24. Oktober 2024
, News
Auf der Überholspur mit Ultraschall
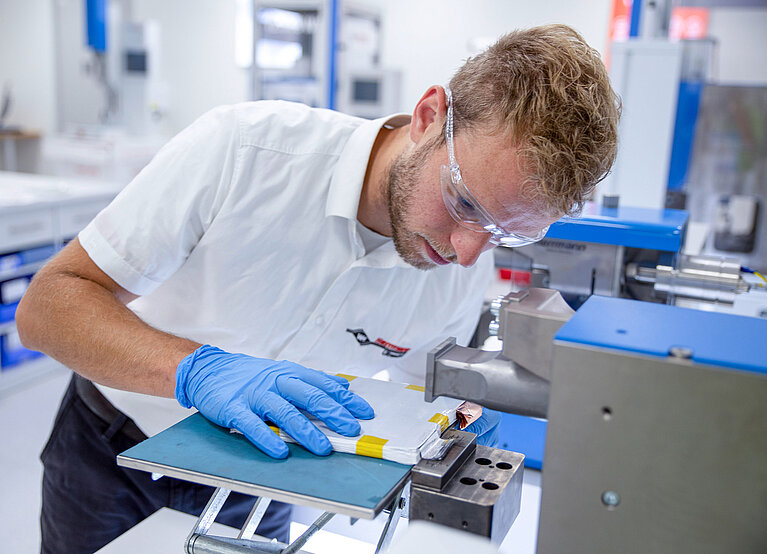
Minimale Ausschussraten bei doppelt so schnellen Taktzeiten: Neue Entwicklungen im Ultraschallschweißen ermöglichen eine Optimierung der Produktion und können damit dauerhaft die Herstellungskosten für Batterien und Kabelbäumen senken. Dabei helfen auch Erfahrungswerte aus dem Schweißen von Kunststoffen.
Als Herzstück von Elektrofahrzeugen spielt die Batteriezelle eine zentrale Rolle in der Produktion. Doch obwohl die Branche für Fortschritt, Innovation und insbesondere auch für Nachhaltigkeit steht, akzeptieren viele Unternehmen hohe Ausschussraten in diesem Bereich – teilweise von bis zu 20 Prozent. Insbesondere in Zeiten von langen Lieferzeiten sowie Materialengpässen wird das zunehmend zu einem großen Kostenfaktor. Dank eines schonenden Fügeprozesses, aber auch konstanter Forschung im Ultraschall-Labor kann das Ultraschallschweißen einen entscheidenden Beitrag dazu leisten, die Produktion sicherer, zuverlässiger und damit auch kosteneffizienter zu machen.
„Das Schweißen kommt in der Regel am Ende der Batterieproduktion zum Einsatz. Das heißt, dass bei fehlerhaften Prozessen die gesamte Batteriezelle entsorgt werden muss. Aus Kosten-, aber auch aus Nachhaltigkeitsgründen ist das nicht akzeptabel. Deshalb haben wir nach Wegen gesucht, die dazu beitragen, einen sicheren und reproduzierbaren Prozess zu bieten – und sie gefunden,“ erklärt Michael Leipold, Business Unit Director Plastics and Metals bei Herrmann Ultraschall.
Für die Reduzierung der Ausschussraten hat sich vor allem ein Mittel bewährt, das bereits beim Ultraschallschweißen von Kunststoffteilen zu Ausschussraten nahe den 0 Prozent geführt hat: die Prozessvisualisierung und -überwachung. Dabei wird jede einzelne Schweißung von einer intelligenten Steuerungssoftware überwacht, die die wichtigsten Parameter wie Schweißkraft, Amplitude, Energie und Fügeweg grafisch in Echtzeit darstellt. So können Verbesserungspotenziale erkannt, Parametereinstellungen optimiert und damit der gesamte Prozess kontinuierlich verbessert werden.
Insgesamt können beim Ultraschallschweißen von Nichteisenmetallen bis zu 150 Parameter pro Schweißprozess erfasst, gespeichert und ausgewertet werden. Jede Schweißung hat damit ihren eigenen digitalen Fingerabdruck, was die Tracability sicherstellt. Gleichzeitig bilden diese Daten eine wertvolle Basis für dauerhaft niedrige Ausschussraten und einen zuverlässigen Prozess.
Besonders anspruchsvoll ist die Produktion von Batteriezellen mit wenigen Folienlagen oder aus dünnen Materialien. Um bei diesen Anwendungen starke Verbindungen erzeugen zu können, ohne die sensiblen Folien zu beschädigen, ist eine extrem präzise Kraftsteuerung in einem Bereich von bis zu fünf Newton bei einer Frequenz von 35 kHz notwendig.
Neben einem elaborierten Steuerungssystem hat sich gezeigt, dass eine entsprechende Ergänzung der Hardware, sprich des Ultraschall-Schweißsystems notwendig ist. Versuche im Ultraschall-Labor ergaben, dass die Entwicklung einer Wippe notwendig ist, um auch bei geringsten Kräften einen stabilen Prozess zu ermöglichen.
Um einen idealen Transfer der Energie aus oder auch in die Batterie zu gewährleisten, benötigt es starke Verbindungen zu Terminals und Hochvoltkabel mit möglichst wenig Übergangswiderstand. Auch hier kann die Ultraschall-Schweißtechnologie einen erheblichen Mehrwert liefern, indem sie Verbindungen erzeugt, ohne dabei Verluste bei der Leitfähigkeit hinnehmen zu müssen. Somit geht keine wertvolle Energie in Batterie und Kabelbaum verloren, wodurch die Reichweite des Elektromobils nicht beeinträchtigt wird.
Doch gerade beim Verschweißen von Hochvoltkabeln aus Aluminium und Kupfer traten bislang zwei Herausforderungen für die Ultraschall-Schweißtechnologie auf:
1. die Zykluszeiten
2. die steigenden Durchmesser der Kabel
Beide Faktoren hängen eng miteinander zusammen und sind entscheidend, um die Produktionseffizienz zu steigern. Deshalb setzten Anwendungstechniker aus den Ultraschall-Laboren an diesen beiden Punkten an und entwickelten entsprechende Lösungen zur Optimierung der Produktionsbedingungen.
Für die immer größer werdenden Durchmesser von Hochvoltkabeln gibt es eine vermeintlich einfache Lösung. Je dicker die Kabel, desto mehr Leistung wird benötigt – entsprechend müssen die Generator leistungsstärker werden. Bis zu 12.000 Watt und Schweißkräfte von rund 10.000 N müssen die Generatoren erzeugen, um Hochvoltkabel mit Querschnitten von 150 mm² und mehr zu verbinden.
Eine so große Leistung erzeugt allerdings auch eine entsprechende Wärme. Damit es hier nicht zu Schäden an den Konvertern kommt, benötigen diese lange Abkühlzeiten. Für die Verschweißung von Hochvoltkabeln mit Terminals wurden deshalb 35 bis 40 Sekunden benötigt.
Um diese Zeit zu verringern, entwickelten Anwendungstechniker von Herrmann Ultraschall eine neue, patentierte Architektur für den Konverter, der die elektrische Spannung in mechanische Vibrationen umwandelt. Dabei wird die entstehende Wärme effektiv abgeleitet, sodass Abkühlzeiten nahezu vollständig obsolet werden. Die Zykluszeiten können damit auf unter 20 Sekunden reduziert werden.
„Zukünftig wird die Automatisierung bei der Verschweißung von Hochvoltkabeln sicher eine zunehmend wichtige Rolle einnehmen. Dabei sind kürzere Taktzeiten entscheidender denn je“, erklärt Michael Leipold und führt weiter aus: „Mit leistungsstarken Konvertern, die sich bereits im Produktionsalltag bewährt haben, können wir diese Beschleunigung realisieren.“
Die vergleichsweise langen Zykluszeiten bei der Verschweißung von Hochvoltkabeln sind jedoch teilweise auch in den Produktionsbedingungen begründet. Denn die meisten Kabel werden an Handarbeitsplätzen verschweißt; automatisierte Anlagen mit Ultraschalltechnologie sind zwar möglich, jedoch bislang die Ausnahme.
Zudem werden häufig eine Vielzahl an individuellen Kabelbäumen und –typen innerhalb einer Produktion verarbeitet. Da die meisten Schweißmaschinen jedoch nur auf die Verarbeitung eine Größe ausgelegt sind, muss der Arbeiter mehrfach die Maschine wechseln.
Mit einem neuartigen Schnellwechselsystem für Herrmann-Maschinen kann hier wertvolle Zeit eingespart werden. Schweißwerkzeuge oder ganze Vorrichtungen können innerhalb von weniger Minuten ausgetauscht werden und ermöglichen damit einen zügigen Applikationswechsel. Im Fokus der Entwicklung solcher Schnellwechselsysteme steht neben der Geschwindigkeit vor allem auch die Benutzerfreundlichkeit. Damit wird gewährleistet, dass keine zeit- oder kostenintensiven Fehler entstehen. Moderne Schweißmaschinen setzen daher auf Spannsysteme zum Austausch von Sonotroden, damit diese automatisch korrekt eingestellt sind.
Für den Erfolg der Elektromobilität sind unter anderem eine große Reichweite, schnelle Ladezeiten und niedrigere Produktionskosten entscheidend. An diesen Punkten kann die Ultraschall-Schweißtechnologie einen signifikanten Beitrag dazu leisten, indem sie:
Produktionskosten können somit durch eine Kombination aus intelligenter Steuerung, einem präzisen Schweißsystem und dem generell schonenden Ultraschall-Verfahren mit minimaler Hitzebelastung des Materials reduziert werden. Grundsätzlich gilt: Je früher der Ultraschall-Partner in das Projekt mit einbezogen wird, desto sicherer und effizienter kann der Schweißprozess gestaltet werden.