Weiche Werkstückaufnahme für einen harten Kunststoff
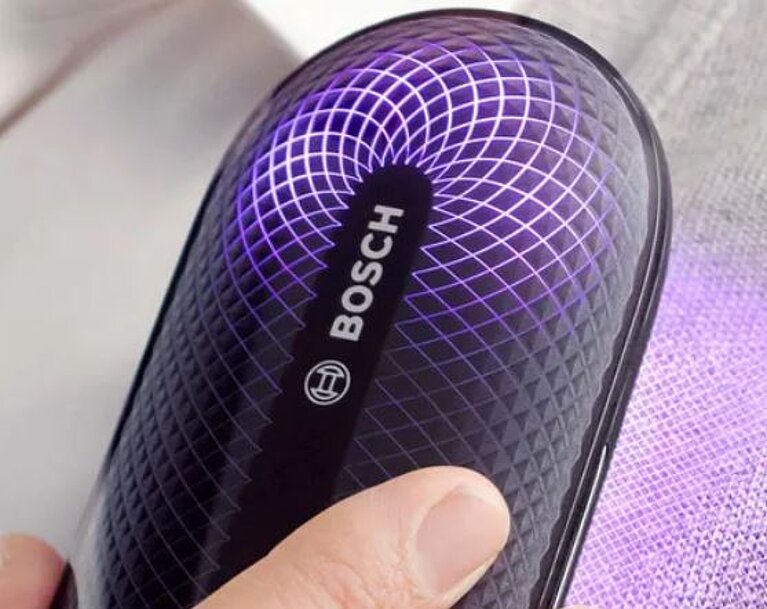
Kunststoffteile unter hohen Ansprüchen mit Ultraschall verbinden
Die einwandfreie Optik war die große Herausforderung bei der Verschweißung einer ovalen, dreidimensionalen Gehäusehälfte für ein Konsumerprodukt. In einem gemeinsamen Entwicklungsprozess von BSH mit der Herrmann Ultraschalltechnik GmbH & Co. KG gelang es, diese Anforderungen bei gleichermaßen festen Verbindungen zu erfüllen.
Die BSH Hausgeräte GmbH entschied sich für Ultraschall als die am besten geeignete Fügetechnologie, da sie nicht nur feste, sondern auch optisch ansprechende Verbindungen ermöglicht. Beides waren maßgebliche Kriterien für die Produktion des neuen elektronischen Textilerfrischers FreshUp. Um sie zu erfüllen, wurde Herrmann bereits früh in das Projekt mit einbezogen und konnte so gemeinsam mit BSH eine Schweißlösung entwickeln, die die Wünsche des Herstellers vollständig erfüllt.
Werkstückaufnahme ermöglicht makellose Verbindung
Im Rahmen dieses Entwicklungsprozesses stellten vor allem die optischen Anforderungen das Ultraschall-Labor von Herrmann auf die Probe. Das glänzende MABS-Material der Gehäuseschalen leitet Ultraschall sehr gut weiter, sodass es nicht nur in der Fügezone, sondern im gesamten Bauteil zu starken Schwingungen während des Schweißprozesses kommt. Dadurch konnten an verschiedenen Stellen, an denen das Bauteil in der Werkstückaufnahme aufliegt, Markierungen an der Oberfläche entstehen.
Um die Vibrationen des Schweißvorgangs zu dämpfen, fertigte man die Werkstückaufnahme aus einem speziellen Gießharz an. Dabei handelt es sich um ein abriebfestes, hitzebeständiges Material mit einer Härte von 80 bis 90 Shore – das entspricht etwa der Härte von Skateboard-Rollen. Mit diesem Faktor ist das Material hart genug, um das Bauteil zu fixieren, aber weich genug, um die Vibrationen des Ultraschalls abzudämpfen. Die geringe Härte des Harzes ermöglicht außerdem die nachträgliche Anpassung seiner dreidimensionalen Form. So konnte durch händisches Polieren und Abschleifen Schritt für Schritt die ideale Passform für das gewölbte Bauteil geschaffen werden.
Eine weitere Optimierung der Werkstückaufnahme erreichte man durch ihre Unterteilung in vier statt wie üblich nur zwei Aufnahmen-Segmente. Durch diese Struktur konnte sichergestellt werden, dass das Bauteil sauber in der Werkstückaufnahme liegt und treffgenau von der Sonotrode geschweißt werden kann. Gleichzeitig verhindert die besondere Aufteilung, dass es im Bereich der Trennebenen zu Beschädigungen am Material kommt. In Verbindung mit dem weichen Gießharz verhindert die Werkstückaufnahme damit zuverlässig optische Beeinträchtigungen der Bauteile.
Gemeinsame Versuche per Video-Schaltung
Eine weitere Besonderheit des Projekts bestand darin, dass das Design der Bauteile von Beginn an festgelegt war. Dadurch stand nur ein geringer Schweißweg von drei Zehntel Millimeter zur Verfügung – ungefähr nur halb so viel, wie normalerweise genutzt werden sollte. Eine Anpassung des Spritzgusswerkzeuges im Bereich des Energierichtungsgebers war nicht möglich, ohne Veränderungen am Aussehen der Gehäuseschale vorzunehmen.
Um beide Bauteile über die gesamte Länge absolut bündig, das heißt auf Block zu verschweißen, wurde der Schweißprozess in einem längeren DOE-Prozess mit mehreren Evaluierungsschleifen gemeinsam entwickelt und optimiert. Es ist vor allem die Fügegeschwindigkeit, deren grafische Darstellung bei der Optimierung unterstützt. Die Versuche wurden im Herrmann Ultraschall-Labor PLASTICS sowie beim Kunden vor Ort durchgeführt und teils per Live-Video übertragen. Letztlich konnten auch dank der engen Zusammenarbeit die richtigen Parameter definiert werden, um unter den anspruchsvollen Vorgaben eine feste und optisch einwandfreie Verbindung zu gewährleisten.
Fazit
Die Entwicklung einer Ultraschall-Schweißlösung für BSH bewies, wie entscheidend neben der Ermittlung der Schweißparameter auch die Gestaltung einer individuell optimierten Werkstückaufnahme ist. Mit den richtigen Materialien und dem passenden Design trägt sie maßgeblich dazu bei, dass Bauteile nicht nur fest, sondern auch mit makellosem Erscheinungsbild miteinander verbunden werden können.
Über den Bosch FreshUp
Der Bosch FreshUp entfernt mit Hilfe der Bosch Plasma Technology unangenehme Gerüche, Bakterien und Viren aus trockenen Kleidungsstücken, ohne dass diese gewaschen werden müssen. Bei Aktivierung der Plasmaquelle wird die Luft direkt am Kleidungsstück ionisiert und Elektroden beschleunigt. Die Molekülketten brechen auf, Bakterien und Viren werden zerstört. Dadurch werden Gerüche dauerhaft und ohne den Einsatz von Chemikalien neutralisiert.
![[Translate to Global - Deutsch:]](/fileadmin/_processed_/9/f/csm_BSH_Werkstueckaufnahme_01_08b89c43da.jpg)