solution to the increasing diameters of high-voltage cables. The thicker the cables, the more power is required – and the generators have to be more powerful. The generators have to produce up to 12,000 watts and welding forces of around 10,000 N to connect high-voltage cables with cross sections of 150 mm² and more.
However, such a high output also generates a corresponding amount of heat. To prevent damage to the converters, they require long cooling times. Therefore, the welding of high-voltage cables with terminals required 35 to 45 seconds.To reduce this time, application engineers at Herrmann Ultraschall developed a new, patented architecture for the converter, which converts the electrical voltage into mechanical vibrations. In the process, the heat generated is effectively conducted away, so that cooling times become almost completely obsolete. Cycle times can thereby be reduced to less than 20 seconds.
"In the future, automation will certainly play an increasingly important role in the welding of high-voltage cables. In this context, shorter cycle times are more crucial than ever," explains Michael Leipold and continues: "With high-performance converters that have already proven themselves in everyday production, we can realize this acceleration."
However, the comparatively long cycle times for welding high-voltage cables are also partly caused by the production conditions. That’s because most cables are welded at manual workstations; automated systems with ultrasonic technology are possible, but have so far been the exception.
In addition, one production often processes a large number of individual wire harnesses and types. However, most welding machines are only designed to process one size, so the worker has to change machines several times.
With a new type of quick-change system for Herrmann machines, valuable time can be saved. Welding tools or entire fixtures can be exchanged within a few minutes, allowing rapid application changes. The development of such quick-change systems focuses not only on speed but also on user-friendliness. This ensures that no time-consuming or cost-intensive errors occur. Modern welding machines therefore rely on clamping systems for exchanging sonotrodes, guaranteeing that they are automatically set correctly.
Key factors for the success of e-mobility include a long range, fast charging times and lower production costs. At these points, ultrasonic welding technology can make a significant contribution by:
Production costs can thus be reduced through a combination of intelligent control, a precise welding system and the generally gentle ultrasonic process with minimal heat stress on the material. Basically, the earlier the ultrasonic partner is involved in the project, the safer and more efficient the welding process can be designed.