Nonwovens: soft material stays soft
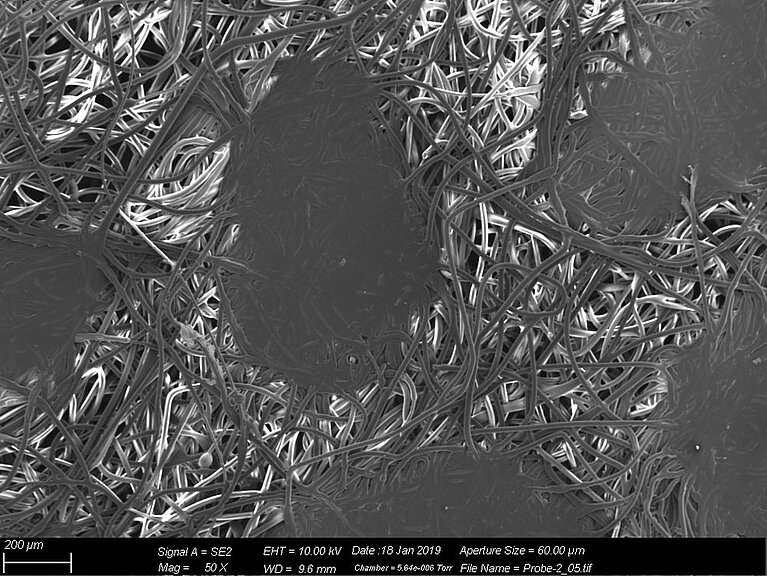
Ultrasonic bonding for ATB
The use of softness-enhancing Air-Through Bonded materials (ATB) is increasing – typical hygiene applications are acquisition distribution layers (ADL), waist panels, and top sheets. Ultrasonic welding can offer process related and environmental advantages over glue and heat bonding. The nonwovens laboratory at Herrmann Ultraschall provides high-tech support for application solutions when it comes to bonding ATB.
ATB is becoming popular because the feel, look and sound of disposable hygiene products before use can greatly affect consumer perceptions of softness. That makes it critical for disposable hygiene manufacturers to understand and evaluate their own production processes for impact on softness. ATB is a costly material and producers are interested in minimizing production scrap when further processing ATBs. It has been problematic to understand why some ATB bond well and others do not.
The composition of ATB with bi-component fibers
The application developers at Herrmann Ultraschall have configured a portfolio to determine and evaluate typical ATB materials – making use of extensive laboratory equipment like a Scanning Electron Microscope and a Differential Scanning Calorimetry. This service will help manufacturers to foresee bonding challenges and material wastage.
Bi-component fibers (Bi-Co) are an important part of ATB. So-called core-sheath Bi-Co, where one polymer is mantled by a second polymer, is a frequently processed bonding fibers for ATB nonwovens and deserve a second look. A bi-component fiber is used to exploit capabilities not existing in either polymer alone: PE increases softness, PET gives strength but has the disadvantage of the high melting point. PLA might be used when fibers from natural sources are being asked for, to name just a few. The melting point of the sheath material is lower than that of the core material, with the result that the core fibers adhere at the crossing points. The sheath ratio of the fiber can vary depending on the manufacturer and the Differential Scanning Calorimetry helps to determine these exact material ratios.
Micrographical evaluation of bonding spots in the ultrasonic laboratory
The evaluation of the surface and cross section of the different laminated materials with the help of a Scanning Electron Microscope allow firstly a study of the fiber quality and secondly an assessment of the weld quality. ATB material can vary greatly – the fiber composition has a strong influence on the material behavior and needs to be evaluated ideally prior to bonding. Weld performance can now also be tested beforehand.
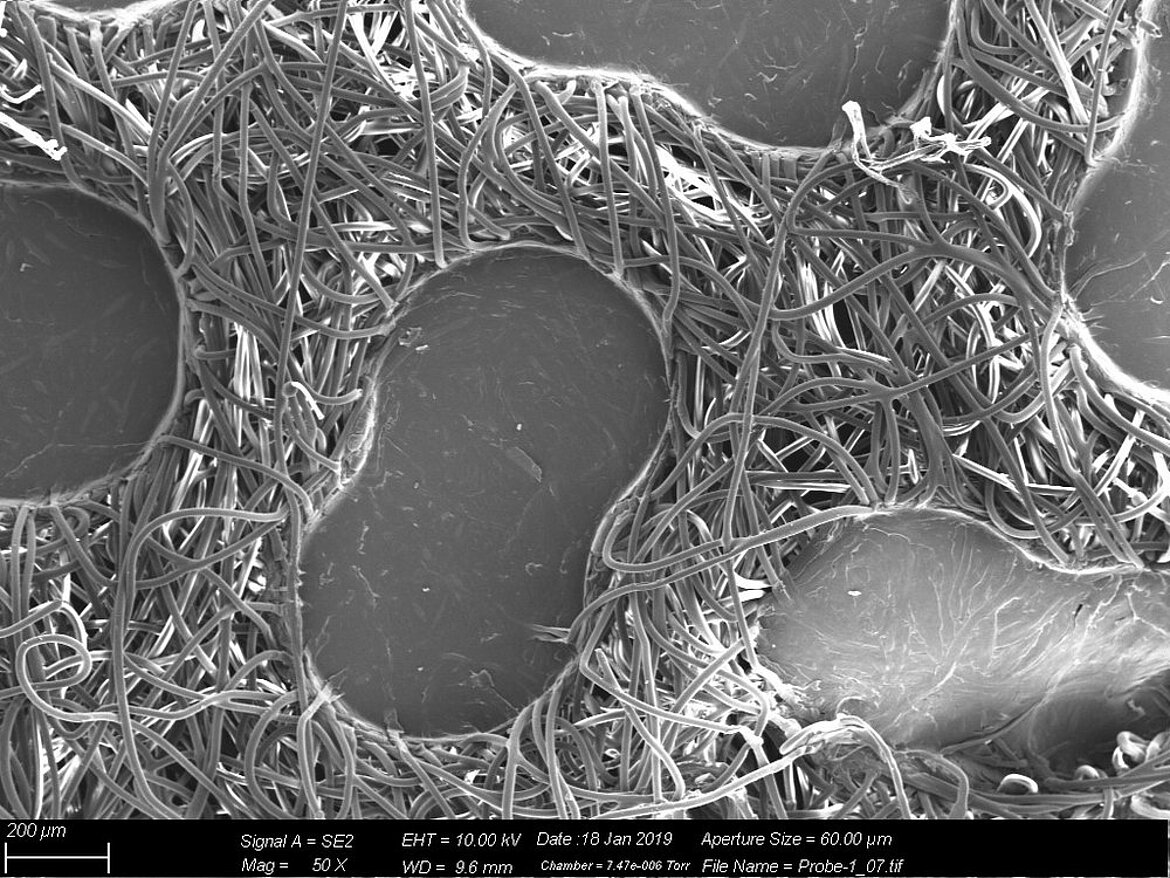