24. Oktober 2024
, News
Digitales Potenzial der Batterie-Produktion ausschöpfen
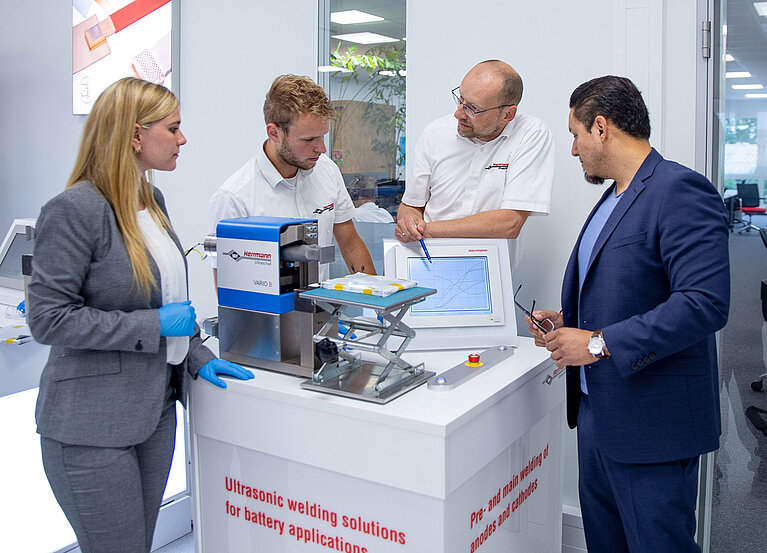
Bis zu 150 Daten pro Schweißvorgang: Das Ultraschallschweißen bietet spannende Möglichkeiten zur Digitalisierung der Batterieproduktion – sowohl in Handarbeitsplätzen als auch in automatisierten Anlagen. Werden die Daten richtig genutzt, können Sicherheit und Effizienz dauerhaft erhöht werden, aber auch neue Maßstäbe in der Qualitätskontrolle gesetzt werden.
Um die Leistungsfähigkeit einer Batterie-Produktion zu steigern, sind qualifizierte Daten erfolgsentscheidend. Nur wenn man genau weiß, an welchen Punkten Ausschuss entsteht oder wie viel Zeit und Energie einzelne Prozesse benötigen, können diese Stellen optimiert werden. Dem Fügeprozess kommt als einem der letzten Schritte in der Produktionskette einer Batterie besondere Bedeutung zu: Kommt es hier zu Fehlern, muss meist die ganze Zelle entsorgt werden, wodurch hohe Kosten entstehen.
Um an dieser kritischen Stelle in der Produktion wichtige Daten zu erfassen, bietet das Ultraschallschweißen optimale Möglichkeiten. Jeder einzelne Schweißprozess wird digital erfasst, gespeichert und kann entsprechend ausgewertet werden.
Die Herausforderung besteht jedoch nicht primär im Erfassen der Daten. Vielmehr geht es um die intelligente Nutzung, um aus den Informationen einen Vorteil zu generieren.
Zunächst ist die Erfassung und Auswertung der Daten entscheidend für die Entwicklung des Schweißprozesses. Für das Schweißen von Batteriezellen sind vor allem die drei zentralen Schweißparameter interessant:
Die Parameter beeinflussen sich gegenseitig, weshalb sie genau aufeinander abgestimmt sein müssen. Ändert man einen der Parameter, müssen auch die anderen Werte zwingend angepasst werden. So beeinflussen etwa die Kraft oder die Amplitude unmittelbar die Leistung: Je mehr Kraft man ausübt oder je mehr Amplitude man verwendet, desto mehr Leistung wird benötigt. Eine höhere Leistung wiederum kann bei gleichbleibendem Energieeintrag die notwendige Zeit reduzieren.
Erste Machbarkeitstests benötigen nur wenige Schweißungen. Mit ausreichend Erfahrung im Umgang mit den Materialien können erste Schweißparameter bereits nach 10-20 Schweißungen entwickelt werden.
„Die richtigen Parameter zu finden, heißt, die Grundlage für einen zuverlässigen Schweißprozess zu legen“, erklärt Markus Haas, Global Sales Director METALS bei Herrmann Ultraschall. „Allerdings herrschen im Labor oft andere Bedingungen als in der Produktion: Luftfeuchtigkeit, Temperatur oder andere Umwelteinflüsse können bedeuten, dass wir die Parameter nochmal nachjustieren müssen.“
Diese weitergehende Optimierung lohnt sich: Mit den idealen Parametern erweitert sich das Prozessfenster so weit, dass Schwankungen in den Materialien bis zu einem gewissen Maß ausgeglichen werden können. Das erhöht die Sicherheit und minimiert die Ausschussraten.
Wichtig ist, dass schon zu Beginn der Prozessentwicklung die Anforderungen geklärt werden. Das bietet die Möglichkeit, den Prozess auf einzelne Parameter hin zu optimieren. Das ist beispielsweise der Fall, wenn die aufgewendete Schweißzeit so gering wie möglich gehalten werden soll, dafür aber mehr Toleranz in der Festigkeit der Verbindung akzeptiert wird.
Vergleicht man zwei Schweißungen miteinander, ist es schwierig, Muster in den Abweichungen zu erkennen. Liegen allerdings 1.000 oder gar 10.000 Datensätze vor, können statistische Unterschiede sichtbar gemacht werden. Diese Möglichkeit bietet die Datenerfassung im Ultraschallschweißen, sofern die Steuerungen mit der entsprechenden Software ausgestattet sind.
So ist es möglich, beispielsweise Rückschlüsse auf die Materialgüte verschiedener Produktionschargen zu ziehen oder die Gründe für Fehlschweißungen zu identifizieren, die sich nicht offenbaren, wenn nur Einzelschweißungen mit vermeintlich unbedeutenden Abweichungen von den Idealparametern betrachtet werden.
Auch der Verschleiß des Schweißwerkzeugs von einer auf die andere Schweißung ist so minimal, dass er nicht auffällt. Über einen längeren Zeitraum betrachtet kann jedoch genau nachgezeichnet werden, wann trotz gleicher Energie mehr Zeit benötigt wird, um eine gute Schweißung zu erhalten – ein starkes Indiz für die Abnutzung am Schweißwerkzeug. Dadurch kann ermittelt werden, nach wie vielen Schweißungen die Sonotrode ersetzt oder die Parameter angepasst werden sollten. So kann künftig frühzeitig reagiert und ein konstant perfektes Schweißergebnis gewährleistet werden.
Ein weiterer Vorteil der Archivierung der Schweißprozesse: Jedes Bauteil kann einer einzelnen Schweißung zugeteilt werden und erhält seinen eigenen digitalen Fingerabdruck. Das ermöglicht eine lückenlose Rückverfolgung. Kommt es im Feld später zu Auffälligkeiten der Batteriezelle, kann genau zurückverfolgt werden, ob der Schweißprozess nach den festgelegten Vorgaben erfolgt ist oder ob Abweichungen aufgetreten sind. Ist letzteres der Fall, können alle weiteren Batteriezellen mit denselben Abweichungen identifiziert werden.
Wichtig ist allerdings dabei nicht nur den Fügeprozess in der Wertschöpfungskette der Batteriezelle zu betrachten. Um wirklich aussagekräftige Auswertungen durchführen zu können, sollten sämtliche Prozessschritte digital abgebildet werden. Das Ultraschallschweißen fügt sich dabei nahtlos in eine solche Betrachtung der gesamten Produktionskette ein.
In einem zunehmend automatisierten Produktionsumfeld wird die Menge an Daten künftig enorm zunehmen. Damit steigen auch die Möglichkeiten zur smarten Nutzung dieser Informationen. „Spannend wird es sein, wenn wir die Möglichkeiten von künstlicher Intelligenz in den Prozess einbeziehen“, erklärt Markus Haas. „Eine KI könnte in Zukunft noch weitere Potenziale aus den Daten extrahieren, mit denen wir den gesamten Schweißprozess noch schneller, noch sicherer oder noch effizienter gestalten können. Dafür benötigt sie aber Zugang zu einer ausreichenden Menge an Daten, die schon heute gesammelt werden kann.“
Unternehmen sollten deshalb frühzeitig auf die Digitalisierung ihrer Produktionsprozesse setzen. Dadurch bereiten sie sich nicht nur optimal auf eine digitalisierte Zukunft vor. Sie können auch heute schon ganz konkrete Mehrwerte erzielen, indem sie die Sicherheit ihrer Produktion erhöhen, die Qualität ihrer Produkte sicherstellen und damit ihre gesamte Effizienz und Wirtschaftlichkeit steigern. Die Nutzung von Ultraschall als zukunftssichere Fügetechnologie bietet dafür einen idealen Ansatzpunkt.
Im Gegensatz zu anderen Fügeverfahren wie dem Laser- oder Induktionsschweißen besteht beim Ultraschallschweißen direkter Kontakt zwischen Bauteil und Schweißwerkzeug. Der Generator regt das Schweißwerkzeug, die Sonotrode, mit einer bestimmten Frequenz und Amplitude zum Schwingen an. Diese Schwingungen werden während des Schweißens vom Bauteil gedämpft. Um diese Dämpfung auszugleichen, steuert der Generator mit einer Anpassung der Leistung entgegen.
All diese Werte können visualisiert und, neben vielen weiteren, digital gespeichert werden. Trotz der äußerst geringen Schweißzeit von wenigen hundert Millisekunden kann so zu jedem Zeitpunkt während des Prozesses genau verfolgt werden kann, was am Bauteil passiert.