Le contrôle du processus est le facteur essentiel
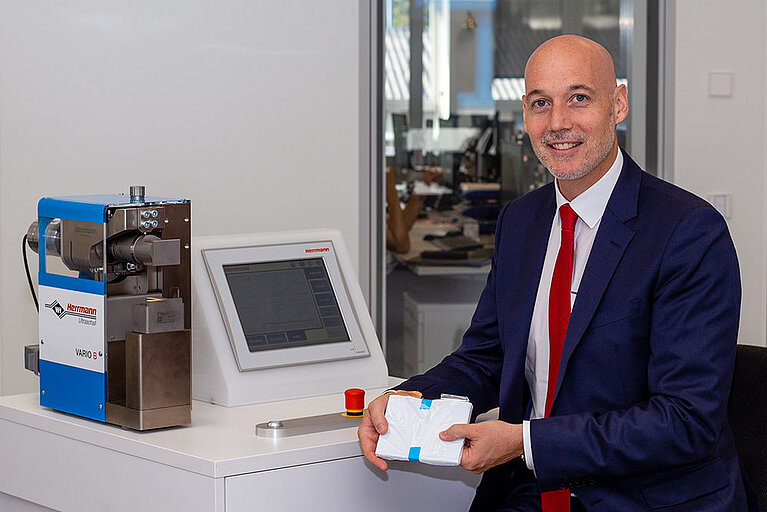
Interview avec Thomas Herrmann, CEO, et André Deponte, Directeur d’unité
Vous êtes un spécialiste du soudage plastique. Pourquoi s’intéresser aux métaux maintenant ?
Thomas Herrmann : Les demandes de nos clients de l’industrie plastique, qui ont également besoin de souder des raccords métalliques, ne cessent d’augmenter. Nous avons réalisé que nous pouvions mettre nos décennies d’expérience dans l’optimisation des procédés à profit dans le domaine des métaux. Par ailleurs, un potentiel de marché entièrement nouveau est en train de s’ouvrir, notamment en raison de la mobilité électrique.
Quels ont été les « points douloureux » jusqu’à présent dans le soudage par ultrasons de métaux non ferreux ?
André Deponte : Avec les solutions existantes, les clients se plaignent principalement du manque de stabilité de procédé et de l’usure élevée des outils, étant donné que du métal entre en contact avec du métal. Les ondes ultrasons ne sont pas amorties comme avec le plastique. Par conséquent, le procédé est hautement abrasif. Une seule règle empirique semble se vérifier : selon le matériau, la sonotrode (outillage de soudage) fabriquée en acier est usée après 100 000 charges et doit être remplacée. Cela correspond à une durée d’utilisation de deux semaines. Si l’on tient compte de la longueur des temps de changement d’outillage et de mise en service, il en résulte la perte d’un temps de production précieux et la génération de déchets de production onéreux. La réduction de la génération de particules est tout aussi importante. Plus la quantité de particules produites pendant le soudage est réduite, plus le risque de courts-circuits sera faible et plus la sécurité de production sera élevée.
Vous avez développé deux machines pour le soudage des métaux. Quelles sont les nouveautés ?
André Deponte : Nous avons perfectionné notre système éprouvé de paramétrage et de visualisation du processus dans l’objectif d’améliorer les « points faibles ». Plus le processus peut être commandé avec précision, plus celui-ci devient stable et exempt de particules. Pour cela, nous avons mené des recherches portant sur la corrélation entre les quantités d’énergie et les temps non productifs. Nous souhaitons augmenter la durée d’utilisation des outils et avons ainsi développé un système de changement d’outillage qui réduit les temps de configuration. Nous aspirons à une réduction drastique des temps de changement d’outillage qui, encore aujourd’hui, peuvent atteindre jusqu’à 2 heures. Notre objectif est fixé à 10 minutes, ce qui serait une véritable révolution. Nous avons investi beaucoup de temps dans la conception afin de garantir un design plus compact des machines et modules, ainsi qu’une manutention plus intuitive.
Quelle est votre stratégie d’entrée sur le marché ?
Thomas Herrmann : Nous lançons deux types de machine, deux appareils dits de soudage par points, avec une machine spécialement développée pour les applications du domaine de la batterie, et une autre destinée aux câbles et terminaux. Nous nous sommes donné pour objectif de générer une valeur ajoutée pour nos clients. Cela commence déjà au cours de la phase de consultation et s’étend jusqu’à un meilleur contrôle de processus, en passant par un changement d’outillage reproductible, plus rapide. Pour le moment, nous en sommes à la phase de test et nous sommes fixé des objectifs élevés. Nous nous apprêtons à recevoir les instructions de nos premiers clients, et ensuite, nous pourrons lancer la machine.
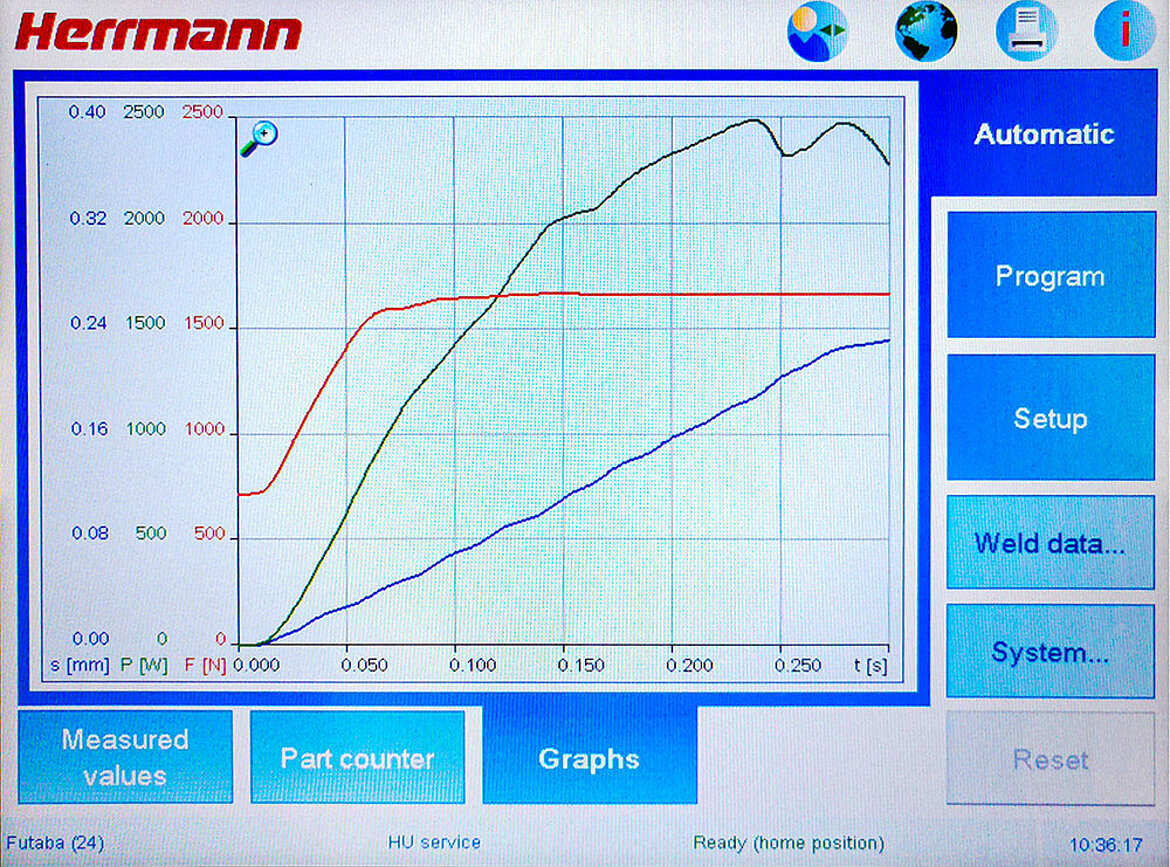
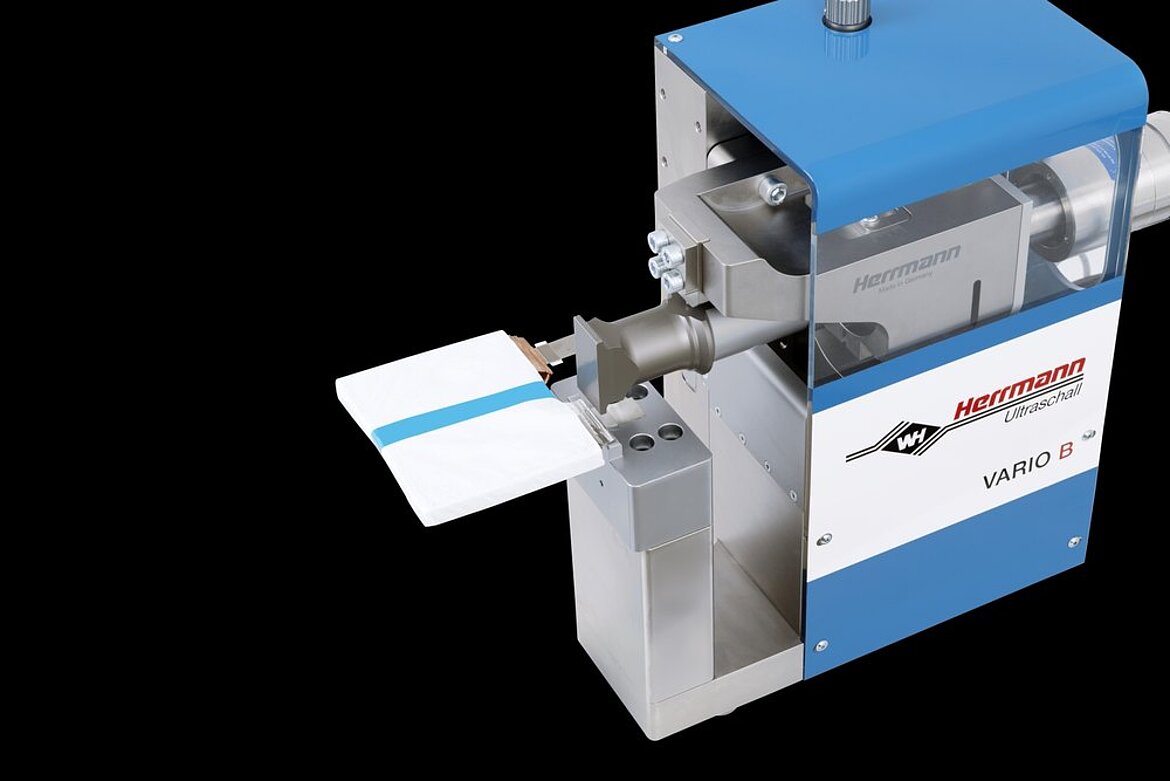