24. October 2024
, News
Utilizing the digital potential of battery manufacturing
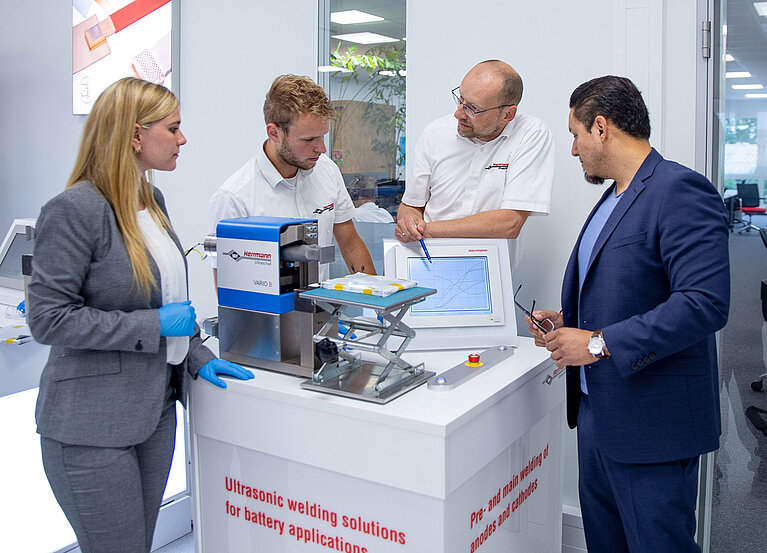
Up to 150 data points per welding process: Ultrasonic welding offers exciting opportunities for the digitalization of battery production - both in manual workstations and automated systems. If the data is used correctly, both safety and efficiency can be permanently increased, and new standards can be set in quality control.
To increase the efficiency of battery manufacturing, qualified data is crucial to success. Optimization of these data points can only occur when you know exactly where rejects happen or the specific time and energy required for individual processes. As one of the last steps in the battery production chain, the joining process is particularly important: if errors occur here, the entire cell usually has to be disposed of, resulting in high costs.
Ultrasonic welding offers optimal possibilities for measuring important data at this critical point in the manufacturing process. Each individual welding process is digitally measured and saved and can be evaluated accordingly.
The primary challenge is not about data measurement, but rather about leveraging it in a way to gain an advantage from the information.
Initially, measuring and evaluating the data is crucial for the development of the welding process. The three central welding parameters are particularly interesting for the welding of battery cells:
- Force
- amplitude
- energy
These parameters influence each other, so they must be precisely aligned. If one of the parameters is changed, the other values must also be adjusted. For example, the force or amplitude directly influences the power: the more force you exert or the more amplitude you use, the more power is required. Higher power, in turn, can reduce the time required while maintaining the same energy input.
Initial feasibility tests only require a few welds. With sufficient experience in handling the materials, initial welding parameters can be developed after just 10–20 welds.
"Finding the right parameters means laying the groundwork for a reliable welding process," explains Markus Haas, Global Sales Director METALS at Herrmann Ultraschall. "However, the conditions in the laboratory are often different to those in manufacturing: humidity, temperature, or other environmental influences can mean that we have to readjust the parameters."
This additional optimization is beneficial: with the ideal parameters, the process window expands significantly, allowing for some degree of compensation for material fluctuations. This increases safety and minimizes reject rates.
It is important that the requirements are clarified during the start of process development. This offers the opportunity to optimize the process according to individual parameters. For instance, if minimizing welding time is a priority, some tolerances in the strength of the connection are accepted
If you compare two welds with each other, it is difficult to identify patterns in the deviations. However, a data set of 1,000 or even 10,000 records, is statistical differences become identifiable. . Data acquisition in ultrasonic welding offers this possibility, provided the controllers are equipped with the appropriate software.
This enables the ability to draw conclusions about the material quality across various production batches, for example. Additionally, it allows for identifying the reasons behind faulty welds, which might not be apparent if only individual welds with seemingly minor deviations from the ideal parameters were considered.
Welding tool wear from one weld to the next is also so minimal that it is hardly noticeable. However, over a longer period, it is possible to trace exactly when more time is required to obtain a good weld despite the same energy - a strong indication of wear on the welding tool. This enables precise tracking to determine when the sonotrode should be replaced or the parameters adjusted after a certain number of welds. In the future, early detection will allow for prompt action, ensuring consistently visually flawless welding results.
Another advantage of archiving the welding processes is that each component can be assigned to an individual weld and is given its own digital fingerprint. This enables seamless traceability. In the event of an anomaly arising within the battery at a later stage, it becomes feasible to track whether the welding process adhered to the specified criteria or if any deviations occurred. If the latter is the case, all other battery cells with the same deviations can be identified.
However, it is important not only to look at the joining process in the battery cell production chain. To be able to carry out truly meaningful evaluations, all process steps should be digitally mapped. Ultrasonic welding fits seamlessly into such a view of the entire production chain.
In an increasingly automated production environment, the amount of data points will increase enormously in the future. This will also increase the potential for smart utilization of this information.
"It will be exciting if we include the possibilities of artificial intelligence into the process," explains Markus Haas. "In the future, AI could extract even more potential from the data, which we can use to make the entire welding process even faster, even safer, or even more efficient. To do this, however, it needs access to a sufficient amount of data, which can already be collected today."
Companies should prioritize the early digitization of their production processes. This proactive approach not only prepares them for a digitalized future but also delivers tangible benefits today, such as increasing the safety of their manufacturing and ensuring product quality, thereby increasing overall efficiency and profitability. Embracing ultrasonics as a future-proof joining technology offers an ideal starting point for this.
Unlike other joining processes such as laser or induction welding, ultrasonic welding involves direct contact between the component and the welding tool. The generator activates the welding tool, the sonotrode, to vibrate at a certain frequency and amplitude. These vibrations are damped by the component during welding. To compensate for this damping, the generator makes adjustments to the power.
All these values can be visualized and saved digitally, along with many others. Despite the extremely short welding time of just a few hundred milliseconds, it is possible to track exactly what is happening to the component at any time during the process.