Efficienza per le piccole serie
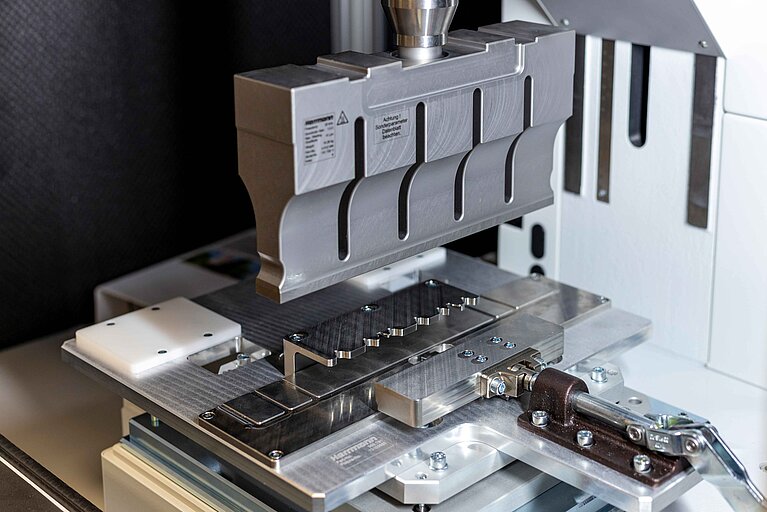
Saldatura economica di lotti di piccole dimensioni con l’utilizzo degli ultrasuoni
Per i produttori, l’improntatura manuale di 18 boccole in ottone in un telaio in plastica per un elemento di comando costituiva un processo laborioso e costoso. La saldatura ad ultrasuoni ha offerto un’efficiente alternativa in grado di ridurre sensibilmente i tempi di ciclo e finanziariamente vantaggiosa – anche in caso di un minore numero di pezzi. La versatilità del sonotrodo ed HERRMANN ENGINEERING hanno svolto un ruolo cruciale.
Con tempi di produzione superiori a tre minuti per componente, il montaggio di un telaio in plastica era un’operazione dispendiosa in termini di tempo per apra-plast Kunststoffgehäuse-Systeme GmbH. Il motivo alla base dei lunghi tempi di ciclo era il numero totale di 18 boccole in ottone da inserire singolarmente a caldo nel telaio. Un processo automatizzato non sarebbe stato vantaggioso per via del ridotto numero di unità. Anche l’alternativa del processo di stampaggio delle boccole era stata scartata per via degli elevati costi associati.
In occasione di uno dei regolari scambi di informazioni con apra-plast, Herrmann Ultraschall GmbH & Co KG è venuto a conoscenza della sfida, presentando poi un’idea per un processo maggiormente efficiente. Con la nostra collaborazione è stato possibile sviluppare una speciale soluzione per la saldatura ad ultrasuoni. Il risultato: i tempi di produzione per il componente si sono significativamente ridotti, mentre è aumentata l’efficienza dell’intero processo.
Cinque volte più veloce grazie allo speciale sonotrodo a coltello
L’operazione di giunzione richiedeva l’improntatura di numerose boccole in ottone nel telaio in policarbonato con il contemporaneo utilizzo di ultrasuoni. A tale scopo, dapprima abbiamo sviluppato uno speciale sonotrodo in grado di inserire tutte le boccole contemporaneamente e con precisione per ogni lato del telaio. È stato possibile ridurre le 18 fasi precedentemente necessarie per l’intero telaio a solo quattro fasi e questo ha significato la riduzione del tempo di ciclo a meno di 40 secondi – vale a dire appena un quinto della durata originale.
Durante lo stesso processo di saldatura, il sonotrodo a coltello viene applicato contemporaneamente a tutte le boccole in ottone su un lato per l’intera lunghezza del telaio. La stimolazione delle boccole avviene tramite ultrasuoni che ne determinano la vibrazione. La vibrazione viene quindi trasferita al telaio in plastica e inizia il processo di fusione. Il materiale fuso fluisce nelle incisioni presenti nelle boccole, producendo così un collegamento fisso. Questo processo consente la completa integrazione delle boccole in ottone nel telaio, proteggendone allo stesso tempo il materiale da eventuali danni. Il risultato è esteticamente impeccabile.
Durante il processo di saldatura è essenziale l’inserimento completo e uniforme delle boccole, in quanto il telaio per la produzione del prodotto finito, un elemento di comando, viene avvitato ad una controparte. Eventuali irregolarità sulla superficie, quali quelle prodotte da boccole sporgenti, potrebbero successivamente impedire la corretta giunzione delle due parti dell’alloggiamento in plastica.
Per assicurare un inserimento uniforme delle boccole, il componente deve essere completamente planare nella macchina durante il processo di saldatura e dobbiamo poterlo fissare in posizione in maniera tale da impedirne qualunque movimento. A tale scopo è stato sviluppato uno speciale supporto con scanalature. Ciò consente all’utente di eseguire il sicuro inserimento del componente nel supporto, serrarlo in posizione e saldare il primo lato del telaio. Dopodiché il pezzo viene ruotato e nuovamente fissato, quindi viene saldato il secondo lato del telaio. Tutte le 18 boccole vengono inserite in un totale di quattro fasi. Alla fine, nel processo di sviluppo del progetto è stata la combinazione del supporto e del sonotrodo appositamente concepiti a consentire un affidabile processo di saldatura per il lungo telaio con bordi di 310 mm.
Una macchina per diverse applicazioni
Per ridurre i tempi di ammortamento della saldatrice ad ultrasuoni, il team Herrmann Engineering ne ha suggerito ulteriori possibilità di utilizzo per gli attuali progetti di apra-plast. Il sistema di cambio rapido per gli utensili di saldatura permette di riattrezzare in pochi minuti la saldatrice ad ultrasuoni per una diversa applicazione. In combinazione con il telaio è stato implementato un ulteriore progetto, anche in questo caso per la produzione di piccole serie.
Il prodotto in questione è l’alloggiamento in plastica di uno strumento di misurazione in cui è integrata una finestra di ispezione in plexiglas (PMMA). In precedenza il collegamento del pannello veniva eseguito manualmente, determinando numerosi svantaggi. La connessione fra i componenti deve essere a tenuta stagna per garantire l’impeccabile funzionamento del prodotto finito. Tuttavia, l’improntatura dei componenti con l’utilizzo di adesivo causava spesso la formazione di bolle con compromissione della tenuta. Oltre a ciò, i componenti potevano scivolare via dalla loro posizione per via della procedura di montaggio manuale, a discapito non solo della tenuta ermetica, ma anche dell’aspetto del prodotto finito.
I test iniziali hanno dimostrato che l’utilizzo degli ultrasuoni in questo caso avrebbe contribuito ad aumentare la qualità del prodotto. La giunzione della finestra di ispezione all’alloggiamento in plastica avviene mediante saldatura ad ultrasuoni per creare una sigillatura a tenuta perfetta. Il mancato utilizzo di adesivo assicura a sua volta un risultato esteticamente impeccabile e rende le connessioni compatibili con l’ambiente, interamente senza additivi. Altro criterio fondamentale per l’utilizzo della tecnologia di saldatura a ultrasuoni è stata la possibilità di monitoraggio del processo: con una stretta attività di monitoraggio e validazione di ogni singolo processo di saldatura, la macchina assicura un livello di affidabilità di lavorazione mai raggiunto prima.
Fattori di successo: formazione e consulenza
Con le due soluzioni sviluppate, apra-plast opera per la prima volta con la tecnologia di saldatura a ultrasuoni. Elementi cruciali per la decisione sono stati l’intensa formazione di base nella saldatura ad ultrasuoni e la consulenza relativa alla fattibilità tecnica e finanziaria del progetto. Con il noleggio di una macchina, il cliente ha potuto effettuare i test in azienda nelle reali condizioni di produzione e acquisire in anticipo familiarità con l’utilizzo della tecnologia.
Conclusione
La soluzione di saldatura sviluppata dimostra che l’utilizzo degli ultrasuoni è vantaggioso anche per la produzione di lotti di piccole dimensioni. Condizione essenziale è l’assistenza completa per l’intera durata del progetto così da poter sviluppare una macchina versatile. Soprattutto se confrontata con processi di giunzione manuali, la saldatura ad ultrasuoni offre il grande vantaggio di tempi di produzione più rapidi e maggiore qualità del prodotto, permettendo quindi ai clienti di progettare processi di lavorazione più economici, sostenibili ed efficienti.