Alojamiento suave para un plástico duro
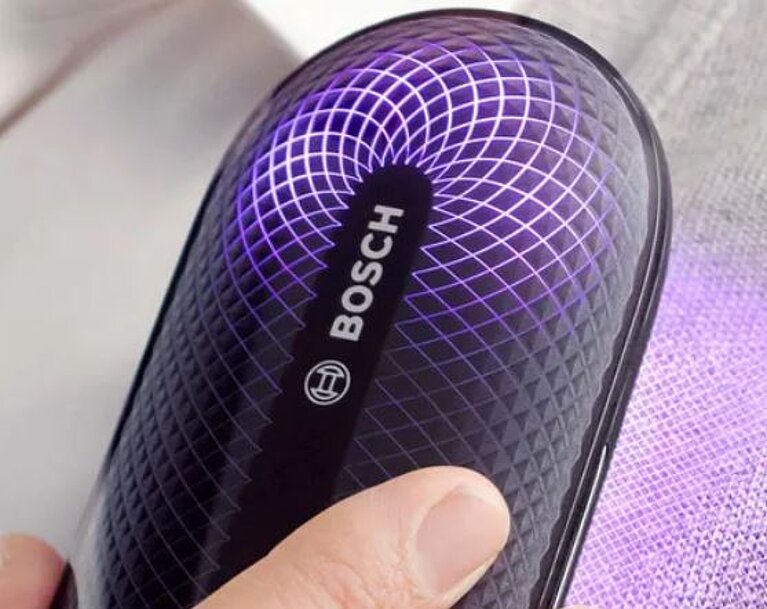
Unión de piezas de plástico conforme a altas exigencias mediante ultrasonidos
La apariencia impecable fue el reto principal al soldar la mitad de una carcasa ovalada tridimensional de un producto de consumo. Un proceso de desarrollo conjunto entre BSH y Herrmann Ultraschall logró satisfacer estos requisitos y a la vez produjo uniones firmes.
BSH Hausgeräte GmbH eligió los ultrasonidos como la tecnología de unión más adecuada, pues las conexiones que los ultrasonidos permiten obtener no solo son firmes, sino también visualmente atractivas. Ambos factores fueron decisivos para la producción del nuevo higienizador electrónico de telas FreshUp. Para satisfacer esos factores, Herrmann se involucró en el proyecto en una de las etapas iniciales y pudo desarrollar junto con BSH una solución de soldadura que cumplió por completo los deseos del fabricante.
El alojamiento de la pieza permite obtener conexiones impecables
Los requisitos estéticos, en particular, pusieron a prueba las capacidades del laboratorio de ultrasonido de Herrmann durante este proceso de desarrollo. El lustroso material MABS de las piezas de la carcasa conduce muy bien los ultrasonidos, por lo que las oscilaciones intensas no solo ocurren en la zona de unión, sino también en todo el componente durante el proceso de soldadura. Eso hizo que aparecieran marcas sobre la superficie, en varios puntos donde el componente se apoya en el alojamiento.
Para amortiguar las oscilaciones del proceso de soldadura, el alojamiento se fabricó con una resina de moldeo especial. Esta resina es un material resistente a la abrasión y al calor con dureza de 80 a 90 en la escala de Shore, que equivale aproximadamente a la dureza de las ruedas de patineta. Con este factor, el material es lo suficientemente duro para sostener el componente en su lugar, pero lo suficientemente suave para amortiguar las oscilaciones de los ultrasonidos. La baja dureza de la resina también permite hacer ajustes subsecuentes de su forma tridimensional. De ese modo, se pudo crear el ajuste ideal para el componente curvo paso a paso desbastando y puliendo el material manualmente.
Se logró una mayor optimización del alojamiento al dividirlo en cuatro segmentos, en vez de los dos habituales. Esta estructura permite que el componente quede colocado adecuadamente en el alojamiento y que el sonotrodo pueda soldarlo con precisión. Al mismo tiempo, la división especial evita que el material se dañe en la zona de las líneas de separación. Junto con la resina de moldeo suave, el alojamiento evita de forma fiable que los componentes tengan defectos estéticos.
Pruebas conjuntas por videoconferencia
Otro aspecto especial del proyecto fue que el diseño de los componentes se estableció desde el inicio. Eso significó que solo se disponía de una pequeña ruta de soldadura de tres décimas de milímetro, que es, más o menos, la mitad de lo que suele usarse normalmente. No era posible adaptar la herramienta de moldeo por inyección en la zona a la que se dirige la energía sin hacer cambios en la apariencia de las piezas de la carcasa.
Para soldar ambos componentes enrasados en toda su longitud, es decir, en bloque, el proceso de soldadura se desarrolló y optimizó de forma conjunta en un amplio proceso de diseño de experimentos con varios ciclos de evaluación. Primero se usó la representación gráfica de las velocidades de unión para optimizar el proceso. Las pruebas se llevaron a cabo en el laboratorio de ultrasonido de la división PLASTICS de Herrmann, así como en el emplazamiento del cliente, y algunas de ellas se transmitieron por videoconferencia en vivo. Por último, y también gracias a la cooperación estrecha entre ambas empresas, fue posible definir los parámetros correctos para lograr una unión firme y visualmente impecable conforme a las exigentes especificaciones.
Conclusión
El desarrollo de una solución de soldadura por ultrasonido para BSH demostró la importancia esencial del diseño de un alojamiento optimizado individualmente, además de la determinación de los parámetros de soldadura. Con los materiales y el diseño adecuados, la solución contribuye de forma significativa a lograr que los componentes puedan unirse no solo con firmeza, sino también con una apariencia impecable.
Acerca del higienizador FreshUp de Bosch
El higienizador FreshUp de Bosch utiliza la tecnología de plasma de Bosch para eliminar olores desagradables, bacterias y virus de la ropa seca sin necesidad de lavarla. Cuando se activa la fuente de plasma, el aire se ioniza directamente en la ropa y los electrodos se aceleran, lo cual rompe cadenas moleculares y destruye bacterias y virus. Así, los olores se neutralizan de forma permanente sin el uso de sustancias químicas.
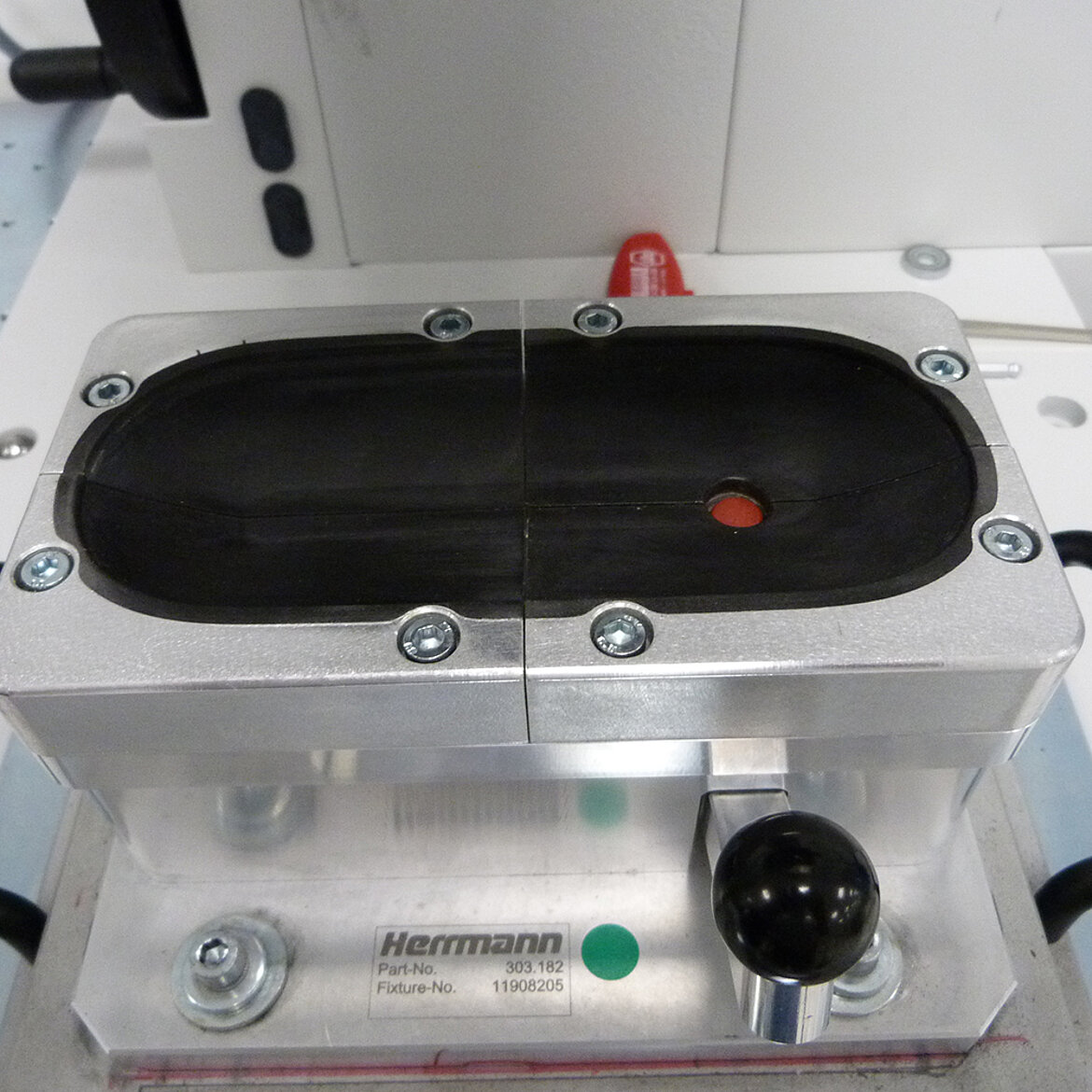