Welding battery cells safely and sustainably with ultrasonics
Batteries enable emission-free and sustainable mobility, but it's time for battery manufacturing to become sustainable as well. That's why we joined forces with CUSTOMCELLS®, one of the world's leading developers of customized lithium-ion battery cells, to look for new ways to optimize battery production from scratch – and found the solution.
With modern ultrasonic welding machines and the know-how from several decades of ultrasonics, we significantly improve the safety, efficiency and energy balance of the production.
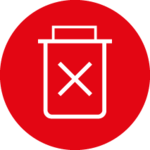
On the way to
0 rejects
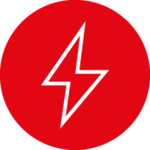
Savings potential of
up to 75 % energy
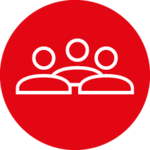
Together to the
ideal welding process
"With Herrmann Ultraschall we have found a reliable partner in the area of safe welded joints at our side. Herrmann's ultrasonic equipment makes a significant contribution to improving our product quality. At Customcells, we highly value sustainability and energy efficiency and are therefore extremely satisfied with the excellent cooperation and the joint implementation of the latest technologies. We can recommend Hermann Ultraschall without any reservation."
Christian Zender, Director Customcells Tübingen GmbH

The challenge
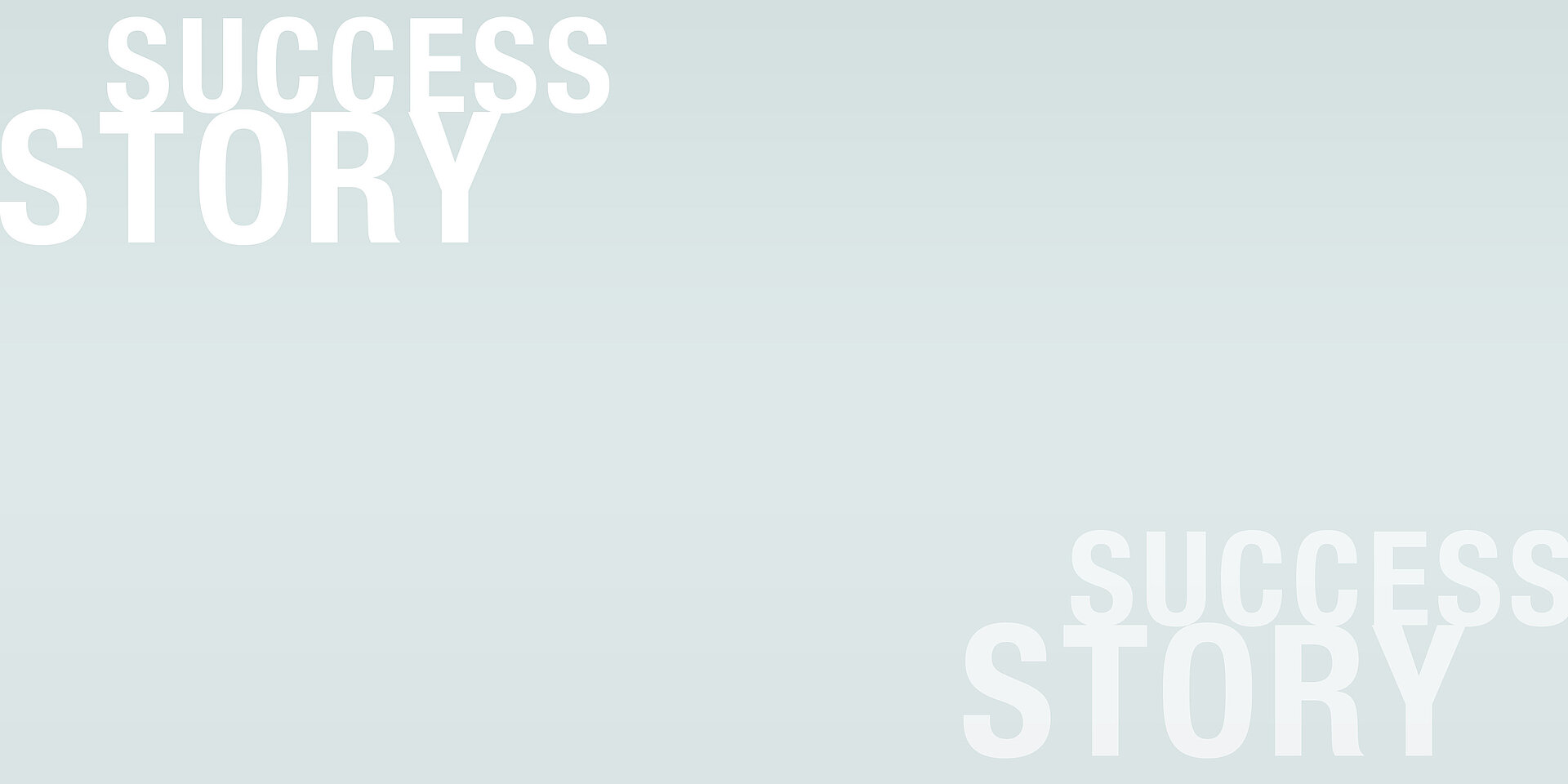
Joining processes such as ultrasonic welding are usually used at the end of battery production. This means that if there are any errors in the process, the entire battery cell has to be disposed of. This leads to high costs in production that can be avoided. Nevertheless, reject rates of up to 20 percent have been accepted in the industry until now.
The ambition of Herrmann Ultraschall and CUSTOMCELLS® is to develop a safe welding process that meets the sustainable demands of the battery industry. This requires a gentle and precise controllable process to avoid damaging the sensitive materials of the battery cells.
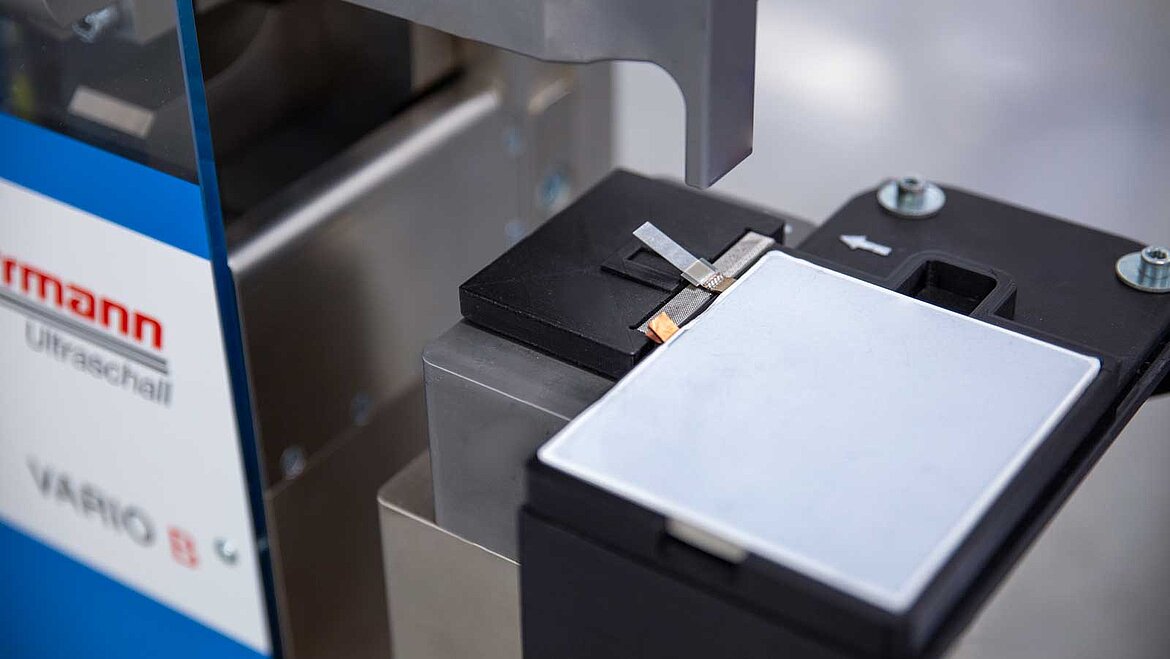
Energy efficient process needed
The status quo in battery production of pouch cells is anything but sustainable: the sensitive materials are often still joined using thermal joining processes such as heat sealing. The energy consumption is high - as is the risk of damaging the materials in the process. Yet there is a safer and more environmentally friendly alternative that is already generating high potential savings in another industry.
Ultrasonics reduces energy consumption
Pouch packaging has been sealed with ultrasonics for decades resulting in enormous benefits for companies. The ultrasonic process saves up to 75 percent energy since the welding tools themselves remain cold. This is because ultrasonics work without any external heat; there is only heat for a short period of time inside the materials due to friction.
Herrmann was able to successfully transfer the knowledge from thousands of solved applications to the welding of pouch cells.
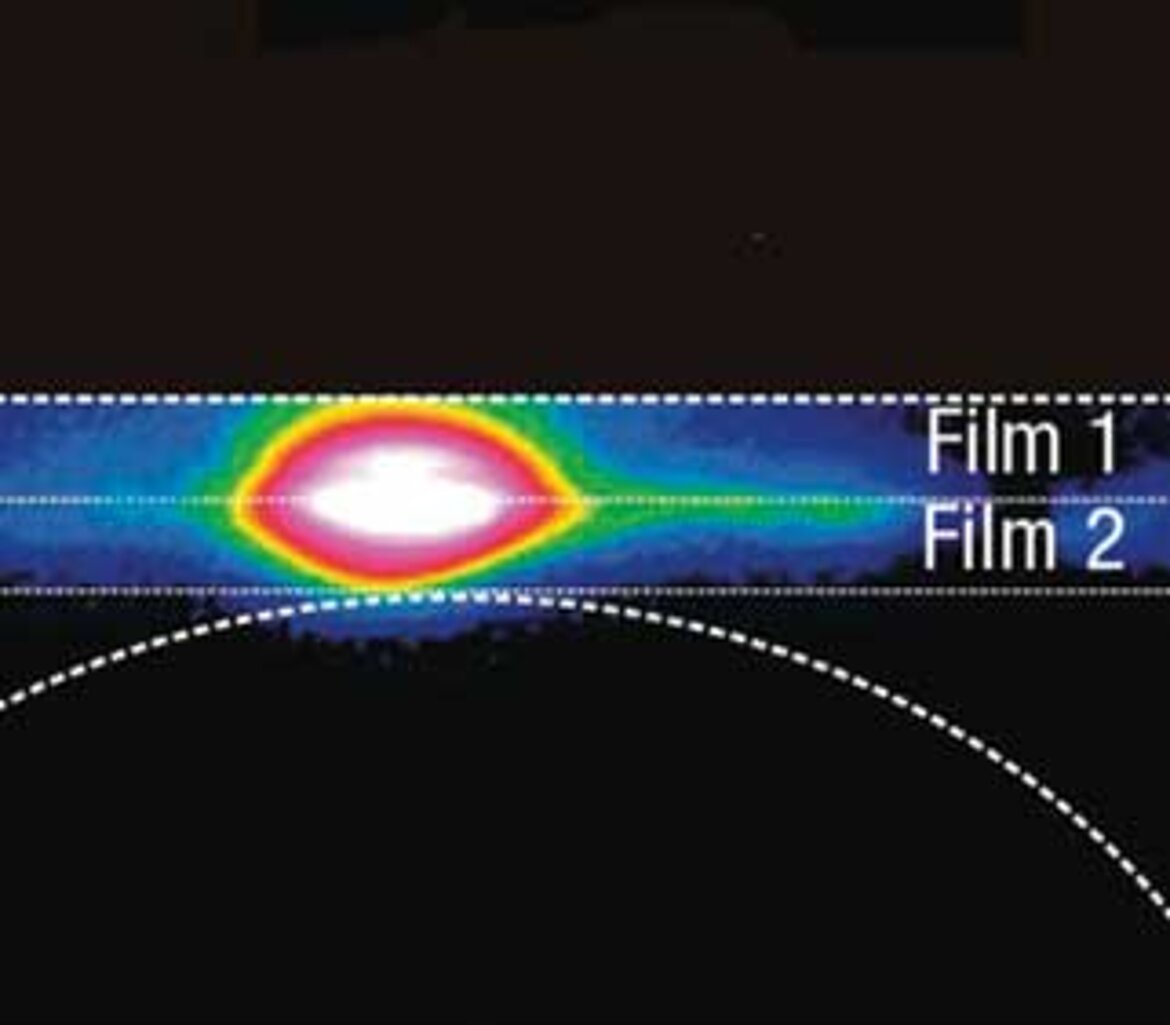
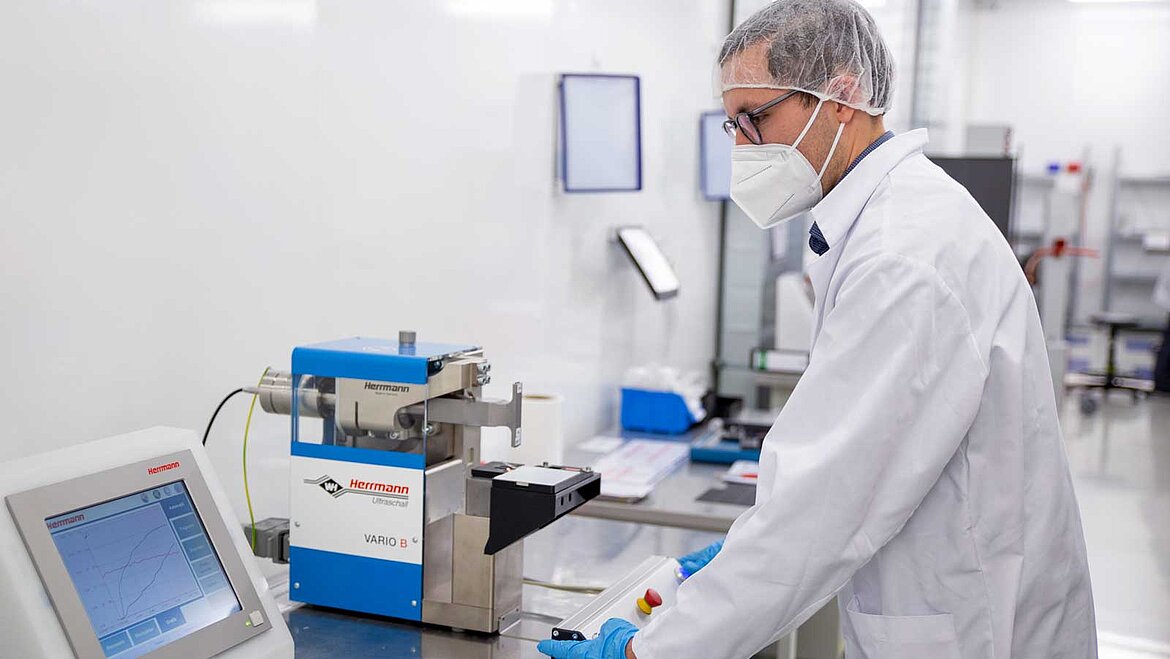
Process data provides security
In the welding of plastics, ultrasonic welding systems from Herrmann already achieve reject rates of close to 0 percent. The key element is the process monitoring: up to 150 different parameters are recorded and documented for each individual weld. The most important of these can be visualized in real time. This ensures reproducible welding results and minimizes rejects.
The same amount of data is also available for each individual ultrasonic welding process of non-ferrous metals. If they are utilized, they form a valuable basis for optimizing the welding process of battery cells to guarantee a constant result. This makes it possible to reduce the reject rate throughout the process – which cuts costs and materials.
The field test
Together with CUSTOMCELLS®, Herrmann has transferred the experience gained from over 60 years of ultrasonics into practice. Here, the machines of the ultrasonics specialist are used for pre-welding and main welding on pouch cells. The unique challenge: the battery cells developed by CUSTOMCELLS® used tabs, which in this welding project are significantly smaller than what is typically used in the industry.
In order to ensure a reliable connection between the tab and the anode or cathode, the sonotrodes of the ultrasonic welding machines were precisely adapted to the respective size of the tabs.
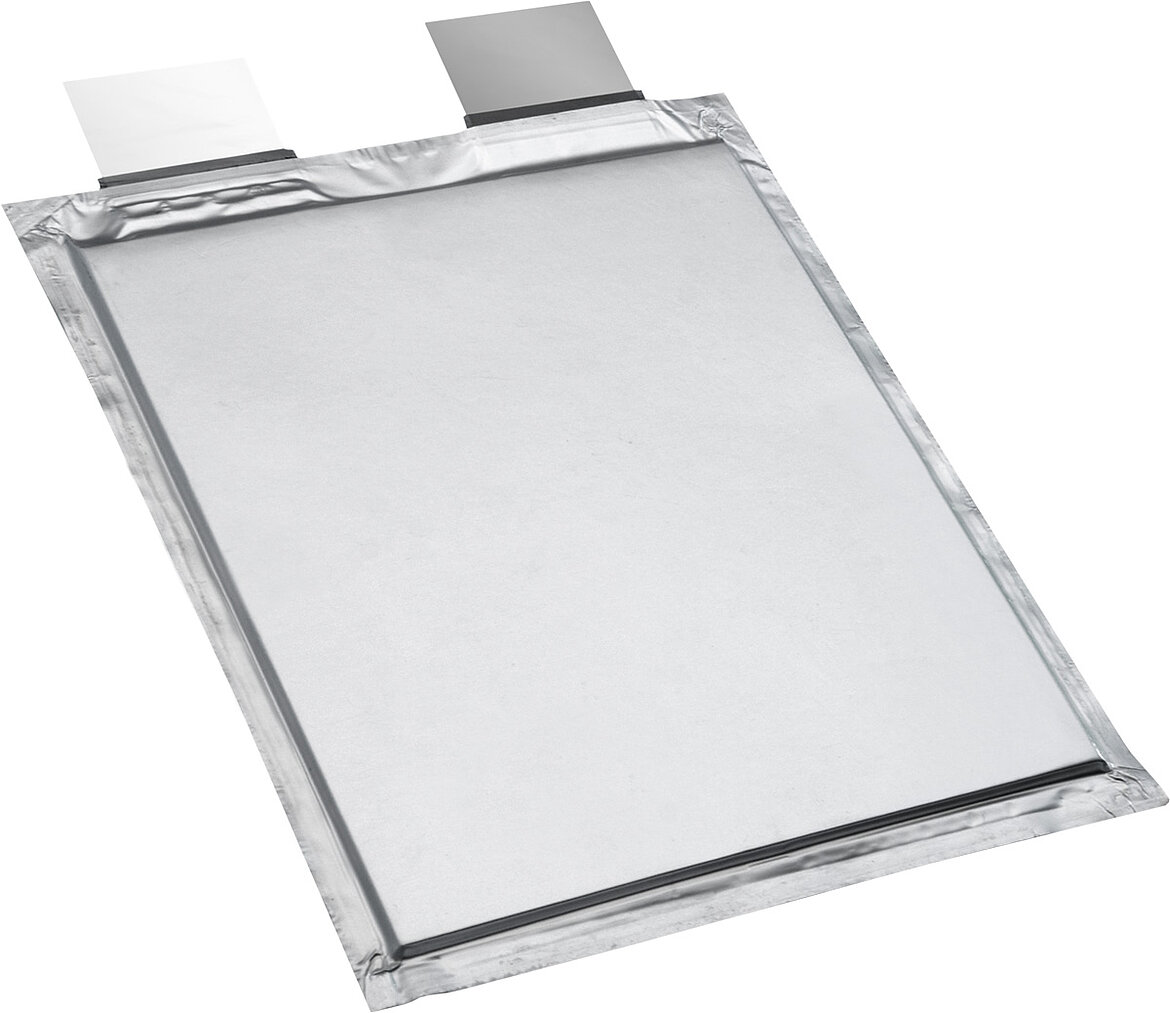
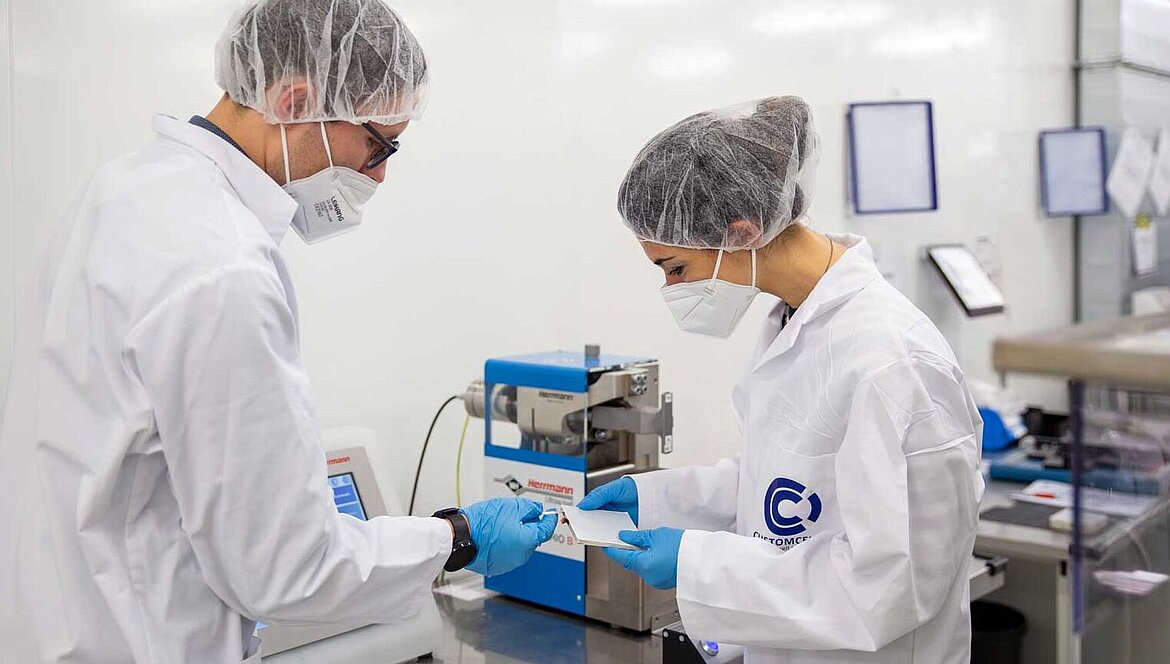
Results from the laboratory confirmed
Welding tests in the ultrasonic laboratory showed that the cells used by CUSTOMCELLS® could be joined safely and gently with a special sonotrode design already developed.
After a short time, the right welding parameters could also be defined. This made it possible to switch to the Herrmann welding systems with virtually no downtime for production. Here, the machines proved to provide a reliable, energy-saving joining process for the battery cells in practice.
Joint development provides an optimized welding process
Ultrasonic welding is the correct technology to achieve strong pouch cell welds with an equally gentle and sustainable joining process. This has been demonstrated through the collaboration with CUSTOMCELLS®, where the advantages of the joining technology could be proven in practice. Throughout the process, it became clear that the several years of experience in ultrasonics, as well as other industries, is extremely valuable to the manufacturing of batteries. This manufacturing process can be made significantly more efficient, safer, and environmentally friendly with the use of ultrasonics.
In addition to experience, qualified advice and flexible service from the ultrasonic partner is needed in order to react immediately to changes in the production process if necessary. The combination of suitable welding solutions and good service forms the basis for smooth production of battery applications with ultrasonics.
Images: © CUSTOMCELLS® - www.customcells.org