Process control is the essential factor
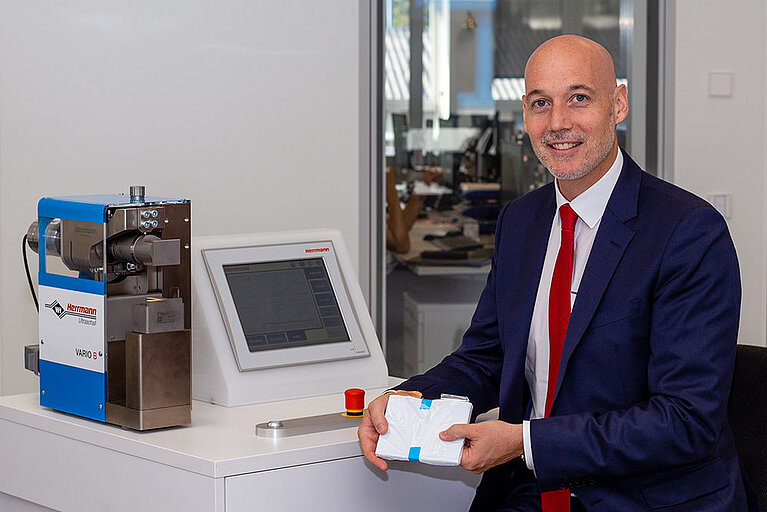
Interview with CEO Thomas Herrmann and Business Unit Director André Deponte
You have been a specialist for plastic welding. Why metals now?
Thomas Herrmann: The requests of our plastics customers, who also need to weld metal connections, have become more and more. We realized that we can easily apply our decades of experience in process optimization to the field of metals. In addition, a completely new market potential is opening up, especially due to E-mobility.
What have been the “pain points” so far in ultrasonic welding of nonferrous metals?
André Deponte: With the existing solutions, customers mainly complain about the lack of process stability and the high tool wear, because metal comes in contact with metal. There is no damping of the ultrasonic waves as is the case with plastics, so that the process is highly abrasive. One rule of thumb seems to hold true: depending on the material, the sonotrode (weld tool) made of steel is worn after 100,000 shots and needs to be replaced. This makes up a service life of two weeks. If you take into account the long tool change and start-up times, you will loose valuable production time and generate costly production waste. Equally as important is the reduction of generation of particles. The fewer particles form during welding, the loser is the risk of short circuits and the higher the safety in production.
You have developed two machines for welding of metals. What is new?
André Deponte: We have advanced our tried and tested process parameterization and visualization to address the “pain points”. The more accurately you can control the process, the more stable and particle-free it becomes. For this purpose, we have done research in terms of the correlation between the amounts of energy and standstill times. We want to increase the service life of the tools and thus have developed a tool change system that reduces setup times. Previous tool change times of up to 2 hours are intended to be undershot by a multiple. Our goal is 10 minutes – that would be quite revolutionary. We have invested much time into design to ensure a more compact design of the machines and modules and more intuitive handling.
What is your market entry strategy?
Thomas Herrmann: We are launching two machine types – both are so-called spot welders – a machine specially developed for battery applications, on the one hand, and the cable-terminal machine, on the other. Our declared objective is to generate added value for our customers. This already begins during the consulting phase and ranges to better process control through to faster, repeatable tool change. At the moment we are undergoing the field test phase and we have set high goals. We are just about to be specified by the first customers and then we are ready to go.
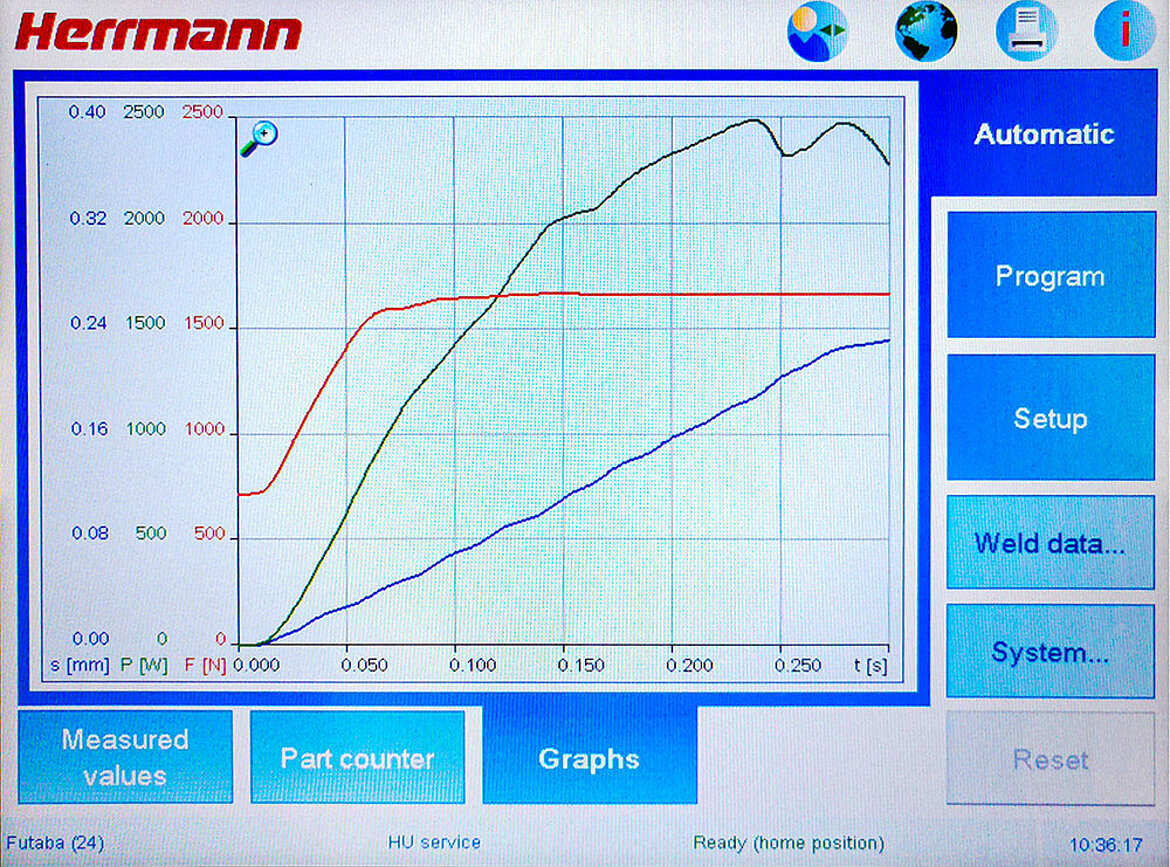
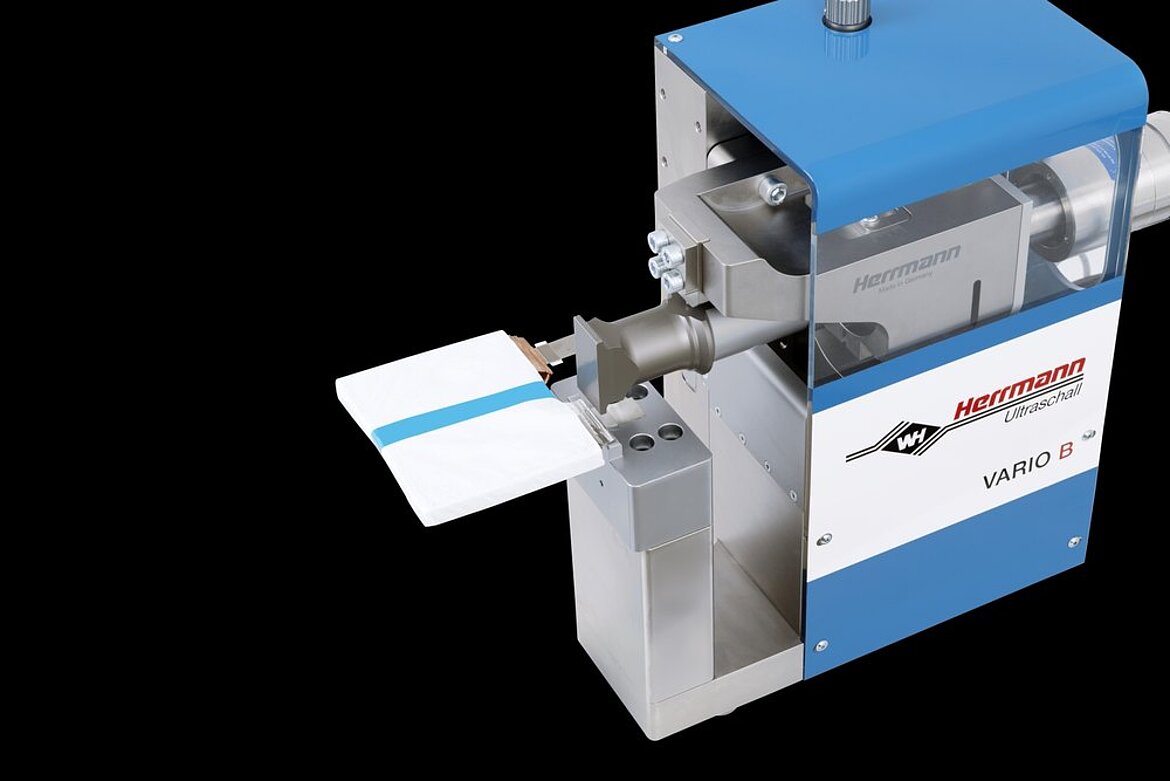