Il controllo del processo è il fattore fondamentale
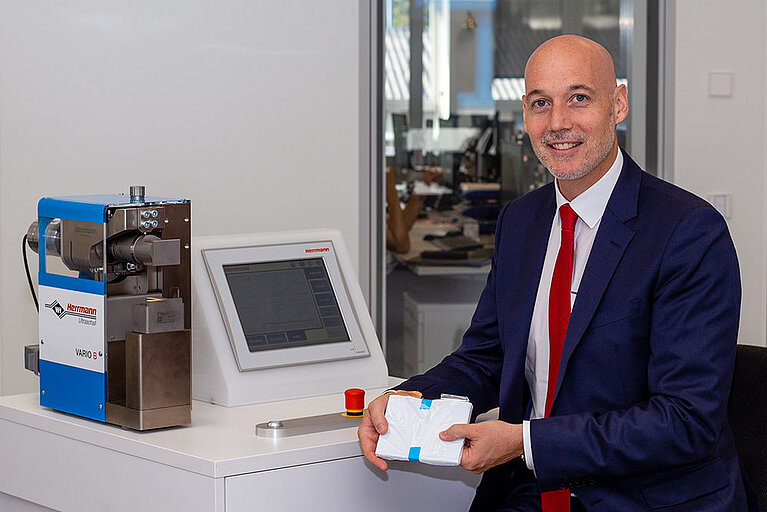
Intervista al CEO Thomas Herrmann e al direttore di divisione André Deponte
L’azienda è specializzata nella saldatura di materiali plastici. Perché dedicarsi ai metalli, ora?
Thomas Herrmann: I nostri clienti del settore dei materiali plastici necessitano di saldare anche connessioni metalliche, e le loro richieste in tal senso sono in costante aumento. Ci siamo resi conto che i nostri decenni di esperienza nell’ottimizzazione dei processi possono essere facilmente applicati al campo dei metalli. Inoltre, sul mercato sta emergendo un potenziale completamente nuovo, soprattutto per via della mobilità elettrica.
Quali sono stati finora i “punti dolenti” della saldatura a ultrasuoni di metalli non ferrosi?
André Deponte: Con le soluzioni esistenti, i clienti principalmente lamentano la mancanza di stabilità dei processi e l’elevata usura degli utensili, perché il metallo entra in contatto con il metallo. In queste applicazioni non si ha lo smorzamento delle onde ultrasoniche che si verifica invece con i materiali plastici, quindi il processo risulta altamente abrasivo. Una regola empirica sembra essere valida: a seconda del materiale, il sonotrodo (l’utensile di saldatura) in acciaio risulta usurato dopo 100.000 colpi. Significa una vita utile di due settimane. Se si considerano i lunghi tempi di sostituzione dell’utensile e di messa in funzione, viene perso prezioso tempo produttivo e si generano costosi scarti di lavorazione. Altrettanto importante è ridurre la formazione di particelle. Meno particelle si generano durante la saldatura, più il rischio di cortocircuiti è ridotto e maggiore è la sicurezza durante la produzione.
Sono state sviluppate due macchine per la saldatura dei metalli. Quali sono le novità?
André Deponte: Abbiamo sviluppato ulteriormente la nostra parametrizzazione e visualizzazione dei processi, già ampiamente collaudata, per porre rimedio ai cosiddetti “punti dolenti”. Più si riesce a controllare il processo in modo accurato, più esso diventa stabile e produce meno particelle. A questo scopo, abbiamo condotto ricerche sulla correlazione tra le quantità di energia e i tempi di fermo macchina. Vogliamo aumentare la vita utile degli utensili e abbiamo quindi sviluppato un sistema di sostituzione degli utensili che riduce i tempi di allestimento. Intendiamo ridurre i precedenti tempi sostituzione dell’utensile, che potevano raggiungere anche le 2 ore, in modo decisamente drastico. Il nostro obiettivo è ridurlo a 10 minuti: sarebbe un risultato davvero rivoluzionario. Abbiamo inoltre investito molto tempo nella progettazione per garantire un design più compatto delle macchine e dei moduli e una gestione più intuitiva.
Qual è la strategia di entrata sul mercato?
Thomas Herrmann: Stiamo lanciando due tipi di macchine, entrambe cosiddette saldatrici a punti. Una appositamente concepita per le applicazioni dell’industria delle batterie, e una per i terminali di cavo. Il nostro obiettivo dichiarato è generare valore aggiunto per i nostri clienti, iniziando già durante la fase di consultazione per poi offrire un migliore controllo del processo grazie a una modalità di sostituzione dell’utensile più rapida e ripetibile. Al momento siamo nella fase dei test sul campo, per i quali ci siamo posti obiettivi ambiziosi. Stiamo per ricevere le specifiche dai primi clienti e siamo pronti per partire.
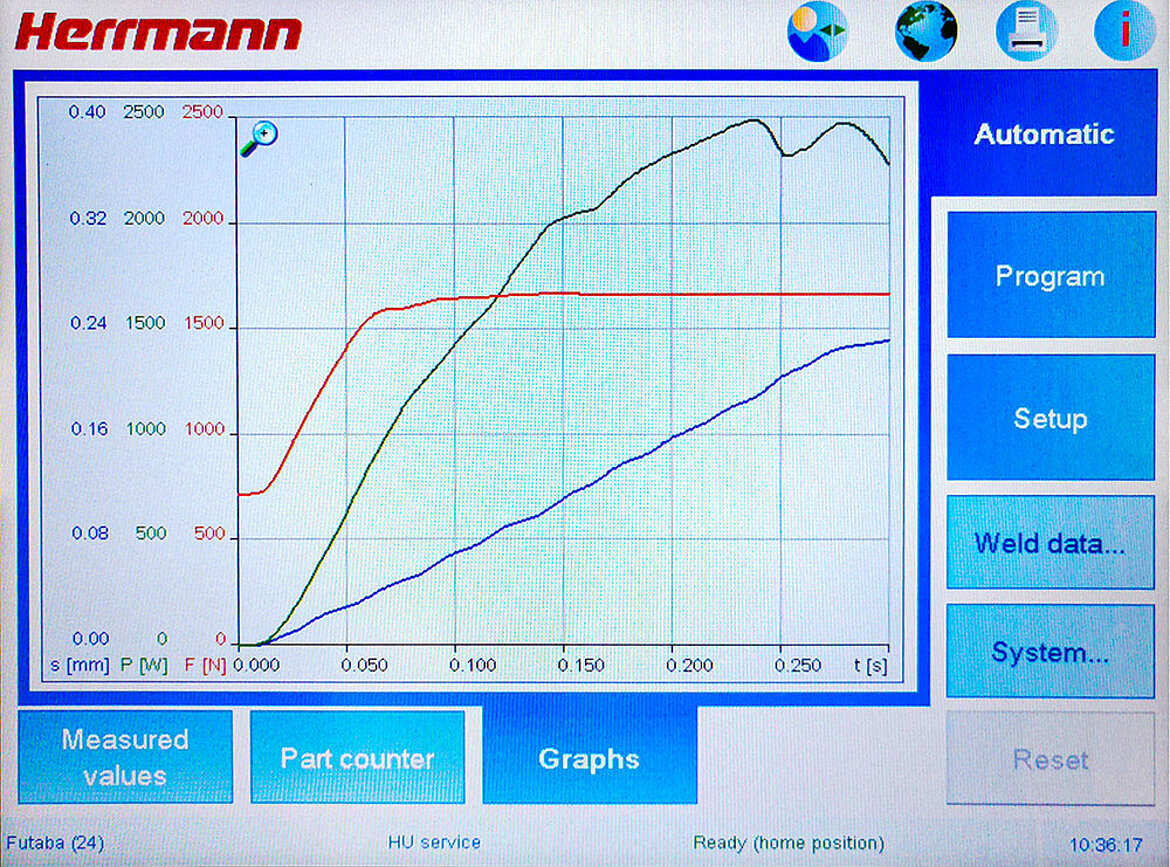
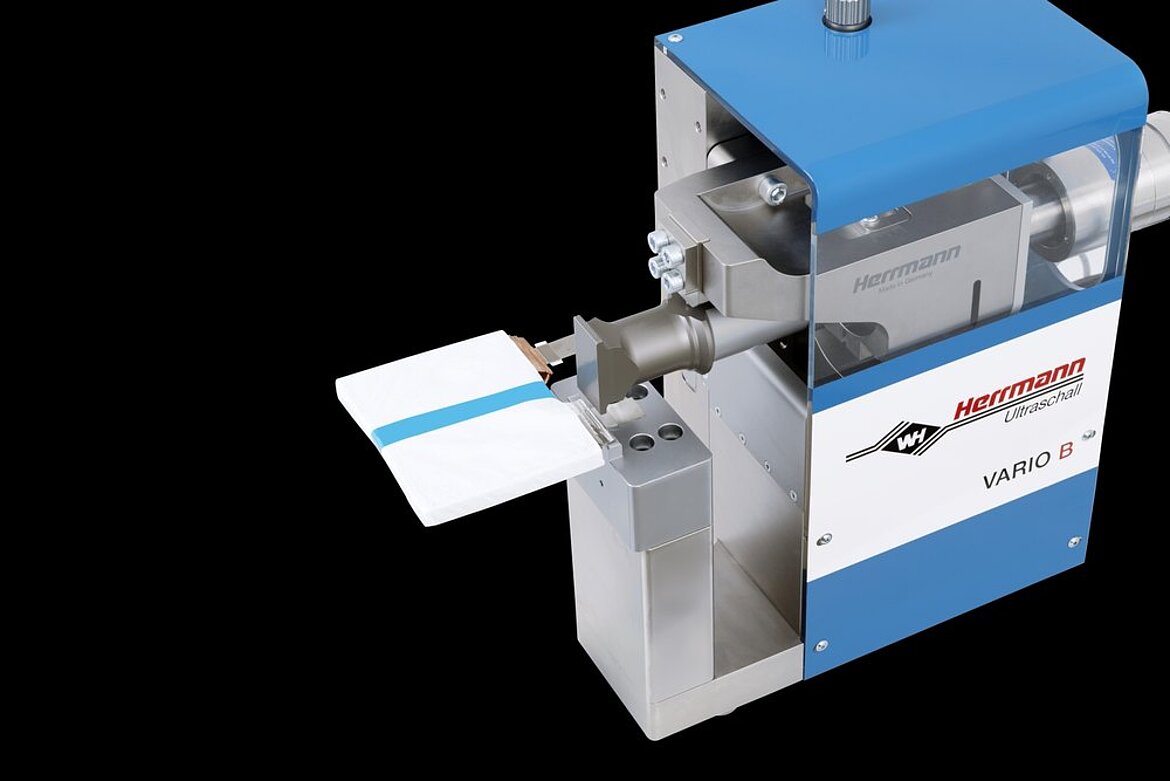