O controle do processo é o fator essencial
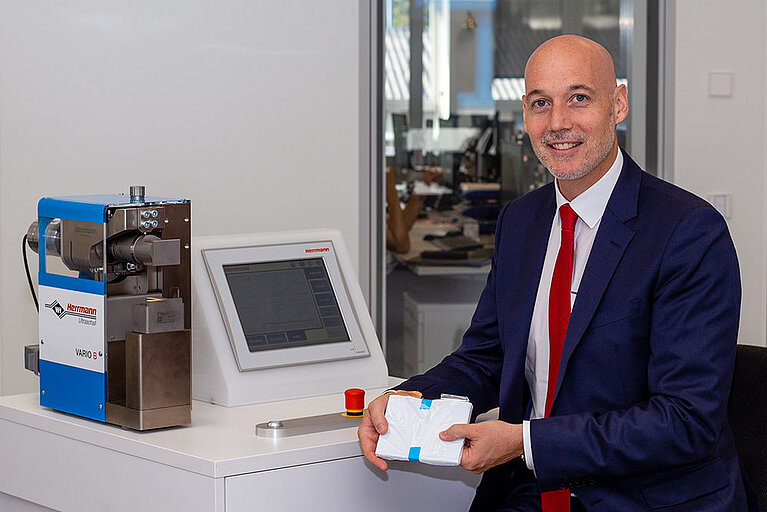
Entrevista com o CEO Thomas Herrmann e o Diretor da Unidade de Negócios André Deponte
Você é um especialista em soldagem de plásticos. Por que metais agora?
Thomas Herrmann: Os pedidos de nossos clientes de plásticos, que também precisam soldar conexões de metal, tornaram-se cada vez mais frequentes. Percebemos que podemos aplicar facilmente nossa décadas de experiência em otimização de processos no campo dos metais. Além disso, um mercado potencial completamente novo está se abrindo, especialmente devido à eletromobilidade.
Quais têm sido os "pontos problemáticos" até o momento no que diz respeito à soldagem por ultrassom de metais não ferrosos?
André Deponte: Com as soluções existentes, os clientes reclamam principalmente da falta de estabilidade do processo e do alto desgaste das ferramentas, pois o metal entra em contato com metal. Não há amortecimento das ondas ultrassônicas, como no caso dos plásticos, de modo que o processo é altamente abrasivo. Uma regra parece ser verdadeira: dependendo do material, o sonotrodo (ferramenta de soldagem) feita de aço fica desgastado após 100 mil disparos e precisa ser substituído. Isso representa uma vida útil de duas semanas. Se considerar os longos períodos de tempo de troca de ferramenta e inicialização, será perdido um tempo valioso na produção e isso gerará desperdício de produção, que é caro. Igualmente importante é a redução na geração de partículas. Quanto menos partículas se formarem durante a soldagem, menor será o risco de curto-circuito e, consequentemente, maior será a segurança na produção.
Você desenvolveu duas máquinas para soldagem de metais. Qual é a novidade?
André Deponte: Avançamos em nossa parametrização e visualização do processo testado e comprovado para abordar os "pontos problemáticos". Quanto mais puder controlar o processo com precisão, mais estável e livre de partículas ele se tornará. Para isso, pesquisamos a correlação entre as quantidades de energia e os tempos de paralisação. Queremos aumentar a vida útil das ferramentas e, portanto, desenvolvemos um sistema de substituição de ferramentas que reduz os tempos de configuração. Tempos de anteriores de substituição da ferramenta de até 2 horas devem ser alcançados por um múltiplo. Nossa meta é 10 minutos, isso seria bastante revolucionário. Investimos muito tempo na versão para garantir uma versão mais compacta das máquinas e módulos e um manuseio mais intuitivo.
Qual é sua estratégia de entrada no mercado?
Thomas Herrmann: Estamos lançando dois tipos de máquina, ambas são chamadas de soldadoras por pontos, por um lado, são máquinas especialmente desenvolvidas para aplicações por bateria, e por outro, a máquina de terminal por caso. Nosso objetivo declarado é gerar valor agregado aos nossos clientes. Isso começa já durante a fase de consultoria e abrange desde um controle melhor do processo até uma substituição mais rápida e repetível da ferramenta. No momento, estamos em fase de testes de campo e definimos metas altas. Estamos prestes a sermos estabelecidos pelos clientes e, então, estamos prontos para começar.
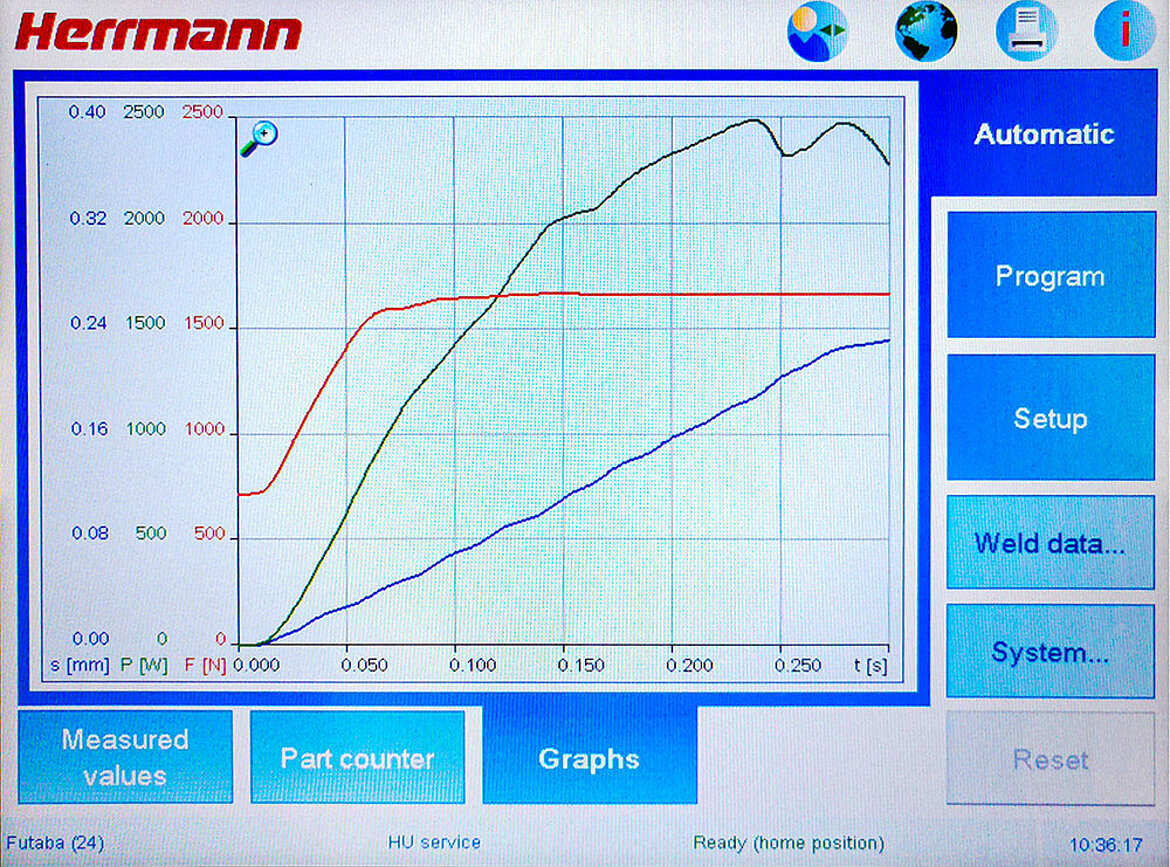
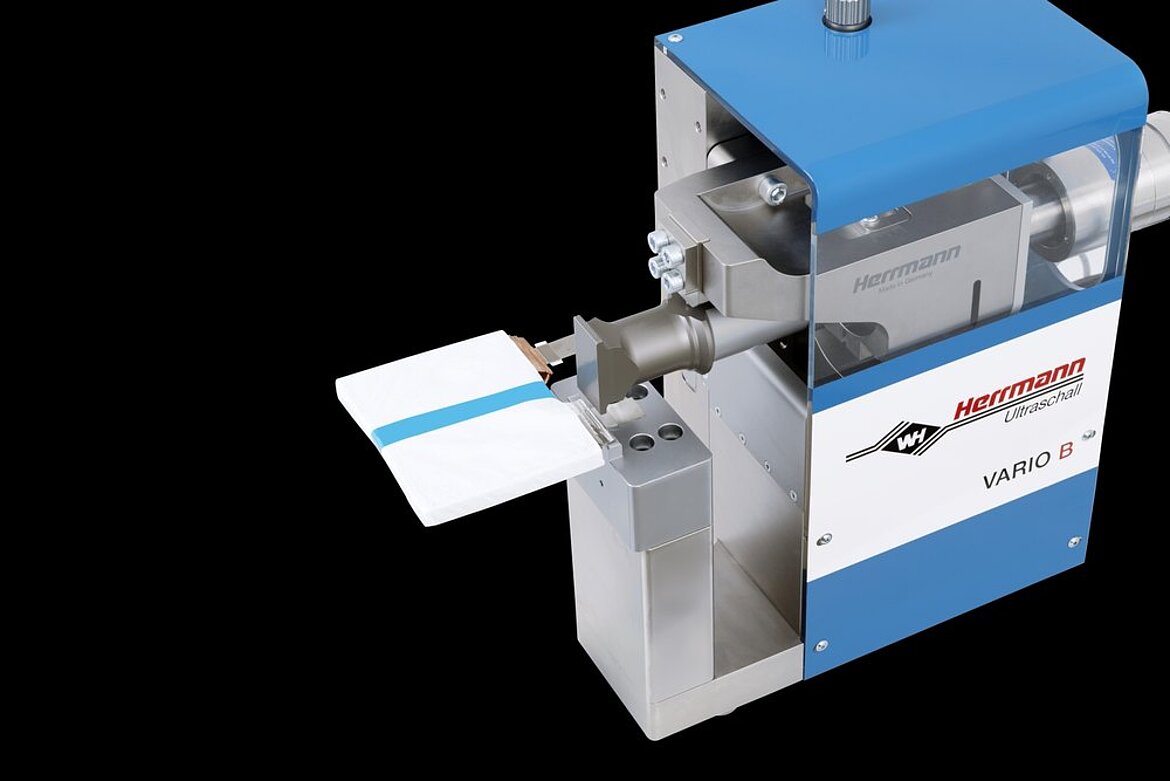