Quand durabilité rime avec baisse des coûts
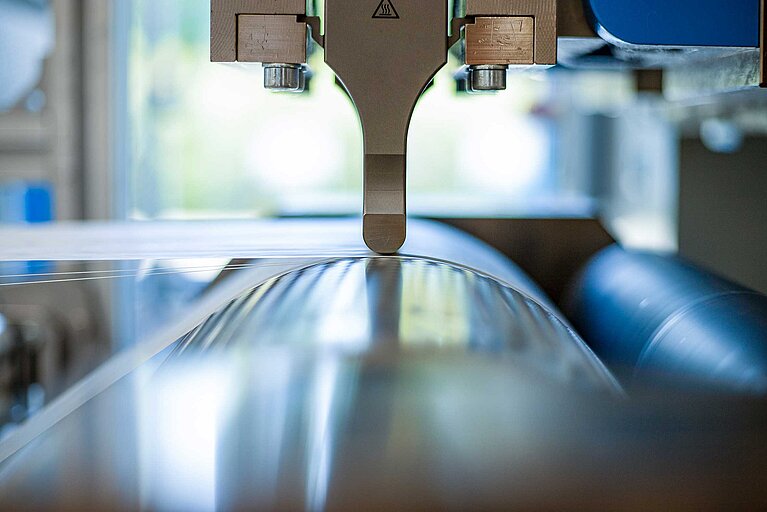
Une toute nouvelle méthode pour fixer les fils élastiques de manière sûre et efficace à l’aide des ultrasons
Afin d’améliorer l’efficacité de la procédure coûteuse de fixation des élastiques dans les non-tissés, Herrmann Ultraschall a développé une technologie innovante : la fixation des fils élastiques à l’aide des ultrasons. Les producteurs bénéficient ainsi d’une méthode à la fois flexible, stable et durable qui améliore l’expérience client tout en réduisant les coûts de production.
Cette technologie de fixation brevetée est basée sur un nouveau type de sonotrode. Grâce à la structure unique de sa surface, cet outil de soudage crée un tunnel entre les couches de non-tissé à travers lequel sont guidés les fils élastiques. Selon l’application, des points de soudure spécifiques sont réalisés en continu ou par intermittence, permettant de fixer les fils dans le non-tissé en ayant uniquement recours aux ultrasons.
Le gros avantage des ultrasons réside en ceci qu’il n’est plus nécessaire d’utiliser des agents d’assemblage supplémentaires pour fixer les fils élastiques. En comparaison des technologies d’assemblage conventionnelles, cette méthode réduit nettement la consommation de ressources et d’énergie et, par conséquent, les coûts de production. La suppression de produits chimiques permet également d’améliorer le toucher des produits, mais aussi leur bilan en termes de développement durable ainsi que leur longévité, l’élasticité des fils étant maintenu sur une plus longue durée.
En même temps, le process ultrasons réduit nettement le risque de rupture des fils, étant donné que les fils élastiques n’entrent pas en contact avec l’outil de soudage pendant la procédure de fixation. Au lieu de cela, ils sont légèrement déformés en raison de la forme spéciale des tunnels créés par la sonotrode, de sorte qu’après la fixation, les frottements de surface au contact entre les filaments et les non-tissés sont augmentés, ce qui améliore leur adhérence.
En comparaison des solutions précédentes basées sur les ultrasons, le guidage des fils par la sonotrode offre des avantages supplémentaires : « Auparavant, il fallait utiliser un rouleau-enclume avec une gravure spéciale pour une application. Le guidage précis des fils était donc onéreux et complexe », explique Dr Raquel Roussel-Garcia, du département Application Development NONWOVENS chez Herrmann. « Grâce à la géométrie révolutionnaire des canaux de guidage dans la sonotrode, nous sommes capables de réaliser plusieurs associations de matières et tailles de produit différentes avec un seul outil. Cela permet de minimiser les coûts d’investissement tout en donnant plus de flexibilité à la procédure. » La sonotrode étant intégrée à un système simple de changement rapide, il est également possible de réduire les frais liés à l’immobilisation et à la maintenance dans la production, a-t-elle ajouté.