Prozessbeherrschung ist das A und O
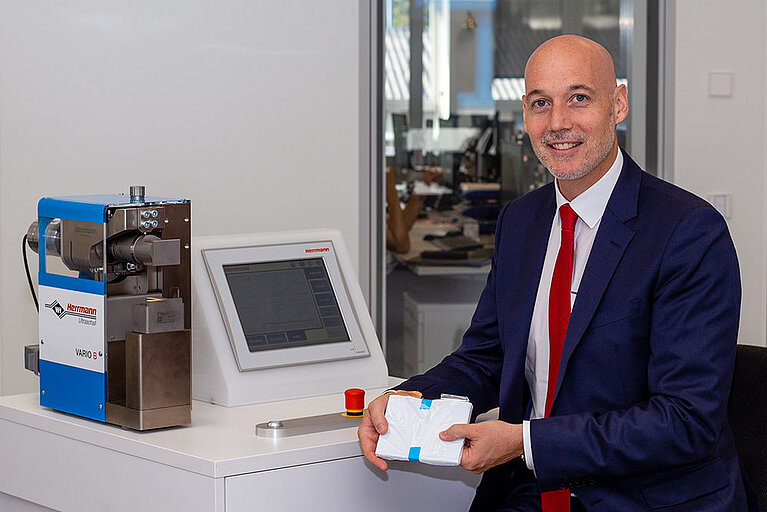
Interview mit CEO Thomas Herrmann und Geschäftsbereichsleiter André Deponte
Sie sind Spezialist für das Kunststoffverschweißen. Wieso jetzt Metalle?
Thomas Herrmann: Die Anfragen unserer Kunststoffkunden, die auch Metallverbindungen schweißen müssen, haben sich gehäuft. Wir haben realisiert, dass wir unsere jahrzehntelange Erfahrung in der Prozessoptimierung gut auf Metalle übertragen können. Zudem erschließt sich gerade durch die Elektromobilität ein ganz neues Marktpotential.
Was sind bisher die „Pain Points“ beim Ultraschallverschweißen von Nichteisenmetallen?
Andre Deponte: Die Kunden klagen bei bestehenden Lösungen neben mangelnder Prozessstabilität über den hohen Werkzeugverschleiß, da Metall eben Metall berührt. Es erfolgt keine Dämpfung der Ultraschallwellen, wie das bei Kunststoffen der Fall ist, sodass der Prozess sehr abrasiv ist. Eine Faustregel scheint zu stimmen: je nach Material ist die Sonotrode (Schweißwerkzeug) aus Stahl nach 100.000 Schuss verschlissen und muss gewechselt werden. Dies läuft auf eine Lebensspanne von zwei Wochen hinaus. Bedenkt man noch die langen Werkzeugwechsel- und Anlaufzeiten, verliert man viel wertvolle Produktionszeit und generiert kostspieligen Produktionsabfall. Genauso wichtig ist die Reduzierung der Partikelbildung. Je weniger Partikel sich beim Schweißen bilden, umso geringer die Gefahr einer Kurzschlusses und umso mehr Sicherheit in der Produktion.
Sie haben zwei Maschine für das Verschweißen von Metallen entwickelt. Was ist neu?
Andre Deponte: Wir haben unsere bewährte Prozess-Parametrierung und –Visualisierung weiterentwickelt, um die „Pain Points“ zu adressieren. Je feiner Sie den Prozess steuern, umso stabiler und partikelfreier wird er. Dazu erforschen wir Korrelationen zwischen der Energiemenge und den Standzeiten. Wir wollen die Lebensdauer der Werkzeuge verlängern und haben dazu ein Werkzeugwechselsystem entwickelt, dass die Rüstzeiten verringert. Bisherige Wechselzeiten von bis zu 2 Stunden wollen wir um ein Vielfaches unterbieten. Unser Ziel sind 10 Minuten – das wäre ziemlich revolutionär. Dazu floß viel Zeit in das Design, um die Maschinen und Module kompakter zu konstruieren und eine intuitivere Handhabung zu gewährleisten.
Was ist Ihre Markteintrittsstrategie
Thomas Herrmann: Wir sind mit zwei Maschinentypen am Start – beides sogenannte Spotwelder – einerseits eine speziell für Batterieanwendungen entwickelte Maschine und die Kabel-Terminal-Maschine. Unser erklärtes Ziel ist es, dem Kunden einen Mehrwert zu genieren. Das fängt in der Beratungsphase an und geht über die bessere Prozessbeherrschung bis hin zu einem schnelleren, reproduzierbaren Werkzeugwechsel. Momentan befinden wir uns in der Feldtestphase und haben uns hohe Ziele gesteckt. Wir sind kurz davor, von den ersten Kunden spezifiziert zu werden und dann geht es los.
-
NEWS Metalle schweißen für E-Mobilität
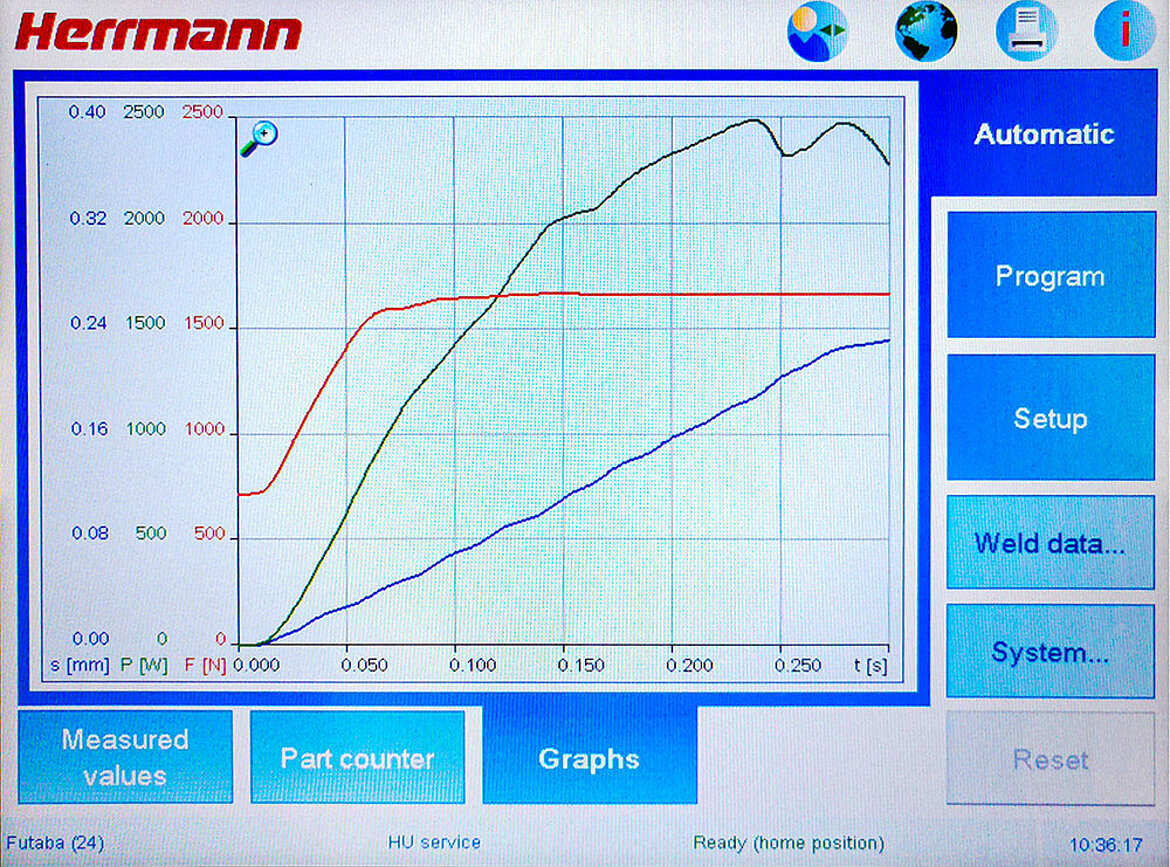
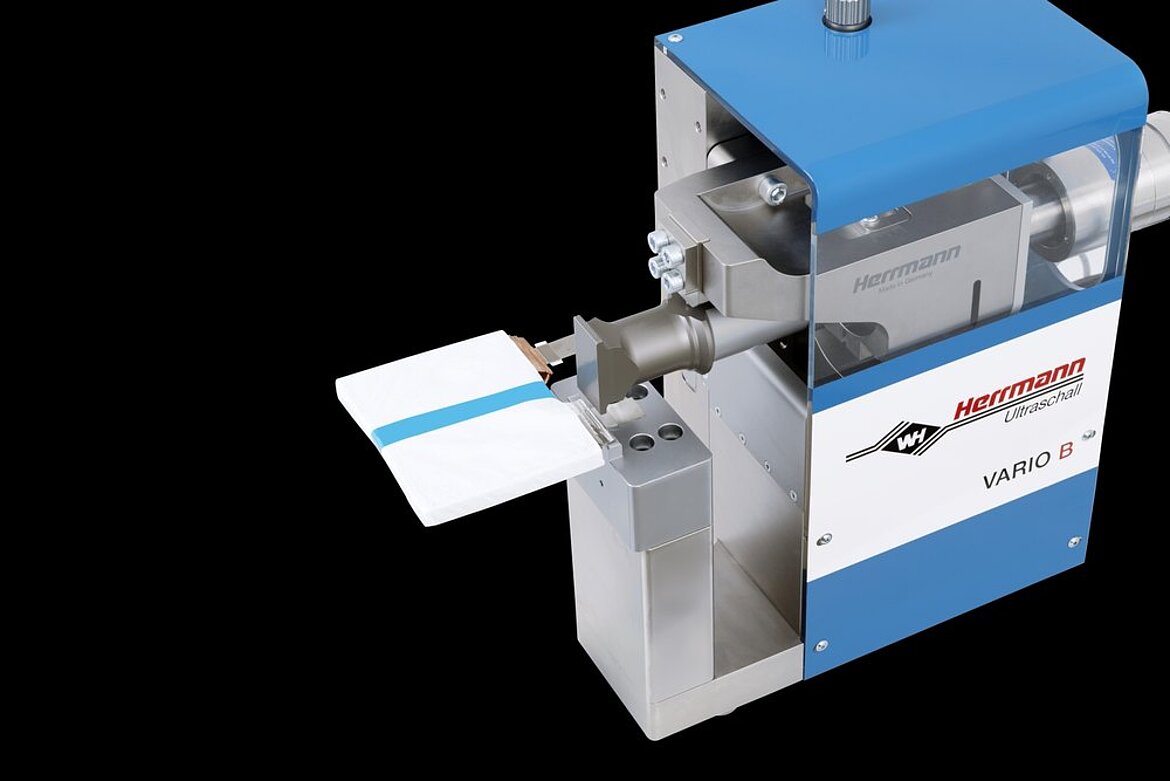