Soft fixture for a hard plastic
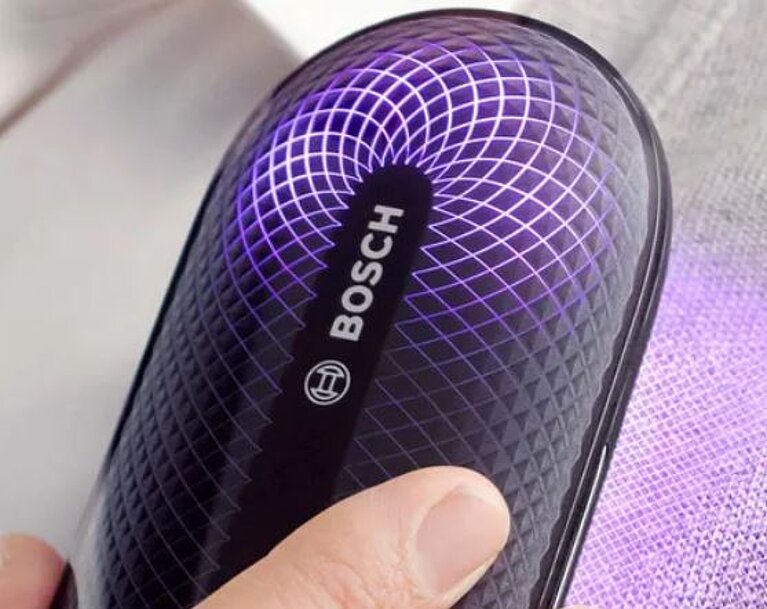
Joining plastic parts under high demands with ultrasonics
Flawless appearance was the major challenge in welding an oval, three-dimensional half case for a consumer product. A joint development process between BSH and Herrmann Ultraschall succeeded in meeting these requirements while also providing strong joints.
BSH Hausgeräte GmbH chose ultrasonics as the most suitable joining technology, as it not only enables strong but also visually appealing connections. Both were deciding factors for the production of the new electronic fabric refresher FreshUp. In order to meet them, Herrmann was involved in the project at an early stage and was able to develop a welding solution together with BSH that completely fulfilled the manufacturer's wishes.
Fixture allows flawless connection
During this development process, the optical requirements in particular put Herrmann's ultrasonic laboratory to the test. The shiny MABS material of the case shells conducts ultrasonics very well, so that strong vibrations not only occur in the joining zone, but also in the entire component during the welding process. This caused marks to appear on the surface at various points where the component lies in the fixture.
To dampen the vibrations of the welding process, the fixture was made of a special casting resin. This is an abrasion-proof, heat-resistant material with a hardness of 80 to 90 Shore - roughly equivalent to the hardness of skateboard wheels. With this factor, the material is hard enough to hold the component in place, but soft enough to dampen the vibrations of the ultrasonics. The low hardness of the resin also allows for subsequent adjustment of its three-dimensional shape. In this way, the ideal fit for the curved component could be created step-by-step by manual polishing and grinding.
Further optimization of the fixture was achieved by dividing it into four fixture segments instead of the usual two. This structure ensures that the component lies cleanly in the fixture and can be welded accurately by the sonotrode. At the same time, the special division prevents damage to the material in the area of the parting lines. Together with the soft casting resin, the fixture reliably prevents visual impairment of the components.
Joint trials per video calls
Another special part of the project was that the design of the components was fixed from the start. This meant that only a small welding path of three tenths of a millimeter was available - about half as much as would normally be used. It was not possible to adapt the injection-molding tool in the area of the energy direction without making changes to the appearance of the case shell.
In order to weld both components flush over the entire length, i.e. on block, the welding process was jointly developed and optimized in an extensive DOE process with several evaluation loops. Primarily the joining speeds graphical representation is used to optimize the process. The tests were carried out in Herrmann's PLASTICS ultrasonic laboratory as well as at the customer's site, and some of them were transmitted via live video. Ultimately, it was also thanks to the close cooperation that the right parameters could be defined to ensure a strong and visually flawless joint under the demanding specifications.
Conclusion
The development of an ultrasonic welding solution for BSH proved how crucial the design of an individually optimized fixture is, in addition to determining the welding parameters. With the right materials and design, it makes a significant contribution to ensuring that components can be joined together not only strongly, but also with a flawless appearance.
About the Bosch FreshUp
The Bosch FreshUp uses Bosch Plasma Technology to remove unpleasant odors, bacteria and viruses from dry clothes without the need to wash them. When the plasma source is activated, the air is ionized directly at the clothing and electrodes are accelerated. Molecular chains are broken and bacteria and viruses are destroyed. This permanently neutralizes odors without the use of chemicals.
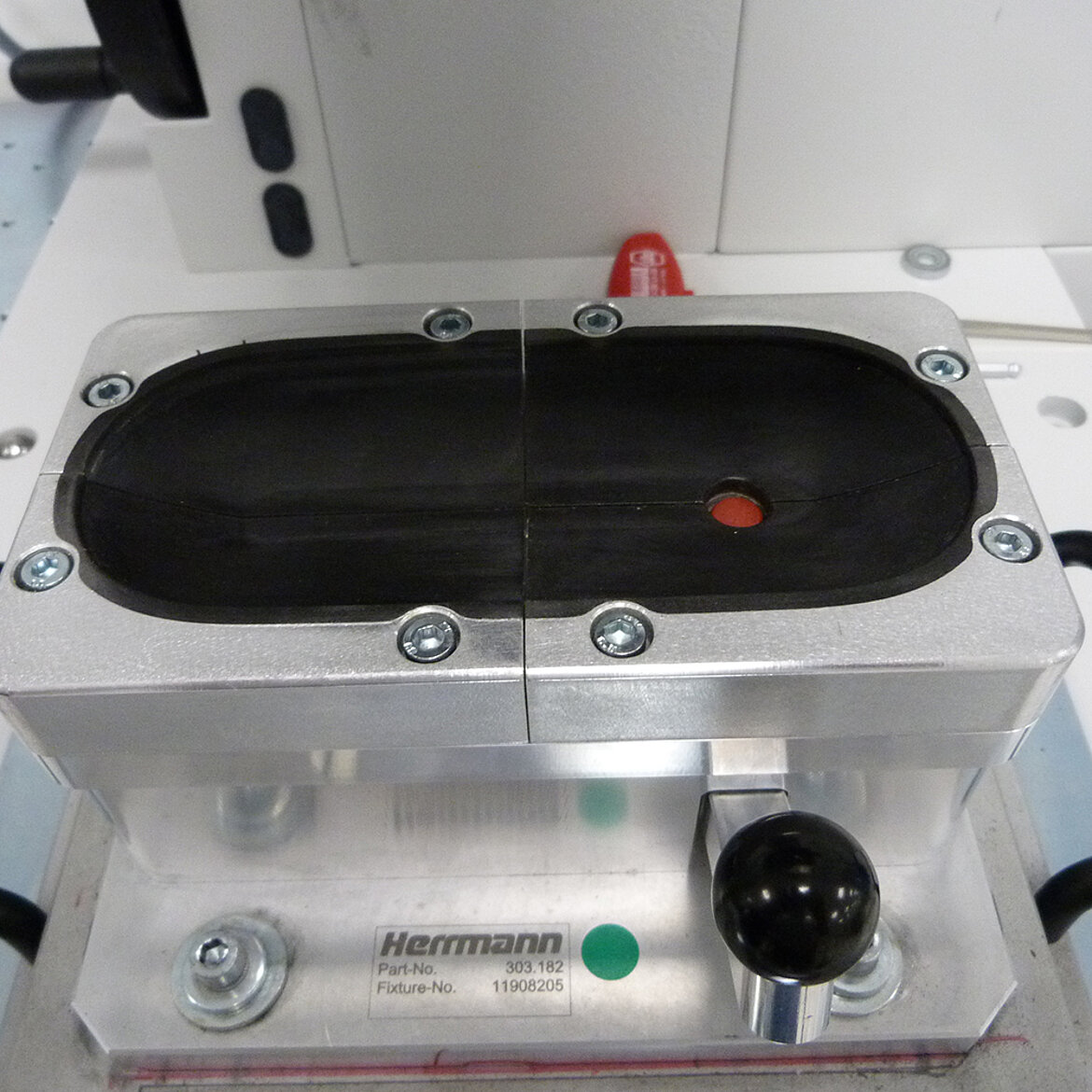