El control de proceso es el factor esencial
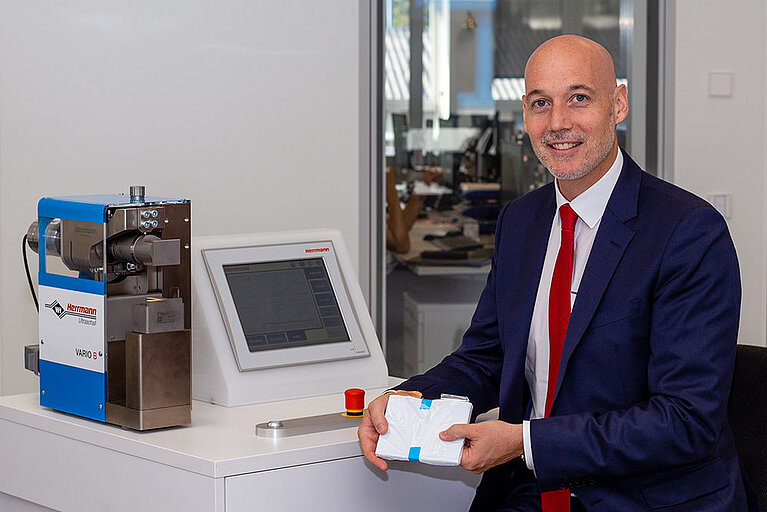
Entrevista con el director general Thomas Herrmann y el director de la unidad de negocios André Deponte
Ustedes, por mucho tiempo, se especializaron en la soldadura de plásticos. ¿Por qué ahora trabajan con metales?
Thomas Herrmann: Las solicitudes de nuestros clientes de la industria de los plásticos, que también necesitan soldar conexiones metálicas, fueron en aumento. Nos dimos cuenta de que podemos aplicar con facilidad nuestras décadas de experiencia en la optimización de procesos al campo de los metales. Además, se está abriendo un mercado potencial completamente nuevo, en especial a causa de la industria de la electromovilidad.
¿Cuáles han sido hasta ahora los “puntos neurálgicos” en la soldadura por ultrasonido de metales no ferrosos?
André Deponte: Con las soluciones existentes, los clientes se quejaban principalmente de la falta de estabilidad de los procesos y del elevado desgaste de las herramientas, porque el metal entra en contacto con metal. No hay amortiguación de las ondas de ultrasonido como ocurre con los plásticos, por lo que el proceso es sumamente abrasivo. Aquí se cumple una regla general: dependiendo del material, el sonotrodo (la herramienta de soldadura que está hecha de acero) se desgasta después de 100 000 disparos y entonces es necesario sustituirlo. Esto equivale a una vida útil de dos semanas. Al considerar los tiempos prolongados que hay que invertir en el cambio de herramienta y en la puesta en marcha, nos damos cuenta de la cantidad de tiempo de producción valioso que se pierde y de los costosos desechos de producción que se generan. Otro factor igual de importante es reducir la generación de partículas. Cuanta menor sea la cantidad de partículas que se formen durante la soldadura, menor será el riesgo de que se produzcan cortocircuitos y mayor será la seguridad de la producción.
Desarrollaron dos máquinas soldadoras para metales. ¿Qué hay de nuevo en ellas?
André Deponte: Desarrollamos aún más nuestra tecnología probada de parametrización y visualización de procesos para atender los “puntos neurálgicos”. Aumentar la precisión con la que podemos controlar el proceso hace que este sea más estable y permite eliminar las partículas. Con ese fin, hemos investigado la correlación que hay entre las cantidades de energía y los tiempos de inactividad. Queremos prolongar la vida útil de las herramientas y, por lo tanto, desarrollamos un sistema de cambio de herramienta que reduce los tiempos de instalación. Nos hemos propuesto reducir considerablemente los tiempos cambio de herramienta previos de hasta 2 horas. Nuestra meta es que sea de 10 minutos, y eso sería un logro revolucionario. Hemos invertido mucho tiempo en diseñar este sistema para asegurarnos de que las máquinas y módulos tengan un diseño más compacto y de que su manejo sea más intuitivo.
¿Cuál es su estrategia para entrar al mercado?
Thomas Herrmann: Estamos presentando dos tipos de máquina. Ambas son soldadoras por puntos. Una la desarrollamos específicamente para aplicaciones de baterías, mientras que la otra es una máquina para soldar uniones cable-borne. Nuestro objetivo expreso es generar valor añadido para nuestros clientes. Comenzamos a hacerlo desde la fase de asesoramiento y abarca el mejoramiento del control de proceso hasta conseguir que el cambio de herramienta sea más rápido y reproducible. Actualmente estamos en la fase de pruebas de campo y nos hemos fijado metas elevadas. Estamos por recibir las especificaciones de nuestros primeros clientes; en cuanto eso ocurra, tendremos todo listo para ponernos en marcha.
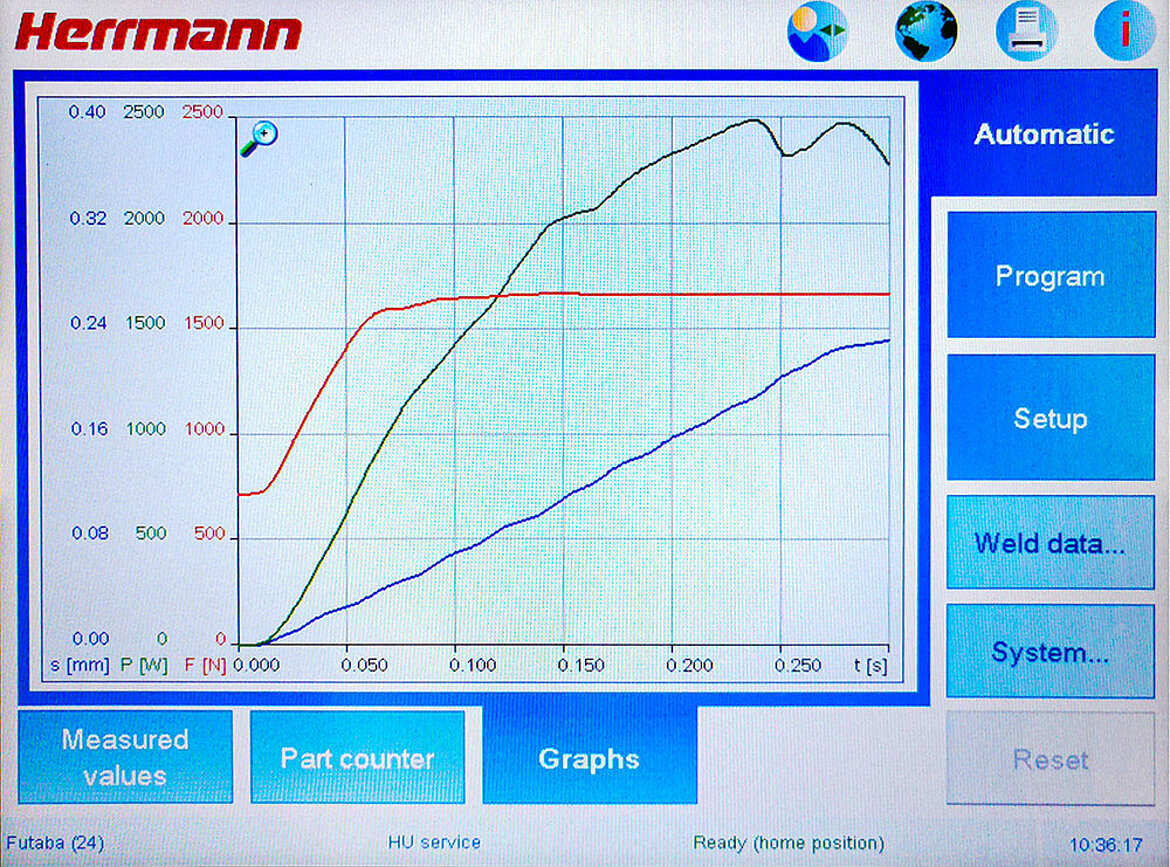
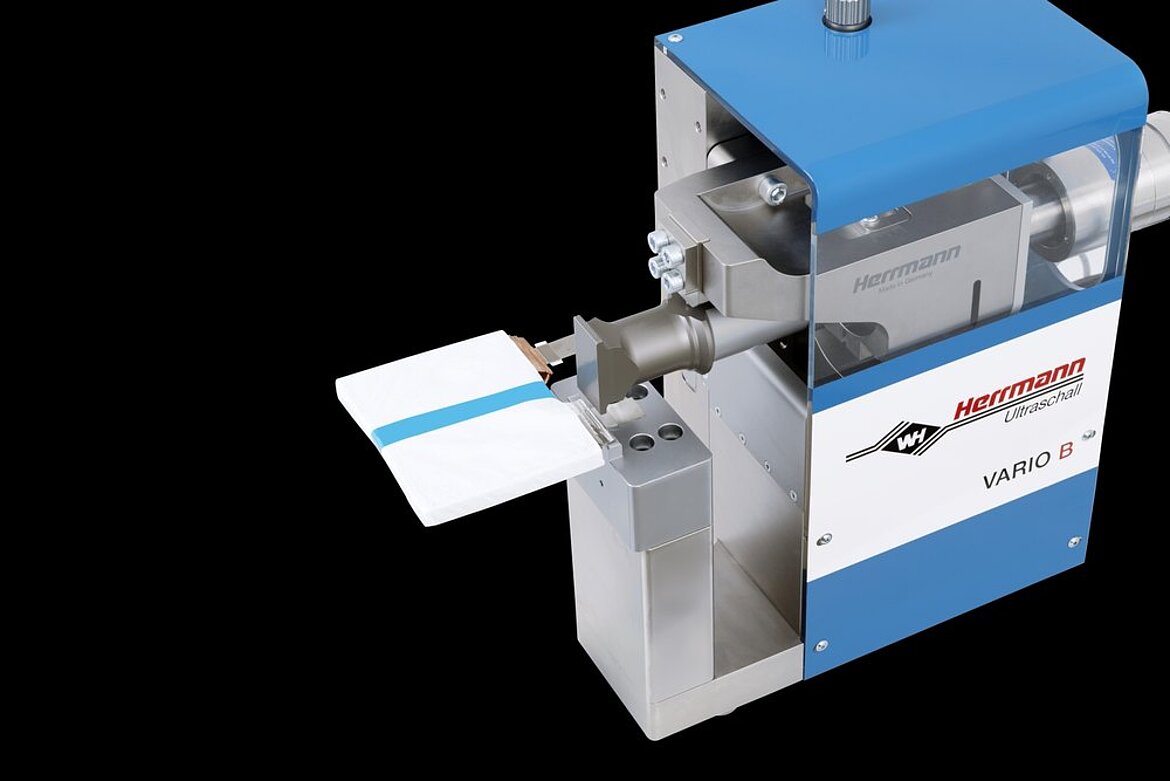