Ultrasonics brings new momentum to the circular economy
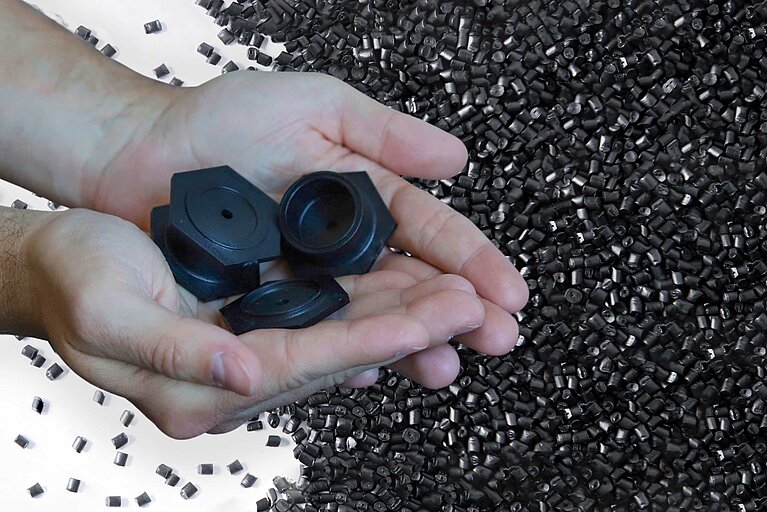
A study by Herrmann Ultraschall shows weldability of pure recycled material with ultrasonics
In a new feasibility study, Herrmann Ultraschall investigated the welding of a recycled plastic. The result: with the right parameters, comparable welding results are as achievable as with conventional plastics.
Pure recycled material has so far found little use, but the current shortage of materials is making it increasingly interesting, especially for companies in the automotive sector. For sustainability reasons, too, it can be worthwhile to use recycled plastic. The problem is that every time plastic is reprocessed, its material properties can deteriorate as the molecular chains become shorter and shorter. In a comparative study, Herrmann Ultraschall’s PLASTICS laboratory investigated how these changes affect the vibration behavior of plastic components.
Adjustment of welding parameters necessary
Using plastic PA 6.6, a common plastic frequently used in the automotive industry, the application engineers produced hexagonal test specimens to carry out the comparative study. The engineers used a conventional plastic of the type PA 6.6 with 30 percent glass fiber content; this was compared to a re-granulate also made of PA 6.6 GF30.
In initial preliminary tests, the basic weldability of the recycled material was examined first. For these trials, the technicians used a group of parameters as a starting point - so-called initial parameters - which are also used for the conventional plastic of the same type. This showed that although the test specimens made of recycled plastic could reliably weld together with ultrasonics, it was not possible to achieve a homogeneous connection with the initial parameters: The sectional images showed a clear parting plane between the upper and lower parts. This made it necessary to adjust the welding parameters
A quick way to a welding solution with initial parameters In the ultrasonics laboratory, initial parameters are a combination of welding parameters that serve as a starting point for the first welding tests. They are based on internal guidelines that list recommended values for amplitude and force for all common thermoplastics. Thanks to the guides, initial parameter sets, which are often already promising, can be generated quickly and easily. In this way, they help to reduce the development time and costs of a welding solution for the customer. |
3,000 Newton also achieved for the recyclate
In order to define the suitable values for recycled plastic, 18 different parameter groups were determined in a subsequent comparative study (DOE) around the initial parameters of the plastic, in which central parameters such as welding force, amplitude, welding path or trigger force were varied. Five specimens from each of the two comparison groups were welded with these values. The results were evaluated by sectional views as well as tensile tests.
In the course of this series of tests, the application engineers of the ultrasonic laboratory came across parameter sets that produced excellent welding results for the recycled material and for the virgin plastic. Of particular interest: the two parameter sets differed only in amplitude, which was 10 micrometers lower for the recycled plastic than for the conventional plastic.
"For both bodies, we were in a range around 3,000 newton. That is quite impressive. We had actually expected to get worse values in both the cross-section and tensile tests. But with the parameter set determined in the DoE in each case, we achieved comparably good results," explains Jochen Ochs, Head of the PLASTICS application laboratory at Herrmann.
The series of tests thus provides not only positive results, but also, above all-important empirical values for future customer inquiries. However, it is not possible to make a general statement for the weldability of recycled plastics with ultrasonics from this study alone. Just as is the case with conventional plastics, each composition must be examined individually.
"For us, the most important thing is that the plastic is a thermoplastic, regardless of whether it is a recycled or a conventional plastic," explains Jochen Ochs and continues: "In the data sheet, we can read out some factors regarding the mechanical and thermal properties. But you can't find a real indicator for the quality of the weldability in the data sheet, because there are other influencing factors that often only become apparent in the welding test." However, thanks to the company's many years of experience, precise assessments could be made in advance.
Bio-plastics as a sustainable alternative
The examination of recycled plastics is already the second study by Herrmann's ultrasonic laboratory on a more sustainable use of plastics. A few years ago, the first tests were carried out on the weldability of bio-plastics.
For this purpose, test specimens from three different compositions were examined: two of the bio-plastics tested consisted of blends, i.e. a composition of bio-plastic as well as standard plastic. The third material consisted of one hundred percent biopolymers. While the two blends were able to achieve similar results to standard plastics, the pure bioplastic achieved only half the tensile forces. However, this still makes it sufficient for a wide range of application types.
Conclusion
With recycled and bio-plastics, new paths to more sustainable production are opening up for many companies in the plastics industry. Especially high-quality re-granulate that is reused for the first time can become an important element in saving resources in the future. If there is uncertainty about the use of the more environmentally friendly plastics, suitably well-equipped ultrasonics laboratories can advise on the closer selection of the material and provide certainty through welding tests.
From reject to regranulate In the regranulation process, clean plastic rejects are first processed in mills to produce a pure regrind. In a compounder, this regrind is melted, homogenized and degassed. This gives the regranulate mechanical properties similar to those of the original plastic and allows it to be further processed accordingly. However, the decisive factor here is the quality and purity of the plastic rejects used. |
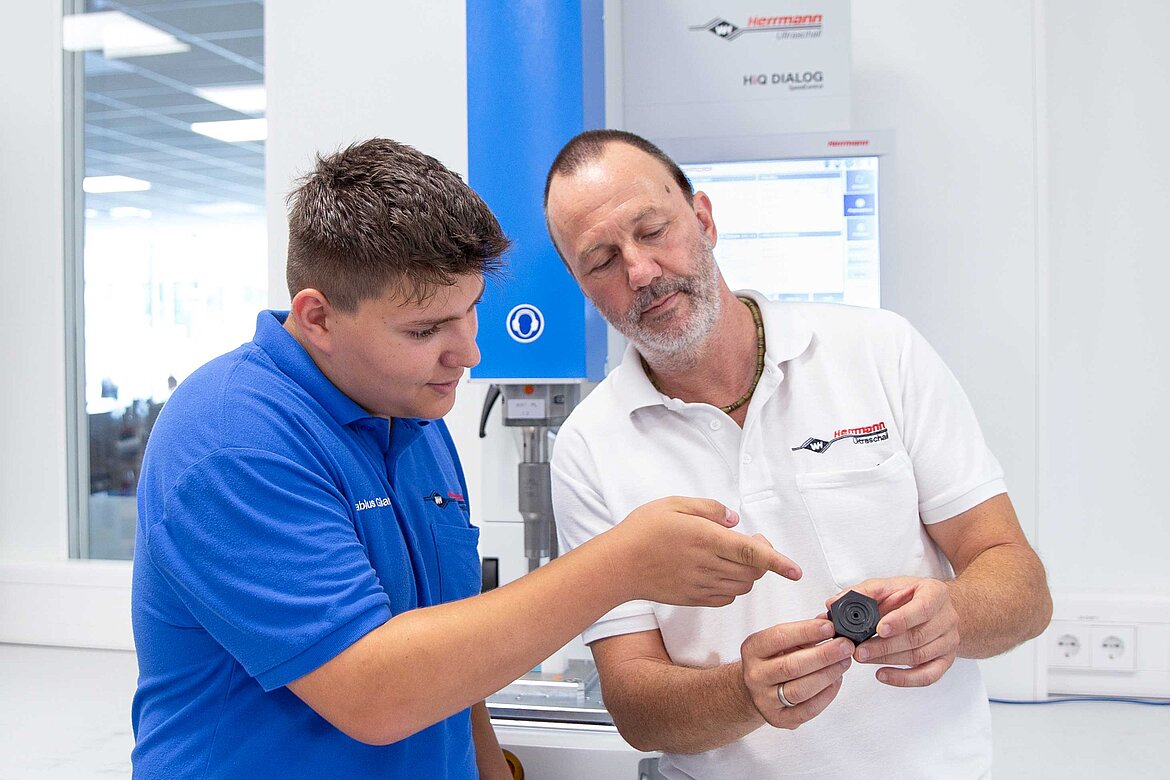
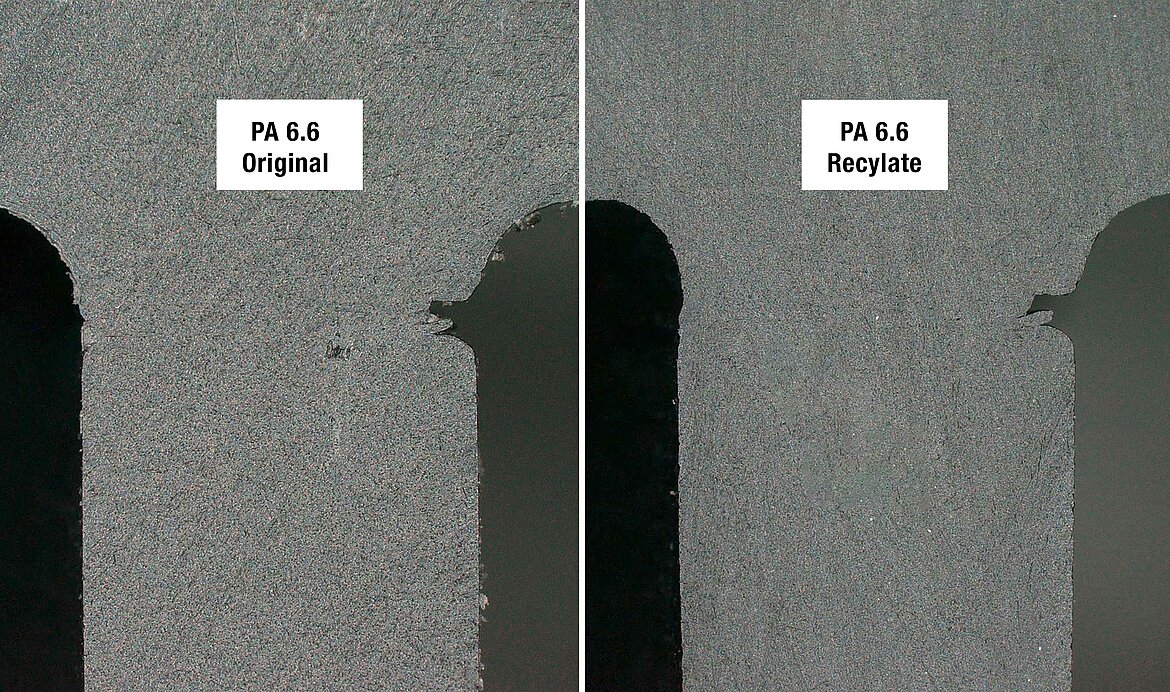
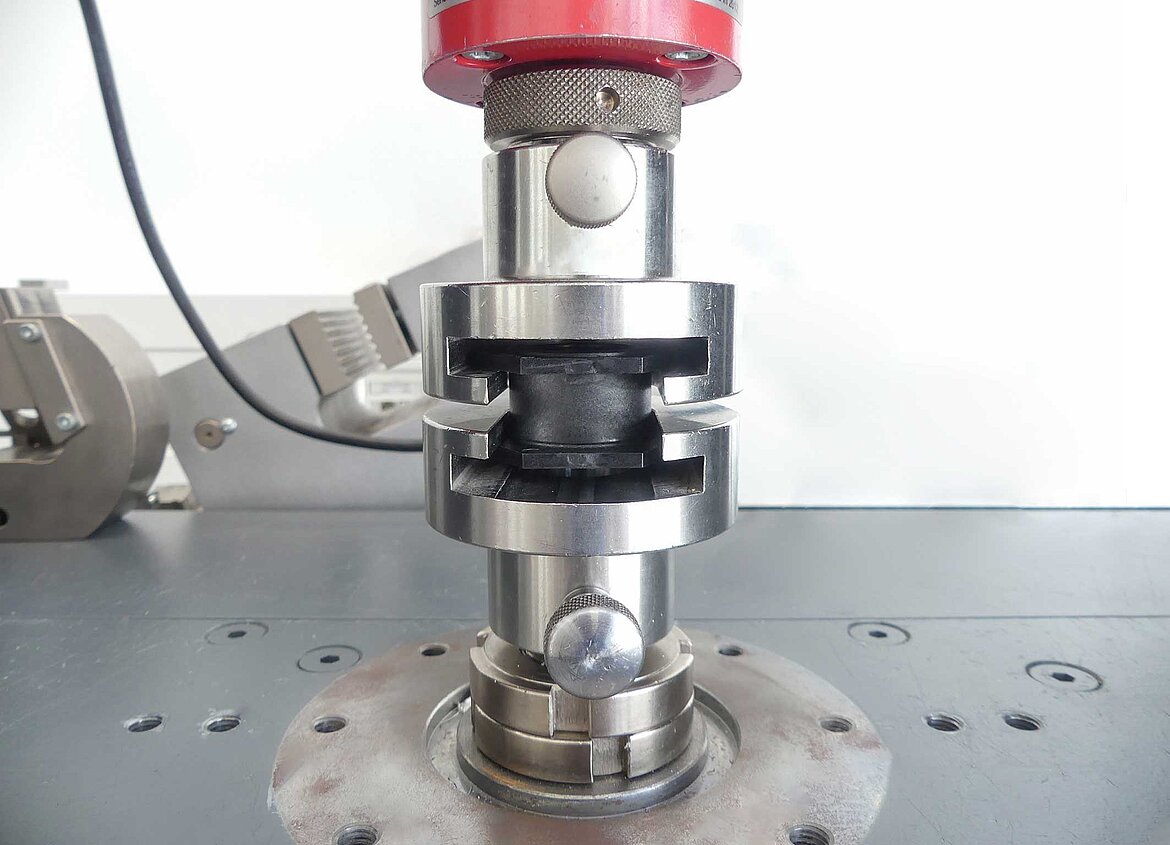