Ultrasonic welding of bio-based plastics
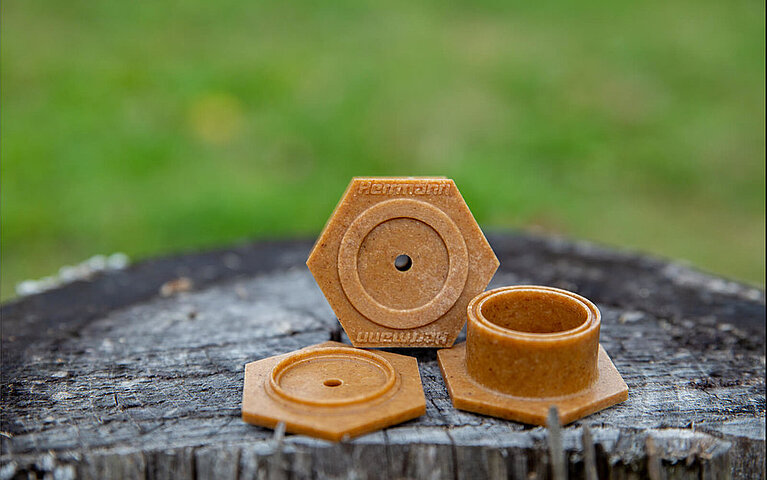
Ready for the age without oil?
As of now there are few inquiries for the welding of recycled materials, ie plastics that already have been processed once or more before. The weldability must be determined empirically in the test laboratory.
The next step is much more exciting: how does the use of bio-based plastics (bio-polymers) made from organic matter develop, and how can such bio-polymers be welded?
Our ultrasonic lab has studied two technical biopolymers from Tecnaro that are 100% renewable and biodegradable.
Biopolymers
ARBOFORM® materials incorporate lignin material, which is the second most abundant polymer in nature after cellulose. Lignin is a by-product of the pulp industry and accumulates around 50 million tonnes annually worldwide. When mixing lignin with natural fibers (flax, hemp or other fiber plants) and natural additives, we obtain a processable under temperature and pressure fiber composite material that can be processed on plastic injection molding machines to form parts.
Depending on the formulation, ARBOBLEND® materials consist of biopolymers, such as polyhydroxyalkanoates (PHA), polycaprolactone (PCL), polyesters (eg Bio-PET), starch, polylactic acid (PLA), bio-polyolefins (bio-PE), bio-polyamides (bio-PA), lignin, natural resins, waxes, oils, natural fatty acids, cellulose, biological additives and natural reinforcing fibers. Depending on the application, ARBOBLEND materials can be biodegradable or resistant.
Both types of plastic have strength values in the range of PC-ABS and are therefore suitable for comparison. The first step was the production of test specimens by our partner BARLOG. This provides a uniform starting point for testing the weldability, tensile and pressure resistance in the laboratory at Herrmann Ultraschall.
The test results have shown that the lignin-based bio-plastics can be welded by means of ultrasound and in principle can be processed with similar parameters. In tensile tests, it was found that the two bio-plastics do not quite come close to the pull-off forces of the petroleum-based plastic, but the ARBOLEND is within a comparable range of values and the ARBOFORM within normal strength requirements.
Conclusion:
Technical biopolymers currently play a subordinate role in production, but as a joining specialist, we are available to the plastics industry when it comes to investigating and shaping future trends.
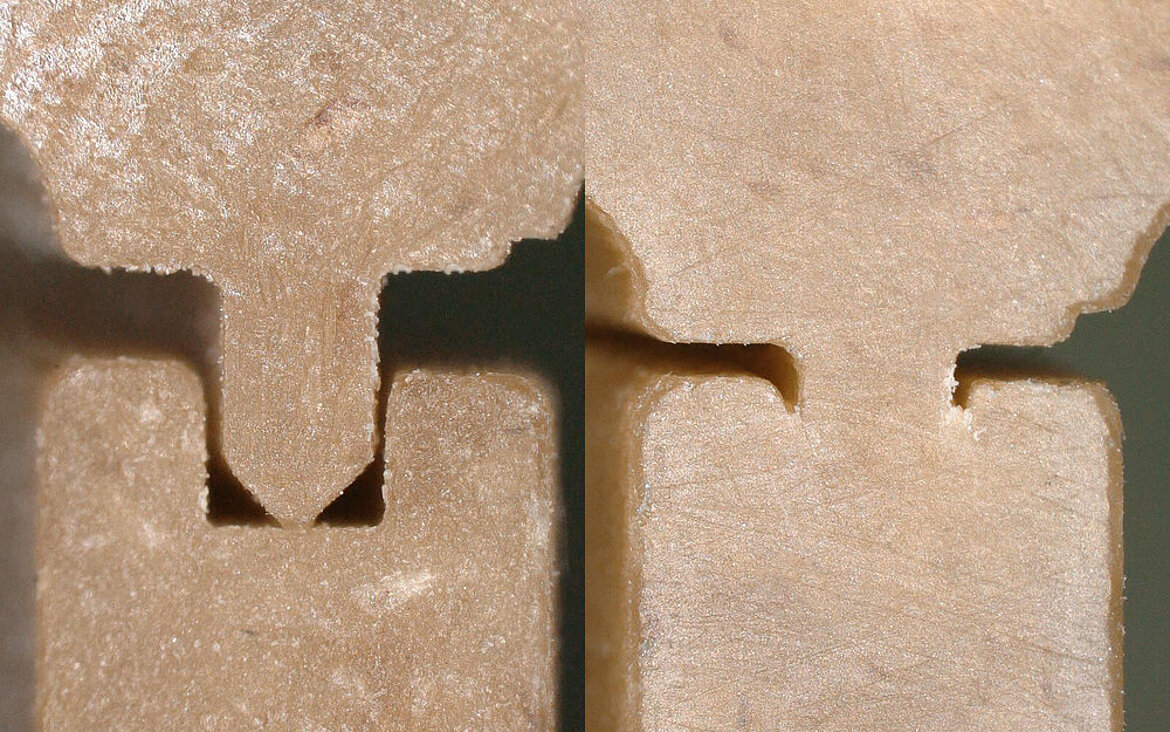