Soldadura de metales para la industria de la electromovilidad
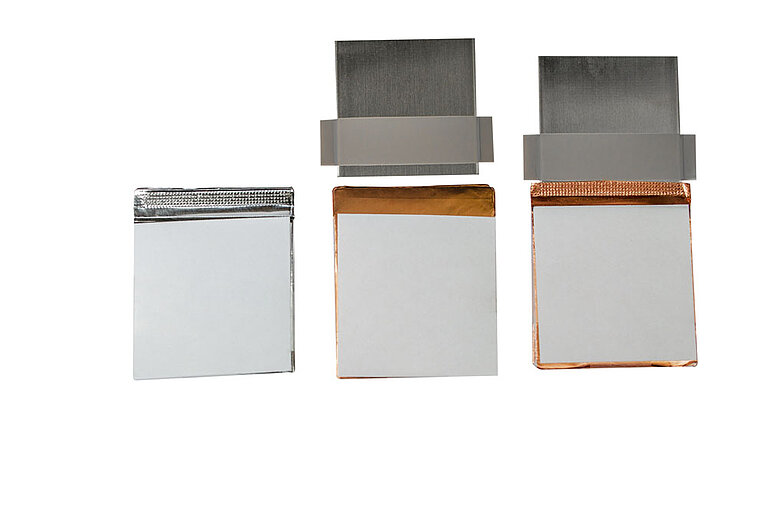
Soldadura por ultrasonido de cobre y aluminio
La soldadura por ultrasonido de metales no ferrosos es un proceso bien establecido y actualmente está en auge por el creciente mercado de las baterías de iones de litio (LIB, por sus siglas en inglés), que ahora son la principal forma de almacenamiento de energía en la industria de la electromovilidad. En Herrmann Ultrasonidos tenemos décadas de experiencia como especialistas en soldadura por ultrasonido, y ahora hemos desarrollado un nuevo sistema de soldadura para metales: el sistema HiS VARIO.
La soldadura por ultrasonido es un proceso limpio, seguro y ecológico que no solo es adecuado para presoldar y soldar ánodos y cátodos en la fabricación de LIB, sino también para elaborar conexiones eléctricas en las industrias de la automoción, bienes de consumo y artículos electrónicos. El proceso puede utilizarse en un puesto de trabajo manual o incorporarse de forma automatizada en las líneas de producción. Las ventajas que ofrece este proceso son las siguientes:
- Alta resistencia
- Tiempos de soldadura breves
- Bajo consumo de energía
- No requiere materiales consumibles
- Las oscilaciones longitudinales deshacen la capa de óxido
La soldadura por ultrasonido se emplea principalmente para unir metales conductivos no ferrosos y metales preciosos con compuestos de cobre-aluminio que constituyan el 90 % de las piezas para soldar. La energía que se requiere para crear la unión se suministra mediante oscilaciones mecánicas. Para ello, el generador de ultrasonido produce vibraciones eléctricas en el rango de 20 o 35 kHz a partir de la corriente alterna de la red de suministro con frecuencia de 50 Hz. Para convertir las vibraciones eléctricas en oscilaciones mecánicas de la misma frecuencia, se emplea un convertidor. La herramienta de soldadura, llamada sonotrodo, transfiere las oscilaciones al par de piezas que han de unirse. El sonotrodo se acopla frente a una de las piezas por unir y hace que oscile longitudinalmente. La otra pieza por unir se sujeta en un yunque estructurado y no se mueve. La superficie de acoplamiento del sonotrodo también debe estar estructurada, pues de otra forma la pieza superior de la unión no se movería, es decir, no se generaría ningún movimiento relativo.
El óxido que recubre los sitios de unión se deshace debido a la fricción intensa, y las dos piezas por unir se funden juntas con uniones moleculares al aplicar sobre ellas presión de forma simultánea. El aspecto determinante de la soldadura no es el calor producido, que es mucho menor al que se requiere para alcanzar el punto de fusión del material, sino el movimiento relativo de ambas piezas por unir. Debido a que en el proceso se genera poco calor, no hay ningún efecto negativo en la estructura del material. El grosor máximo de las piezas que intervienen en la unión suele ser de 2 a 3 mm en el caso de las láminas de cobre y depende de la superficie de soldadura. La potencia requerida es de entre 1000 y 6200 W, en función de la aplicación.
La visualización del proceso es importante
El control del sistema comprueba los parámetros de proceso y genera una representación gráfica de ellos. Esa representación gráfica de los parámetros en la pantalla de la máquina ―que incluye amplitud, energía, recorrido de soldadura y fuerza de soldadura― resulta un instrumento importante para garantizar la estabilidad del proceso. Para cada aplicación debe determinarse una ventana de proceso a fin de compensar las tolerancias del material y de la producción. Todos los pasos del proceso de producción de celdas de la línea de entrada deben tomarse en cuenta en esta etapa. Es importante reducir al mínimo los rechazos, particularmente en el caso de las costosas celdas para baterías. Al determinar los parámetros de soldadura ―es decir, al tomar en cuenta la aplicación, el material y el entorno de producción― resulta esencial pensar de forma holística. Esa es la razón por la que es importante implicar a los proveedores de tecnología de ultrasonidos en el desarrollo del producto tan pronto como sea posible. En Herrmann Ultrasonidos estamos convencidos de que la parametrización fina es una gran oportunidad para seguir mejorando la calidad de la producción y prolongar la vida útil de los sonotrodos. Es ahí donde podemos observar correlaciones entre la estabilidad del proceso y la reducción de las partículas, y entre las entradas de energía, la estabilidad del convertidor y la vida útil de las herramientas de soldadura.
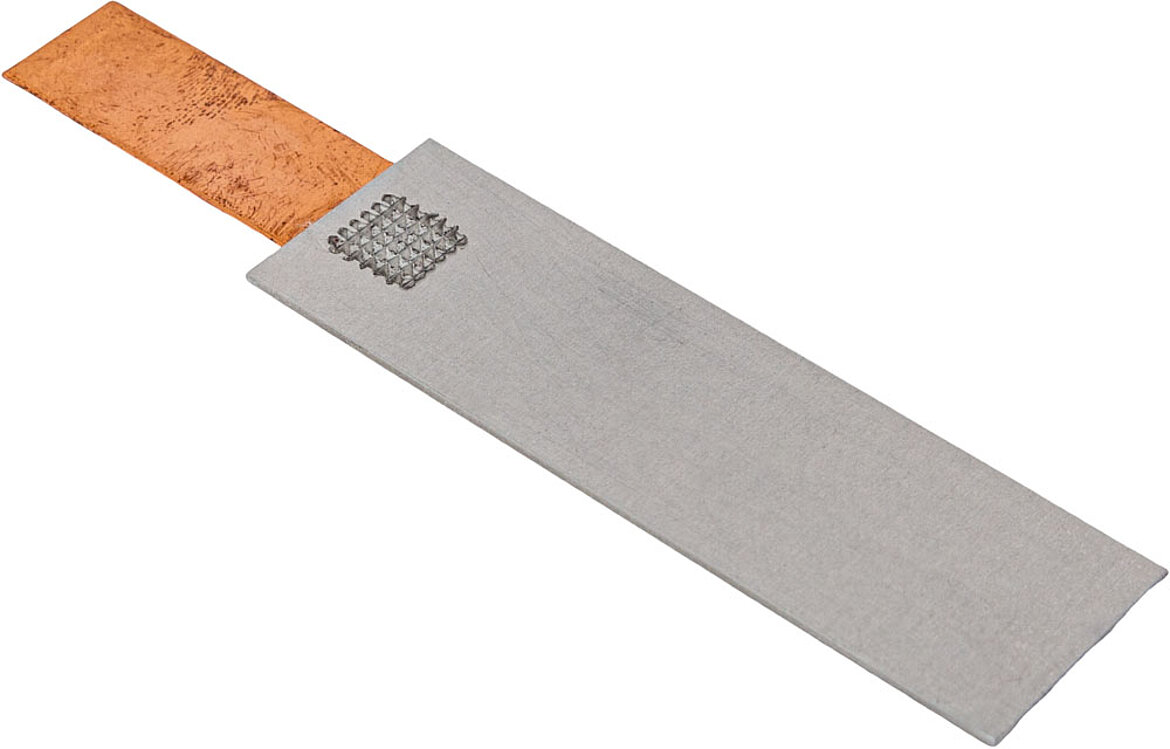
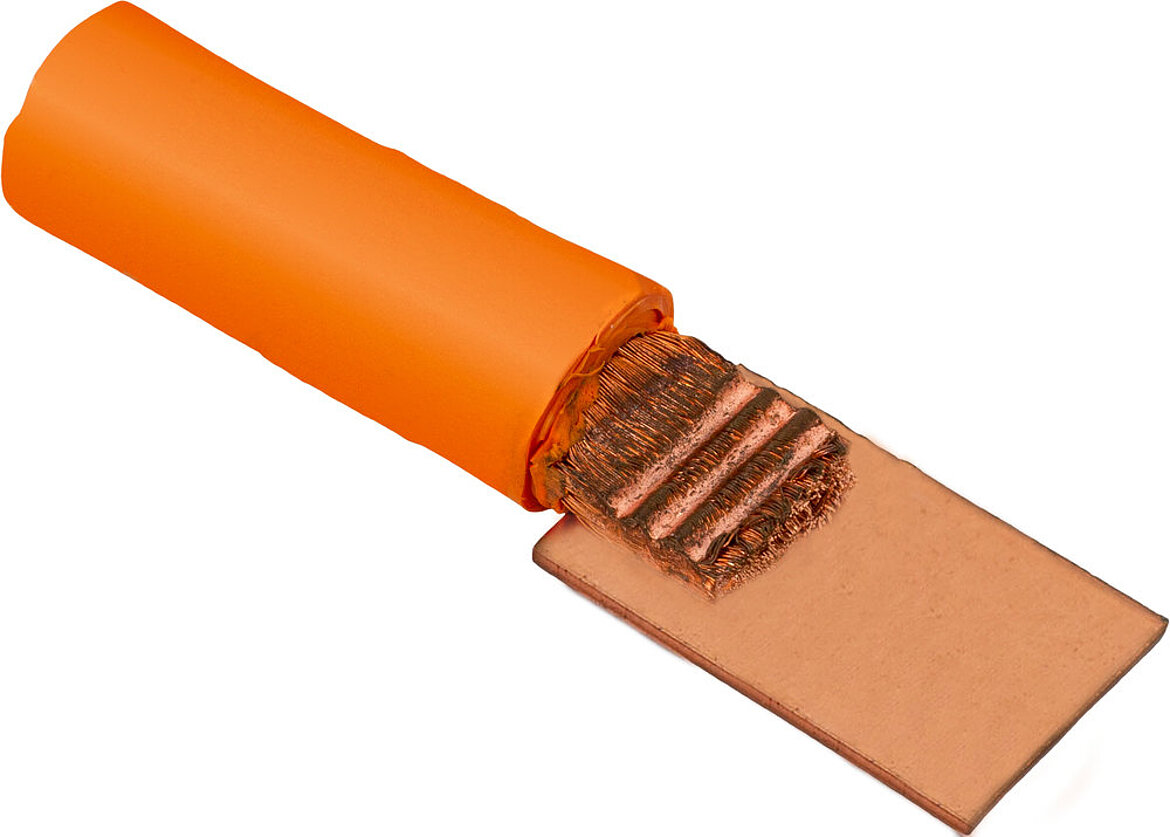
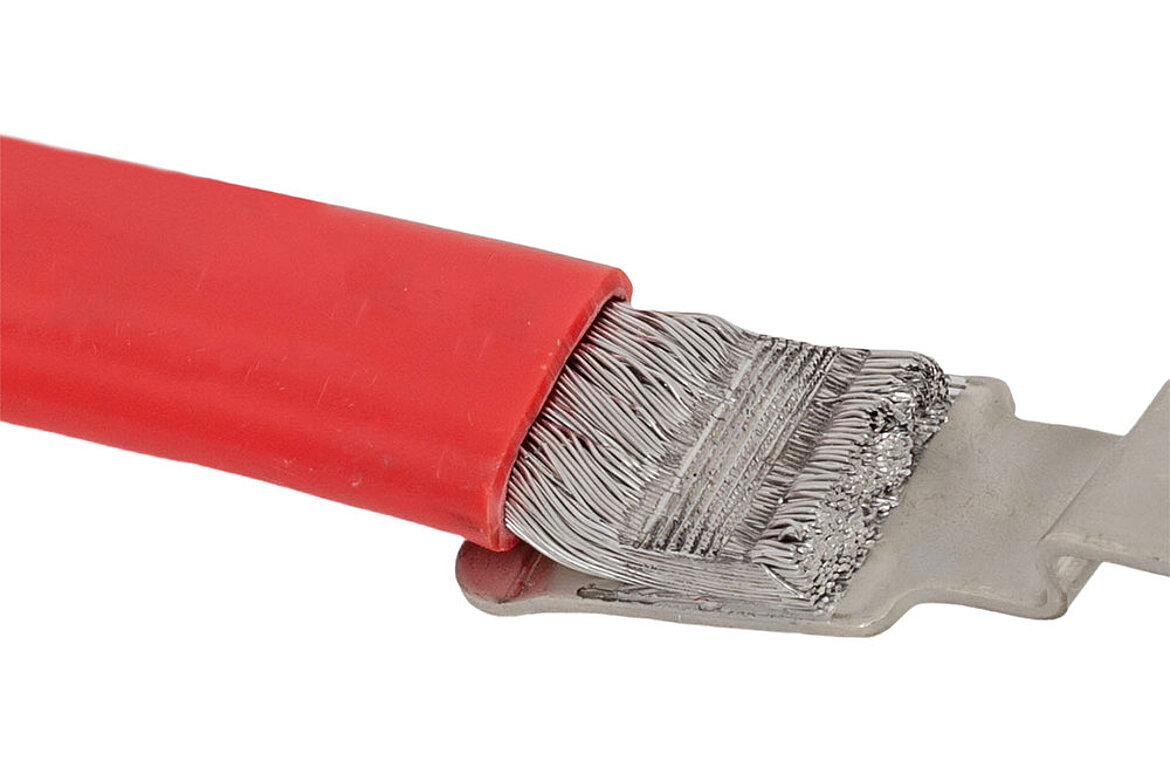
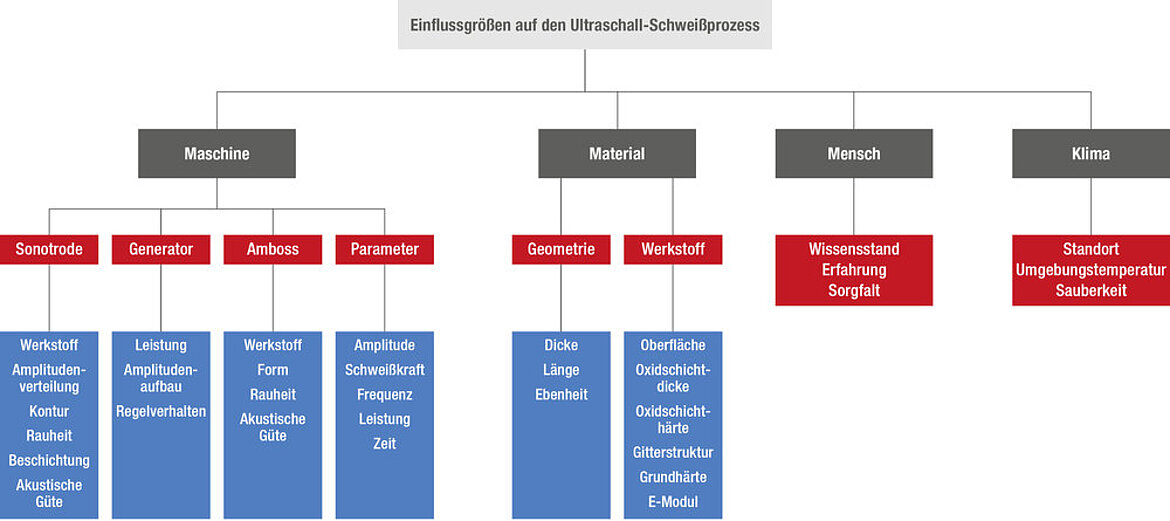