De petites séries rentables
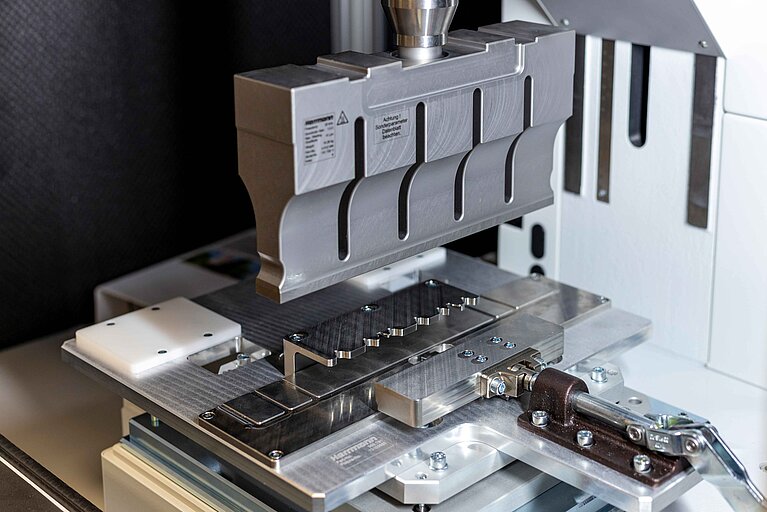
Souder des lots de petite taille de manière économique grâce aux ultrasons
L’insertion manuelle de 18 connecteurs femelles en laiton dans un châssis plastique pour un panneau de commande représentait pour les producteurs une procédure laborieuse et onéreuse. Le soudage par ultrasons a offert une alternative efficace qui a permis de raccourcir considérablement les temps de cycle tout en étant financièrement rentable, malgré un petit nombre d’unités. La polyvalence de la sonotrode et la solution HERRMANN ENGINEERING ont joué un rôle essentiel ici.
Avec des temps de production de plus de trois minutes par composant, l’équipement d’un châssis plastique était une tâche chronophage pour la société apra-plast Kunststoffgehäuse-Systeme GmbH par le passé. La longue durée des temps de cycle avait pour cause un total de 18 connecteurs femelles en laiton qui devaient être insérés un par un dans le châssis sous l’action de la chaleur. Un processus automatisé ne valait pas le coup au vu du petit nombre d’unités. Quant à la méthode alternative consistant à mouler les connecteurs femelles, il en était hors de question étant donné les coûts élevés associés.
Au cours de l’un des échanges réguliers qu’elle entretient avec la société apra-plast, Herrmann Ultraschall GmbH & Co. KG a pris connaissance de cette problématique et présenté une idée pour une procédure plus efficace. Dans le cadre de notre collaboration, nous avons pu développer une solution de soudage par ultrasons spécifique. Résultat : les temps de production du composant ont été nettement raccourcis et le rendement de l’intégralité de la procédure, amélioré.
Cinq fois plus vite grâce à la sonotrode MS spéciale
La tâche d’assemblage consistait à insérer plusieurs connecteurs femelles en laiton dans un châssis en polycarbonate à l’aide des ultrasons. Pour ce faire, nous avons tout d’abord développé une sonotrode spéciale capable d’insérer tous les connecteurs femelles de manière simultanée et avec précision sur chaque côté du châssis. De 18 étapes de travail alors nécessaires pour équiper entièrement le châssis, nous sommes passés à seulement quatre, ce qui signifie que le temps de cycle a été réduit à moins de 40 secondes seulement, autrement dit un cinquième de la durée initiale.
Au cours du processus de soudage en tant que tel, la sonotrode MS est appliquée simultanément sur tous les connecteurs femelles en laiton sur un côté et sur toute la longueur du châssis. Les connecteurs femelles sont stimulés par les ultrasons, et entrent ainsi en vibration. Ces vibrations sont ensuite transférées au châssis plastique et initient le processus de fusion. La fusion pénètre dans les indentations des connecteurs femelles où une liaison fixe est générée. Le processus permet l’intégration complète des connecteurs femelles en laiton dans le châssis, tout en protégeant leur matériau de tout type d’endommagement. Il en résulte une soudure visuellement impeccable.
Durant le processus de soudage, il est essentiel que les connecteurs femelles soient complètement et uniformément insérés, car le châssis est voué à être vissé sur une contre-pièce pour la fabrication du produit final, à savoir un panneau de commande. La présence d’irrégularités à la surface, susceptibles d’être causées par des connecteurs femelles protubérants p. ex., risque de compromettre le bon assemblage des deux pièces du boîtier plastique et donc la création d’une belle jointure de scellage ultérieurement.
Afin de garantir une insertion uniforme des connecteurs femelles, le composant doit être bien à plat dans la machine au cours du processus de soudage, et nous devons être en mesure de le fixer en place afin de prévenir tout mouvement. Un dispositif de posage spécial avec rainures a été développé à cette fin. Ainsi, l’utilisateur peut insérer le composant dans le dispositif de posage en toute sécurité, bien le fixer en place et souder le premier côté du châssis. La pièce est ensuite tournée et refixée, et le second côté du châssis est soudé. Les 18 connecteurs femelles sont intégrés en un total de quatre étapes. Au cours du processus de développement du projet, c’est en fin de compte l’association de la sonotrode et du dispositif de posage, tous deux de conception spéciale, qui a permis d’obtenir un processus de soudage par ultrasons fiable pour le long châssis dont les bords mesuraient 310 mm de long.
Une machine, de multiples applications
Afin de réduire la durée d’amortissement de la machine de soudage par ultrasons, l’équipe Herrmann Engineering a suggéré d’autres possibilités d’utilisation dans le cadre des projets actuels de la société apra-plast. Le système de changement rapide des outillages de soudage signifie que la machine de soudage par ultrasons peut être rééquipée pour une application différente en seulement quelques minutes. Un autre projet a été mis en œuvre avec le châssis, également dans le cadre d’une production en petites séries.
Le produit en question est le boîtier plastique d’un instrument de mesure dans lequel un regard en plexiglas (PMMA) est intégré. Jusqu’alors, le regard était rattaché à la main, une opération impliquant un certain nombre d’inconvénients. Le raccord entre les composants doit être étanche afin de garantir le bon fonctionnement du produit final. Or, une insertion par adhésif implique le risque fréquent de formation de bulles d’air, venant alors compromettre l’étanchéité. Par ailleurs, les composants parvenaient à bouger de leur place en raison de la procédure d’assemblage manuelle. Autrement dit, il n’y avait pas que l’étanchéité qui risquait d’être compromise, l’esthétique du produit final aussi.
De premiers tests ont démontré que l’utilisation des ultrasons ici pouvait contribuer à améliorer la qualité du produit. Le regard est raccordé au boîtier plastique par le biais d’un soudage par ultrasons en vue de créer une jointure de scellage parfaitement étanche. D’autre part, le renoncement à la méthode par adhésif garantit également un résultat visuellement impeccable et crée un assemblage éco-compatible intégralement sans additifs. Un autre critère essentiel en faveur de l’utilisation de la technologie de soudage par ultrasons était la possibilité de surveiller le processus : à travers une surveillance étroite et une validation de chacun des processus de soudage, la machine garantit un niveau de fiabilité de processus sans précédent.
Facteurs clés de succès : formation et conseil
Avec ces deux solutions développées, apra-plast travaille pour la première fois avec la technologie de soudage par ultrasons. Une formation élémentaire approfondie sur le soudage par ultrasons et un conseil en matière de faisabilité financière et technique du projet ont été déterminants dans la prise de décision. En louant une machine, le client a pu effectuer des essais en interne, dans des conditions réelles de production, et se familiariser avec l’utilisation de la technologie à l’avance.
Conclusion:
La solution de soudage développée démontre clairement que l’utilisation des ultrasons vaut également la peine dans le cadre d’une production de lots de petite taille. Une assistance et un accompagnement solides tout au long de la durée du projet représentent alors une condition essentielle afin de pouvoir développer une machine polyvalente. Par comparaison avec des procédés d’assemblage manuels notamment, la technique du soudage par ultrasons offre l’immense avantage de garantir des temps de production plus rapides et une qualité de produit améliorée, ce qui signifie que les clients peuvent concevoir des procédés de fabrication entiers qui soient plus économiques, plus rentables et plus efficaces.