Pequeñas series eficientes
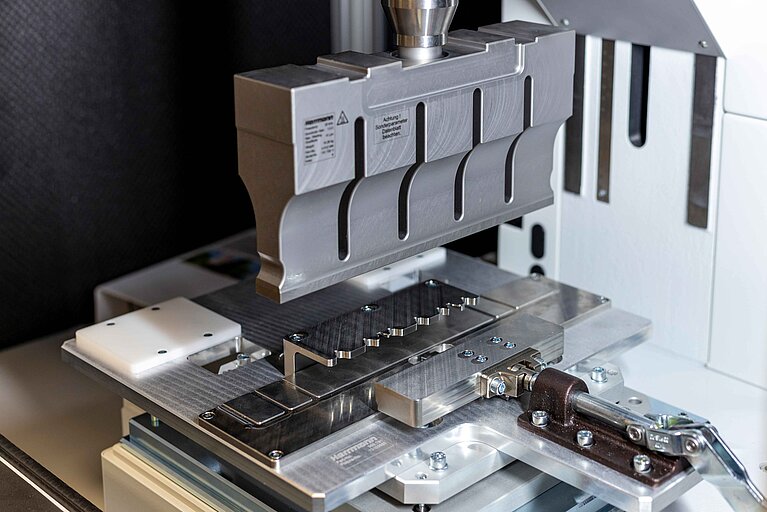
Soldadura para tamaños de lote pequeños mediante ultrasonidos de forma económica
Para los productores, estampar manualmente 18 conectores hembra de latón en un armazón de plástico de un elemento de mando era un proceso laborioso y caro. La soldadura por ultrasonido ofreció una alternativa eficiente que redujo de forma considerable los tiempos de ciclo. Además, fue provechosa desde el punto de vista económico, a pesar del reducido número de piezas producidas. La versatilidad del sonotrodo y la participación de HERRMANN ENGINEERING fueron factores esenciales en este proyecto.
Con tiempos de producción de más de 3 minutos por componente, preparar un armazón de plástico solía ser una tarea que demandaba mucho tiempo para apra-plast Kunststoffgehäuse-Systeme GmbH. Los tiempos de ciclo eran tan largos porque cada uno de los 18 conectores hembra de latón tenía que estamparse de forma individual en el armazón mediante calor. Debido al reducido número de piezas a producir, emplear un proceso automatizado no resultaba conveniente. El proceso alternativo de moldeo de los conectores hembra también se descartó por el alto costo asociado.
Durante uno de los diálogos habituales que sostenemos con apra-plast, en Herrmann Ultraschall GmbH & Co KG nos enteramos del reto y presentamos una idea para conseguir un proceso más eficiente. Nuestra colaboración nos permitió desarrollar una solución especial de soldadura por ultrasonido. ¿El resultado? Los tiempos de producción del componente se redujeron de forma importante y la eficiencia de todo el proceso se incrementó.
5 veces más rápido gracias al sonotrodo de cuchilla especial
La tarea de unión consistía en estampar varios conectores hembra de latón en el armazón de policarbonato, simultáneamente y mediante ultrasonidos. Para ello, primero desarrollamos un sonotrodo especial que puede estampar todos los conectores hembra simultáneamente y con precisión en cada lado del armazón. Logramos reducir las 18 etapas que antes se requerían para procesar todo el armazón a solo 4 etapas, lo cual significa que el tiempo de ciclo se redujo a solo 40 segundos, es decir, una quinta parte de la duración original.
Durante el propio proceso de soldadura, el sonotrodo de cuchilla se aplica simultáneamente a todos los conectores hembra de latón ubicados sobre ese lado a lo largo del armazón. Los ultrasonidos estimulan los conectores hembra y hacen que oscilen. Luego, la oscilación se transfiere al armazón de plástico e inicia el proceso de fundición. El material fundido fluye hacia el interior de las muescas de los conectores hembra, donde se produce una conexión fija. Este proceso permite que los conectores hembra de latón queden incrustados por completo en el armazón y simultáneamente protege el material contra daños. De ese modo, se obtuvo un resultado visualmente impecable.
Durante el proceso de soldadura, resulta fundamental que los conectores hembra queden estampados de manera completa y uniforme, ya que el armazón para la producción del producto final (un elemento de mando) se atornilla a una pieza contrapuesta. La presencia de irregularidades en la superficie, como las que producen los conectores hembra mal estampados, podría impedir que ambas partes de la carcasa de plástico puedan juntarse para generar un sello posteriormente.
Para procurar que los conectores hembra se estampen de manera uniforme, el componente debe quedar completamente plano en la máquina durante el proceso de soldadura y debemos poder fijarlo en su lugar para que no ocurra ningún movimiento. Para conseguirlo, desarrollamos un alojamiento (fixture) especial con ranuras. Eso le permite al usuario estampar el componente con firmeza en el alojamiento (fixture), prensarlo en su lugar y soldar el primer lado del armazón. Luego, la pieza se gira y se vuelve a sujetar para entonces soldar el segundo lado del armazón. Los 18 conectores hembra quedan incrustados en 4 etapas en total. Durante el proceso de desarrollo del proyecto, la combinación del sonotrodo y el alojamiento de diseño especial fue lo que finalmente permitió obtener un proceso de soldadura por ultrasonido fiable para producir el armazón largo con aristas de 310 mm de longitud.
Una sola máquina para varias aplicaciones
Con el fin de reducir el tiempo de amortización de la máquina soldadora por ultrasonido, el equipo de Herrmann Engineering sugirió otros usos posibles a partir de los proyectos actuales de apra-plast. El sistema de cambio rápido de las herramientas de soldadura permite que la máquina soldadora por ultrasonido pueda equiparse con otra herramienta en tan solo unos minutos para adecuarla a una aplicación diferente. Se implementó un proyecto adicional, en conjunto con el del armazón, que también se produjo en pequeñas series.
Este producto es la carcasa de plástico de un instrumento de medición en el que se incrusta una mirilla de inspección hecha de plexiglás (PMMA). Antes, la hoja se unía de forma manual, lo cual tenía varias desventajas. La conexión entre los componentes debe ser impermeable para que el producto final funcione sin defectos. Sin embargo, cuando los componentes se estampan empleando un adhesivo, suelen formarse burbujas de aire que afectan de forma adversa la impermeabilidad. Además, los componentes podían deslizarse y desalinearse debido al proceso de unión manual, lo cual no solo causaba defectos de impermeabilidad en el producto final, sino también de apariencia.
Las pruebas iniciales mostraron que el empleo de ultrasonidos en este caso podía contribuir a elevar la calidad del producto. La mirilla de inspección se une a la carcasa de plástico mediante soldadura por ultrasonido para generar un sello absolutamente impermeable. Además, prescindir de adhesivos también permite obtener un resultado visualmente impecable y genera una conexión totalmente compatible con los procesos ecológicos, sin aditivos. Otro criterio crucial para usar la tecnología de soldadura por ultrasonido fue la posibilidad de supervisar el proceso: gracias a la estrecha supervisión y validación de cada proceso de soldadura individual, la máquina permite obtener un nivel de fiabilidad del proceso que antes no podía alcanzarse.
Factores de éxito: entrenamiento y asesoramiento
Con las dos soluciones desarrolladas, apra-plast está trabajando por primera vez con la tecnología de soldadura por ultrasonido. El entrenamiento básico pormenorizado sobre la soldadura por ultrasonido y el asesoramiento relativo a la factibilidad financiera y técnica del proyecto fueron factores decisivos. Mediante el arrendamiento de una máquina, el cliente fue capaz de ejecutar pruebas internas en condiciones de producción reales y familiarizarse de antemano con el uso de esta tecnología.
Conclusión
La solución de soldadura que desarrollamos muestra con claridad que el uso de los ultrasonidos también es provechoso para quienes necesitan producir tamaños de lote pequeños. Para ello, resulta esencial contar con apoyo firme durante todo el proyecto a fin de poder desarrollar una máquina versátil. En comparación con los procesos de unión manuales en particular, la soldadura por ultrasonido ofrece la gran ventaja de agilizar los tiempos de producción y elevar la calidad del producto, lo cual significa que los clientes pueden diseñar todos sus procesos de fabricación de tal forma que sean más económicos, sostenibles y eficientes.