Unlocking the potential of Digitalization with ultrasonic welding
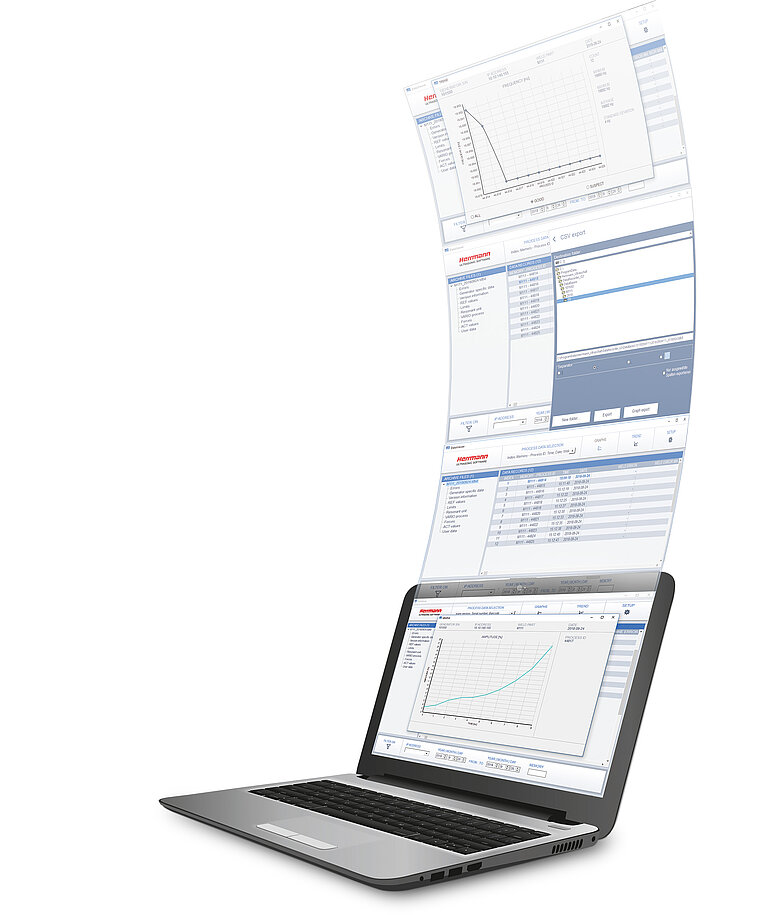
Using the data in battery and wire productions to reduce reject rates and increase efficiency
The most valuable resources in manufacturing are no longer materials or machines. It is the data. Whether in automated systems or at manual workstations: Every welding process of battery cells or wire terminal applications offers the opportunity to collect valuable digital information. For example, it can help to determine the causes of faulty welds in order to avoid them in the future. The challenge for companies is to measure, structure and evaluate the data meaningfully.
Ultrasonic welding is the ideal joining technology for utilizing this digital potential. With direct physical contact between the component and the welding tool, the generator can immediately gather significant information about the process.
To provide easy access to this process data, Herrmann Ultraschall has developed the DataRecorder G3. The software can measure, save and export more than 150 parameters per welding process. In total, up to 5,000 welding processes from a maximum of 16 generators can be recorded simultaneously, seamlessly and safely. This huge amount of data can be used to optimize parameters such as welding time, energy or force to maximize the efficiency of the process end in the long term.
In order to evaluate the data, it is better to have the support of an experienced ultrasonic specialist. Their comprehensive expertise enables the data to be evaluated quickly so that the entire process can be optimized in the shortest possible time. In this way, it is digital information that provides decisive added value for a supposedly purely mechanical welding process.