08. März 2023
, News
Nachhaltigkeit und Kostenersparnis kombinieren
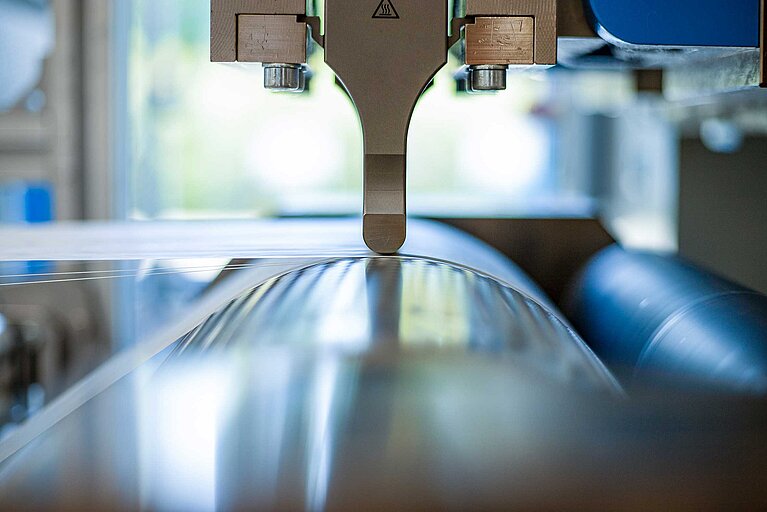
Um den kostspieligen Prozess der Elastikfixierung in Vliesstoffen effizienter zu gestalten, hat die Herrmann Ultraschalltechnik GmbH & Co. KG ein innovatives Verfahren entwickelt: die Verankerung von Elastikfäden mittels Ultraschall. Unternehmen profitieren dabei von einem flexiblen, stabilen und vor allem nachhaltigen Prozess, der dauerhaft die Produktionskosten senkt.
Im Zentrum des patentierten Anker-Verfahrens steht eine neuartigen Sonotrode, die dank einzigartiger Oberflächenstruktur einen Tunnel zwischen den Vliesstoffschichten schafft, durch die die Elastikfäden geführt werden. Je nach Anwendung werden kontinuierlich oder intermittierend spezifischen Schweißpunkten mittels Ultraschall erzeugt, in denen die Fäden im Vliesstoff verankert werden.
Der große Vorteil: Dank des Ultraschalls benötigt die Verankerung von Elastikfäden keine zusätzlichen Fügemittel. Das reduziert gegenüber dem gängigen Klebeverfahren den Ressourcen- und Energieverbrauch signifikant und damit die gesamten Herstellungskosten. Durch den Wegfall der Chemikalien verbessern sich zudem die Haptik, die Nachhaltigkeitsbilanz der Produkte sowie ihre Haltbarkeit, da die Elastizität der Fäden länger erhalten bleibt.
Gleichzeitig reduziert das Verfahren das Risiko für Fadenabriss signifikant, da die Elastikfäden während des gesamten Prozesses nicht mit dem Schweißwerkzeug in Kontakt kommen. Stattdessen werden sie durch die spezielle Form der von der Sonotrode erzeugten Tunnel leicht verformt, sodass sich nach der Verankerung die Oberflächenreibung zwischen den Fäden und den Vliesstoffen erhöht und sich dadurch ihre Haftung verbessert.
Gegenüber vorherigen Lösungen, die auf Ultraschall setzten, bietet die Fadenführung über die Sonotrode ebenfalls entscheidende Vorteile: „Bislang benötige man eine speziell für eine Anwendung gravierte Ambosswalze, was eine exakte Fadenführung kostspielig und komplex machte“, erklärt Dr. Raquel Roussel-Garcia, Application Development NONWOVENS bei Herrmann. „Dank der innovativen Geometrie der Führungskanäle können wir mit einer einzigen Sonotrode viele verschiedene Materialkombinationen und Produktgrößen umsetzen. Damit minimieren Investitionskosten und gestalten den Prozess deutlich flexibler.“ Da die Sonotrode Teil eines einfachen Schnellwechselsystems sei, könne man auch die Stillstandzeiten und Wartungskosten in der Produktion reduzieren.